The fourth industrial revolution has impacted the steel industry from all sides, from production processes to value chain and competition. Steel has been evolving since the first industrial revolution, which brought with it steam engines, moving into electricity and conveyor belts in the second revolution, to the third industrial revolution and its personal computers and internet access.
The fourth industrial revolution is heralded by big data, the internet of things, artificial intelligence, virtual reality and augmented reality, 3D printing and other technological innovations. It’s happening at rapid speed. The steel industry needs to keep up and take advantage of all that this revolution has to offer.
However, the industrial revolution did not happen overnight, and advancements in human development traces back to the Iron Age.
The Iron Age and How it Impacted Civilization
After the Bronze Age was the Iron Age. People started using iron and steel for tools. This was a huge shift for the world, and helped improve nearly all spheres of life from the spread of written language to more effective agricultural practices. Iron offered more choice. People could forge this material into whatever they needed for tools, weapons, or ornaments and decor.
Tools and weapons created during this era often used steel, which was a vast improvement on the bronze items from the previous age. Items made from steel were just as light as bronze, but stronger, so users were able to get more out of each item they created. The strength of these tools made it possible for farmers to plant and harvest more land, faster. It enabled people to sell or trade for livelihood.
The Iron Age is a great example of how the right materials can make life better for everyone.
The New Structure of Steel
As the world moves through the fourth industrial revolution, it is evident the same thing is happening. Instead of improvements in specific materials and tools, however, technology is changing things.
The steel production process can be completed autonomously if the fourth industrial revolution continues the way it is going. This means that manufacturers will be able to have very detailed and thorough control over production, using smart technology that will factor in every element from the surrounding environment to minute details of the material itself. The steel production process will be able to use real-time data to optimize every facet of operations, saving money and time.
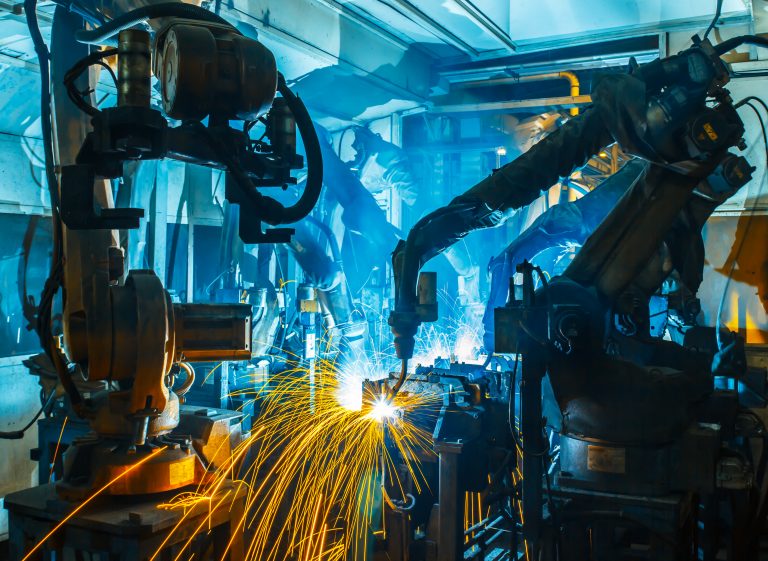
Robot arms with artificial intelligence take part in the steel production process. (Source: Telenor Connexion)
The steel value chain is affected by changes in the provision of after-sales service, owing to new technology. Manufacturers can use smart technology to track how users interact with their completed products and offer better customer service as a result.
Again, real-time information comes into play, allowing steel companies to see exactly how orders are being created, fulfilled and used, as it is happening. Customer needs are met with ease and speed, all tracked and analyzed digitally.
Competition in the steel industry will be affected by this revolution, too. Competitors can see how other companies are using big data and automation to save money and offer a better customer experience, and use those details to revolutionize their offerings. Online steel transaction platforms make this transparency even more accessible, for companies and clients alike.
Implications on the Steel Industry
To keep up with this revolution, and make the most of it, steel companies need to understand the implications on the industry and plan for the future. New technology is only going to become more widespread, more common, and more advanced. Companies need to be ready to react.
Integrating technology and smart software is the ideal way for steel companies, and the industry at large, to take advantage of this new revolution and use it to create better products and better customer relationships.
To get an idea of how to best integrate new tech into existing steel practices, POSCO’s smart steel factory is a prime example, currently being tested at the Gwangyang Steel Mill. POSCO’s smart factories will collect and analyze all of the microdata generated in the steel production process, to determine the cause of every event that impacts quality or production in general.
From facilities to energy and environment, to safety and conditions, the smart factory will monitor everything. And it will respond accordingly to make the best quality steel possible.
Self-learning artificial intelligence ensures that the process of steelmaking is carefully controlled, with adjustments made in real-time to directly and positively impact the result. The smart factories will use technology to fill the gaps where human capabilities are simply no match for software.
The world has come a long way since the Iron Age and through the various industrial revolutions. In the current fourth industrial revolution, steel companies have to take advantage of new technology and innovations by figuring out ways to apply them to steelmaking processes. POSCO has made this a top priority as it continues to research, educate and implement smart technologies to its production processes and materials and will lead the way for steel companies to follow through the fourth industrial revolution.
Cover photo courtesy of Manufacturing Global.
- 4th industrial revolution
- artificial intelligence
- civilization
- current iron age
- customer
- environment
- Fourth Industrial Revolution
- industrial
- Industrial Revolution
- internet of things
- iron
- Iron Age
- iron age 2.0
- manufacturing global
- material
- POSCO
- posco smart factory
- robot arm
- Smart Factory
- Smart Industry
- smart technology
- steel companies
- steel industry
- steel production
- steel production process
- steelmaking
- tools