In the three-part ‘Blast Anatomy’ series, POSCO Newsroom is exploring everything there is to know about the essential and yet so mysterious, blast furnace. In Blast Anatomy #1, we sliced the blast furnace in half to figure out how it makes molten iron. In Blast Anatomy #2, we observed POSCO’s smart blast furnace to understand how it gets smarter every day through deep learning.
Now the ‘FE Odyssey: “I Am a ButterFEly.”’, the final installation of the Blast Anatomy series, will follow the iron (FE) through its journey – all the way from its birthplace in mine to its final destinations, right around us. Better yet, the FE itself will walk us through the entire adventure!
Like a majestic butterfly who muddles through arduous stages – eggs, caterpillars then pupa – the journey of steel is just as rigorous: from iron ore buried deep in the mines until it finally presents its true self, as steel.
Join now to follow the FE Odyssey. POSCO Newsroom presents: “Blast Furnace Anatomy #3 – FE Odyssey: “I Am a ButterFEly.”
l Into the World – Like a Butterfly Fighting Its Way out of the Egg,
Iron Ore Makes Its Way out of the Mine
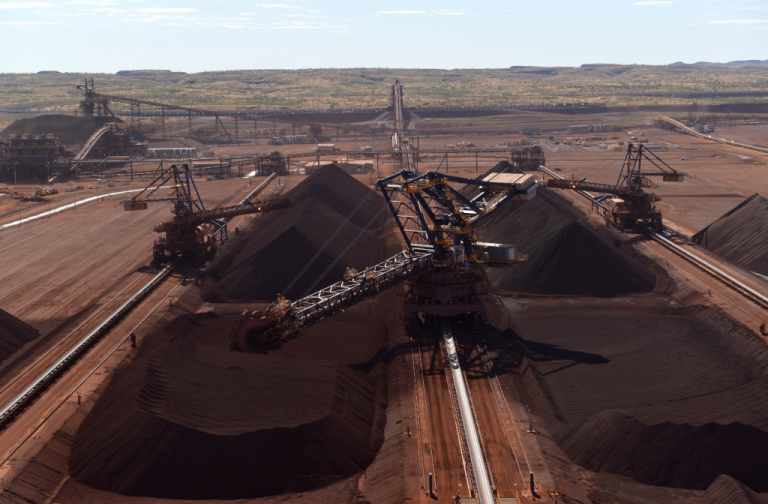
▲ Roy Hill Mine, Western Australia
I was born in Roy Hill mine in Western Australia, over 6,500 kilometers away from Pohang where one of POSCO steelworks is located. While buried deep in the ground of Roy Hill, I always dreamed of transforming into cool and chic steel products – a sturdy car, a slick home electronics, or a shiny stainless travel mug that offers people warm beverages.
Roy Hill mine has a total of 2.3 billion tons of iron ore deposits. POSCO started investing in Roy Hill mining project since 2010 now holding 12.5% of its shares. Roy Hill boasts the annual production of 55 million tons of iron ores. It’s huge! And that’s how so many of my siblings come from there. Besides Roy Hill, my other iron ore siblings also come from places like Canada and Brazil.
From the mine, do I travel straight to steelworks? Not exactly. I wish it were that simple. Before I get transported to the port in Australia, I make a stop at a laboratory for thorough testing – all my internal organs undergo rigorous testing. Using magnets, the lab technicians classify ores with high iron (FE) content. Fortunately, the iron ore that housed me passed the inspection, and I headed to the harbor so I can be sent to Korea.
My siblings and I boarded the transport ships to Korea. After 15 days of a long journey across the ocean, I can hardly forget the excitement I felt when we finally docked. Here we were, at the pier for POSCO’s raw materials, and I was stepping closer to my dream. Every year, 55 million tons of iron ores reach the POSCO docks – both Pohang and Gwangyang combined! These iron ores all share one dream and one dream only – the dream of becoming steel.
After we disembarked from the ship, we got stacked in raw materials yard. The raw material yards at POSCO steelworks measure to be 1.85 million m² – both Pohang and Gwangyang combined.* In that vast field of POSCO yard, I met some new friends – some were called ‘coal.’ Later on, when we reunited in front of the blast furnace, the coal friends would stand before me already transformed as ‘coke.’ Because coal could produce acidic dust, they would first travel to a place called ‘silo,’ an eco-friendly storage facility specifically designated for them.
*The Seoul World Cup Park: 2.1 million m².
When I looked closely, I noticed my iron ore siblings all had very different body types. We were all jagged and uneven. So we got separated, tossed and rolled around a lot, so our bodies can be shaped just right for the furnace. It was a lot of work, but I was so psyched – I knew I would soon get to travel into the blast furnace!
l Rites of Passage for Butterflies, So for the Iron Ores
As it turns out, I knew nothing of what it took to become steel. From the raw materials yard, I thought I would head straight into the blast furnace. Little did I know that I had to undergo one last stage – a process called ‘sintering.’ I also went through several other processes and entered a hot oven. As I got baked in it, I got more polished and solid. It was 1,300℃, so it was super hot, but I heard it’d be even hotter inside a blast furnace, so I got through it okay. After sintering, I transformed into sinter, a raw material for steelmaking, not an ugly and unpolished iron ore anymore!
As sinter, I passed through three filters, and right in front of the rotation chute, I reunited with the friends I’ve met earlier at POSCO yard. We would enter the blast furnace together. Through the rotation chute, we twirled and rolled around, a lot.
I heard some of my friends didn’t quite make it to the rotation chute. They didn’t pass through the filtering stages earlier. But I heard they were going to be reused as raw materials for the sintering instead.
I entered the furnace as sinter, but there were other raw materials like ‘sized lump’ and ‘pellet’. The sized lump came in just the perfect size right from the extraction. Relatively small iron ores became pellets through compressing and molding. Subsidiary materials like limestones also entered the furnace with me. Of course, the crucial fuel friends like coke, who help us melt, also joined us.
Facing the blast furnace, I got so nervous, so I took a deep breath to calm myself down. Because the temperature inside the furnace could reach as high as 2,300℃, it was rather hard to breathe, but my coke friend and I patiently took turns forming layers inside the furnace. As time went on, we traveled down. As we traveled down, we could feel the hot air flying up. Along with the hot air, I flew up in the middle of the furnace. I wasn’t quite sure where I would go next. Meanwhile, I heard my coke friend shouting, “hot air slapping!”
The coke hot aired by 1,200℃ air from the bottom, was oxidized producing carbon monoxide as a result. In turn, this carbon monoxide took oxygen away from me. These series of chemical reactions separated me from oxygen, and I became pure iron, FE! I finally transformed into molten iron and dropped to the floor. Along with my siblings, I roared in victory and exited the furnace through the tap hole.
l How Molten Iron Becomes Steel
I became molten iron, but the excitement was short-lived. To become steel, I have yet to face another set of journeys. As is, right out of the furnace, I was called ‘pig iron’ still containing several impurities like carbon, phosphorus, and sulfur. I still had to go through several processes inside the steelworks to reborn as a slick and beautiful steel product. The processes to come were: steelmaking, casting and rolling.
POSCO’s Pohang and Gwangyang Steelworks are integrated steelworks – because they have all the facilities to turn something like me, a piece of iron ore rock, into perfect and complete steel – all in one place. Let me walk you through each step.
Step 01. Steelmaking process – removing impurities from molten iron, molten iron becomes molten steel at this stage.
To become steel, I still had to shed impurities completely, and my carbon proportion had to be adjusted also. As pig iron, I exited the furnace through the tap hole and got loaded onto the ‘Torpedo Ladle Car’ and transported to the converter.
At this stage, the steelworks workers called me ‘molten iron,’ which meant pig iron made in the blast furnace. The torpedo ladle car is a specially designed car that transports molten iron. Each car, which can load up to 300 tons of molten iron, heads to the converter. Once I got to the converter, I saw scrap metals as well as pure oxygen. The carbon inside me became oxidized, and its proportion was reduced down to 0.3%. At this stage, I became independent from all the unnecessary impurities. Through this steelmaking process, I became molten steel – pure and optimized pre-steel. I wasn’t yet complete but was a ‘steel’ nonetheless, finally!
Step 02. Casting process – where the liquidated steel becomes solid.
As molten steel, I went into a mold, and through the continuous casting process, I got cooled and solidified to become intermediary materials like slab, bloom, and billet. It’s like shaping cookie dough with cookie cutters of various shapes and sizes. Slabs are used for plates or hot rolled coil; blooms for large steel bars or wire rods; and billets are made into small steel bars or wire rods.
Step 03. Rolling process – making steel into plates or wire rods.
After casting, slab, bloom, and billet pass through several rotating rolls taking a series of constant pressure. During this process, I either get thinned out or get stretched as per the client order – in whatever thickness or length. This is the stage where I can finally become wire rods, plates, or coils.
After the rolling process was complete, I underwent yet another rounds of check-ups to see if I had all the adequate qualifications as a steel product. At this stage, I even received an identification tag! I still remember myself waiting in the storage room excited to leave for the next destination. Some of my siblings got on a ship to the United States, and some of my big siblings got transported to the port in Ulsan in a specially designed truck.
l Like Butterflies Flying All Around the World, Steel Travels and Is Everywhere
To become an adult, butterflies must undergo long and arduous journey – first fighting its way out of the eggs, and going through caterpillar and chrysalis stages. Just like butterflies, I was merely a piece of rock at birth. Then, I became sinter, then a pure ‘FE,’ then finally, steel.
My dream came true. I became advanced high-strength steel (AHSS) and got used in a car, in hydrogen batteries – also in refrigerators and washing machines! Some of me became a bridge that crosses over an ocean. I was reborn as indispensable products in people’s lives.
And I don’t just mean me in contemporary society. Even my ancestors played crucial roles in sparking Industrial Revolution and in accelerating modernization. It’s a well-known fact the Industrial Revolution kicked off right around when the steam engine started being used as the main energy source. Simultaneously, the advanced smelting technique during the eighteenth century helped replace wood railways with iron railways. Together with the steam engine, trains became another momentum pushing the Industrial Revolution forward. Even after the Industrial Revolution, I was used everywhere as construction materials, in the machinery, for ships, cars, and home electronics. I was present all throughout human history.
I go on quietly carrying out my duties whether people notice me or not. I am hiding in guitar and piano strings creating beautiful melodies – and even in ticking clocks and car tires. Have you ever noticed my presence?
Like a caterpillar who turned into beautiful butterflies, I, who was once an unpolished piece of rock is now traveling all around the world in different shapes and sizes. Look around! You will notice I’m everywhere – and right next to you, at this moment.