Stainless steel is one of the most common types of steel used today, from kitchen appliances to construction and pipelines. Its non-corrosive, high-strength and 100 percent recyclable properties make stainless steel the go-to material for manufacturers across all industries.
It is also the most common material found in medical supplies that contribute to people’s health and safety on a daily basis.
Surgical Steel
“Surgical steel” is a term used to describe stainless steels for medical applications, and are generally made up of 316, 440 and 420 stainless steels. Surgical stainless steels are corrosion resistant, have a shiny, aesthetically pleasing exterior and are extremely hygienic. Plus, they have a long life cycle and require minimal maintenance.
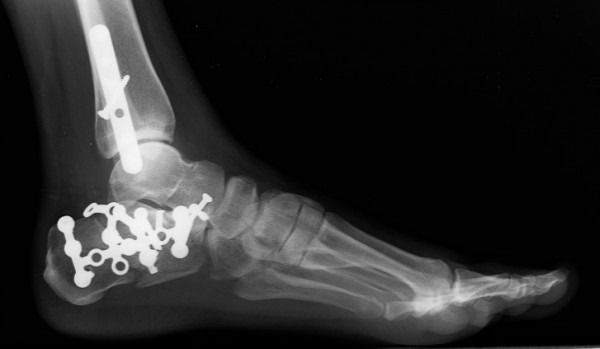
Surgical steel is also used for screws and joints that hold bones together. (Source: National Geographic)
Due to these properties, surgical steel is the material found in medical equipment such as syringes, scalpels and gauges. Moreover, screws used to hold broken bones together and other parts for application inside the body are made of surgical stainless steel.
For the same reasons, surgical steel is also used to make jewelry.
Know anyone who is allergic to certain types of jewelry? Often times people think they are allergic to gold or silver, but chances are, they are allergic to other alloying elements, the most common one being nickel. In the United States, up to 17 percent of women and 3 percent of men are allergic to nickel, and the number is rising. Surgical steel with zero nickel content is a safe and cost-friendly alternative, and demand for the hypoallergenic material is growing.
Surgical steel was a part of the 45.8 million metric tons of stainless steel produced globally in 2016, almost double the 24.5 million metric tons produced in 2005. The growing demand and application of stainless steel are playing a positive role in the economy, but it has also been the cause of environmental pollution.
POSCO’s Surgical Steel
One of POSCO’s surgical stainless steels is the PossRB1. It is comparable to the 420J2 stainless steel that is often applied to kitchen blades, however, it has a much higher level of hardness, and thus can be applied to surgical scalpels and razor blades.
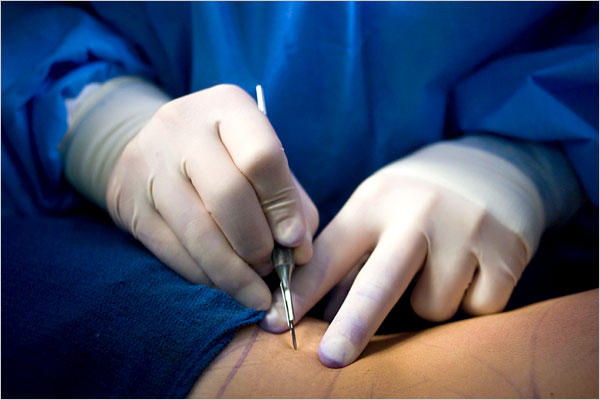
Surgical scalpels come in direct contact with the body and need to be especially clean and non-corrosive. (Source: NY Times)
Another example is POSCO’s 304i stainless steel used to make syringe needles. It is an upgraded version of 304 stainless steel with a 9 percent nickel content, traditionally applied to syringe needles. The production process of syringe needles is demanding and require multiple steps to process into the desired thinness and diameter. To add, the materials need to be especially clean, or else the needle can fracture or not reach the desired thinness. POSCO’s 304i stainless steel is manufactured using POSCO’s strip casting technology and can be processed into the thinnest diameter requirements for 32 gauge needles (dental needles).
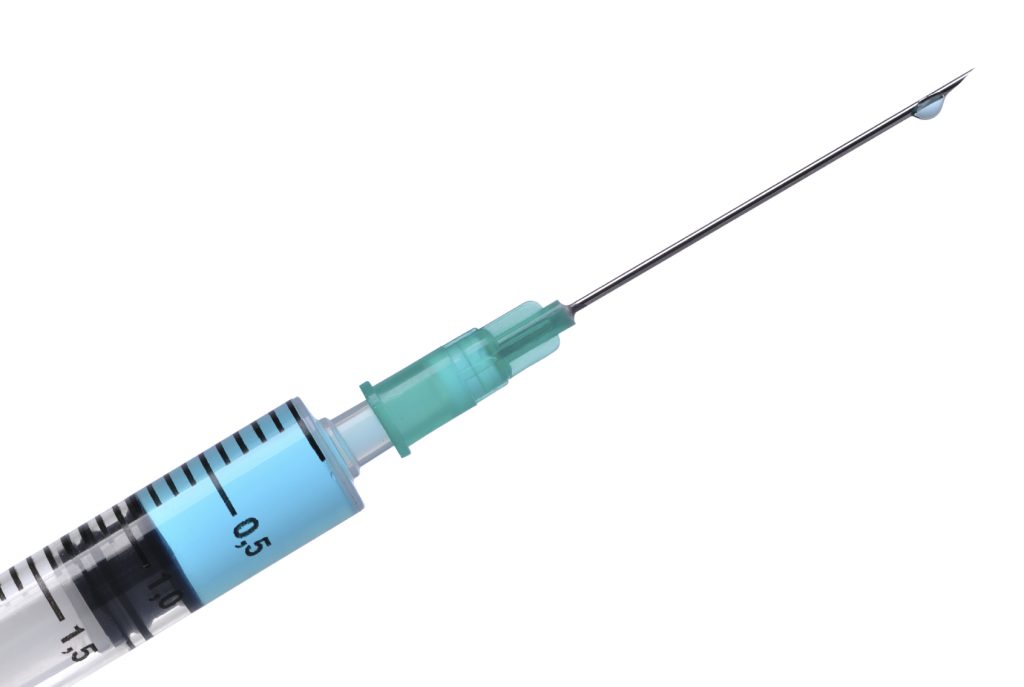
Syringe needles require a demanding production process. (Source: Tangent Industries)
POSCO’s poStrip Technology for Stainless Steel Production
In order to reduce the harmful environmental effects of steelmaking on the environment, POSCO partnered with the Research Institute of Industrial Science & Technology (RIST) in 1989, to come up with an innovative technology for stainless steel production called poStrip, or POSCO’s strip casting technology.
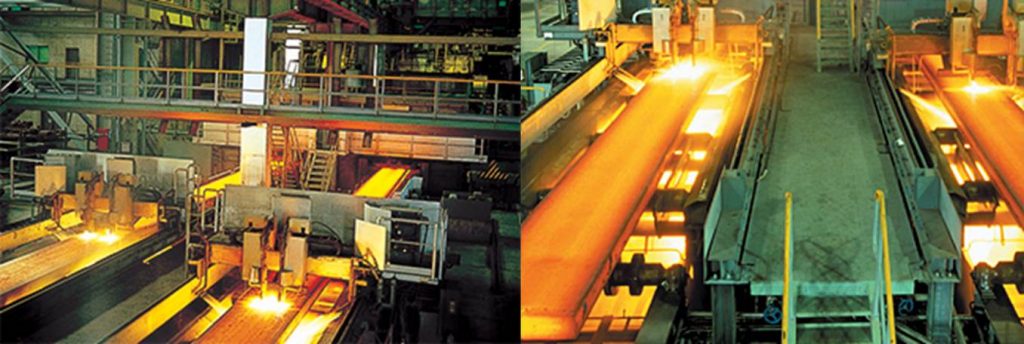
The poStrip technology is an innovative way to make steel production more sustainable. (Source: POSCO E&C)
For more than 13 years, POSCO and RIST experimented with a twin-roll strip casting system where thin strips of steel can be produced in a single, continuous process. Hot molten steel passes through two cylindrical rollers that rotate and cool the hot steel sheets immediately, thus eliminating the need for hot rolling. In conventional casting processes, molten iron is poured into molding frames to produce steel slabs that are then rolled into sheets.
The new technology vastly reduced the cost of production, delivery time as well as the amount of harmful emissions created in the steelmaking process. In the end, POSCO’s poStrip technology was perfected and applied to various types and grades of POSCO’s stainless steels.
Not only is the innovative technology cost-effective and sustainable, it produces better quality steels.
In 2015, POSCO received the Steelie Award for Innovation of the year from the World Steel Association. POSCO was recognized for its high-quality stainless steel products that were produced with the innovative strip-casting production technology. POSCO will continue to research and improve the production and overall quality of stainless steels so that its partners can manufacture world-premium supplies, machines and architecture.
- bio material
- bio steel
- blades
- casting technology
- environment
- innovation of the year
- material
- medical appliances
- medical steel
- piercing
- POSCO
- posco 304i stainless steel
- POSCO E&C
- posco postrip
- posco postrip technology
- posco rist
- posco stainless steel
- posco steelie award
- poscos surgical steel
- possRB1
- poStrip
- postrip stainless steel
- postrip technology
- razor blade
- research institute of industrial science and technology
- RIST
- stainless steel
- steel appliances
- steel joints
- steel production
- steelie award
- steelmaking process
- surgery
- surgery appliances
- surgery material
- surgery steel
- surgical
- surgical material
- surgical scalpels
- surgical stainless steel
- Surgical Steel
- sustainable
- syringe needle steel
- syringe needles
- World Steel Association
- WSA