Twenty years ago, Toyota debuted the first mass-produced hybrid vehicle, but today almost every major car manufacturer has a hybrid or electric car on the production line. Just last week, Tesla surpassed Ford and GM to become the most valuable car maker in the US, signaling to the auto industry that investors are serious about banking on the future of electric vehicles.
Several factors are contributing to the growing interest in electric vehicles. Stricter CO2 emission standards are changing the way cars are being made, and consumers are becoming more environmentally conscious at the same time. To produce more fuel efficient vehicles, car makers are looking to advanced materials in lightweighting that can help make vehicles more eco-friendly while being safe and affordable.
The Push to Reduce Carbon Emissions
In the US, the transportation sector produces nearly 30 percent of all global warming emissions, and more than half of those emissions come from passenger vehicles. Between 1990 and 2004, the average fuel economy of new vehicles actually decreased, but since 2005 those numbers have begun to improve, resulting in less greenhouse emissions (see chart below).
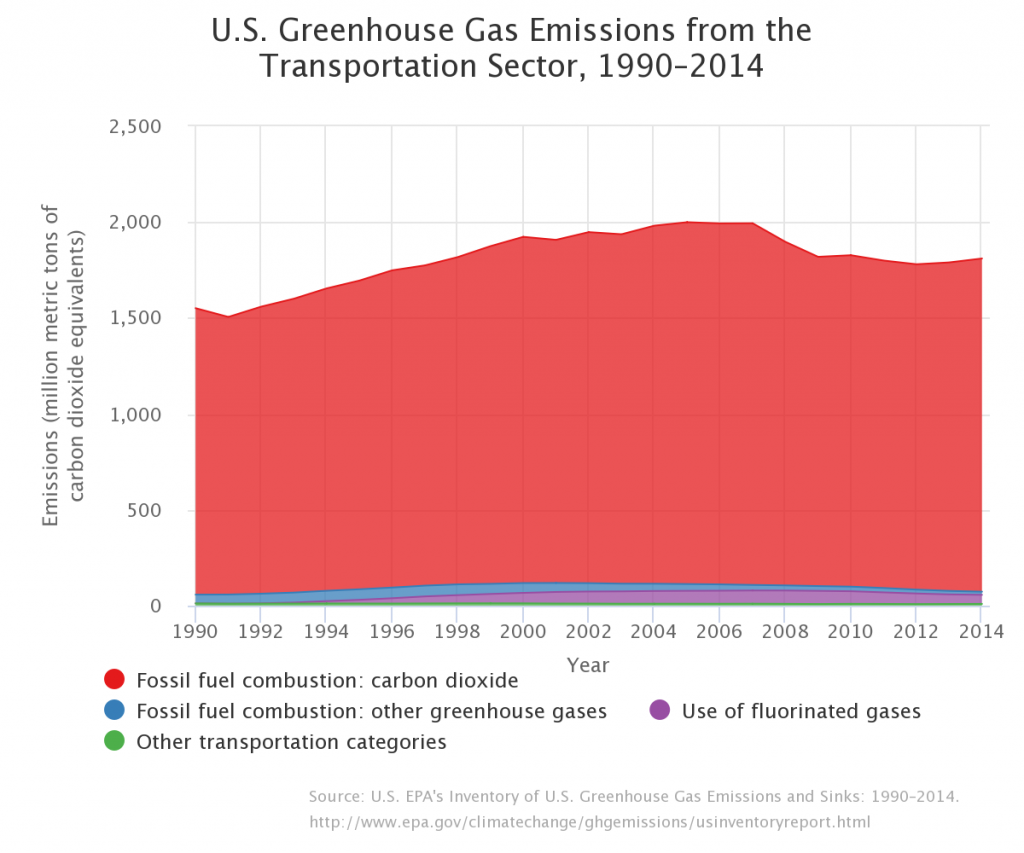
Greenhouse gas emissions from the transportation sector remain high but have gone down in recent years. Increased efforts by the auto industry to produce more fuel-efficient cars is helping this trend. (Source: EPA Inventory of US Greenhouse Gas Emissions and Sinks: 1990-2014)
As air pollution gets worse and global temperatures continue to rise, governments, consumers, and car manufacturers have all seen the urgency in creating more fuel-efficient vehicles. However, in order to build electric vehicles, hybrid cars, and even more fuel efficient combustion engine autos, new materials and production methods must be used. Specifically, cars need to be lighter.
Reducing Weight, Reducing CO2 Emissions
The heavier a car is, the more fuel is required to move it. A study from MIT found that for each 100-kg reduction in a car’s body weight, fuel consumption could decrease by about 0.3 L/100 km for cars and about 0.4 L/100 km for light trucks. This not only translates into fewer CO2 emissions but also into cost savings for consumers. The following table provides estimated fuel cost savings for a range of weight reductions. Today’s cars and light trucks weigh between 1,000 to 3,800 kg.
Estimated Fuel Cost Savings |
||
Weight reduction | Estimated fuel cost savings over 200,000 km – cars | Estimated fuel cost savings over 200,000 km – light trucks |
10 kg | $65 | $87 |
25 kg | $164 | $218 |
50 kg | $327 | $436 |
100 kg | $654 | $872 |
200 kg | $1,308 | $1,744 |
400 kg | $2,616 | $3,488 |
1,000 kg | $6,540 | $8,720 |
Note: For illustrative purposes, savings are based on a fuel price of $1,09/L and the average fuel consumption and weight relationship reported by MIT.
[Source: Savings are based on a fuel price of $1.09/L and the average fuel consumption and weight relationship reported by MIT.] |
Manufacturers have been testing new materials to use in their cars in order to make the weight reductions necessary for a viable EV. Utilization of alternative materials like aluminum, magnesium, and carbon fiber components are increasing due to their lightweight properties. However, additional financial and environmental costs remain high.
In the past, in order to make steel lighter, sacrifices had to be made in strength and ductility. However, recent innovations in advanced high-strength steels (AHSS) have been able to bridge that gap. To demonstrate the recent advancements made with AHSS, engineers designed the PBC-EV, or POSCO Body Concept-Electric Vehicle, using POSCO GIGA STEEL. The PBC-EV car body was able to achieve a 26.4% reduction in total weight when compared to cars of the same size without any sacrifices in safety or structural integrity.
The Eco-friendly Life Cycle of AHSS
When measuring greenhouse emissions of cars, one must also look beyond the immediate impact of gasoline consumption and view the material more holistically through a life cycle assessment. The emissions costs related to the extraction and production of automobile materials can be high. However, technological advancements in steel production have been able to reduce CO2 emissions – helping to make it one of the most eco-friendly materials for car makers.
Based on its life cycle assessment, measuring carbon dioxide emissions from production to recycling, POSCO GIGA STEEL performs remarkably well as an eco-friendly material. Steel emits 2.0 to 2.5 kg of carbon emissions when producing 1 kg of material while aluminum emits 11 to 12.6 kg when producing the same amount. Even after production, cumulative greenhouse gas emissions of vehicles made with steel is 10% lower when looking at the full life cycle.
Lastly, steel remains the most recycled materials on the planet, and automobiles maintain a recycling rate of nearly 100 percent. Almost all steel products contain recycled steel as steel scrap is a necessary ingredient when producing new steel.
Advancements in AHSS have allowed the auto industry to move beyond the barriers that have held it back in the past. As consumers demand more fuel efficient driving options and as governments around the world impose more strict emissions standards, material advancements in steel will become more critical. It is the breakthroughs in steel technology like these that are helping to bring lightweight, fuel-efficient cars to market.
Throughout April and May, The Steel Wire is exploring trends in the auto industry and how POSCO’s innovations in automotive steel is leading the way toward lighter, stronger, and more affordable cars.
- advanced high strength steel
- AHSS
- auto industry
- automakers
- automobile industry
- automobile manufacturers
- automotive industry
- automotive steel
- BMW i3
- car
- car makers
- carbon
- cars
- Chevrolet Volt
- CO2 emissions
- eco-friendly
- electric car
- electric cars
- giga steel
- global
- greenhouse gases
- IIHS
- lightweight
- Lightweight Cars
- material
- MIT
- PBC-EV
- POSCO GIGA STEEL
- production
- recycling
- safety
- steel production
- steel products
- Tesla Model S
- Toyota Prius
- transportation
- vehicle