World Auto Steel (WAS) kicked off its #Steelyourworld campaign to highlight the benefits of advanced high-strength steel (AHSS) as an automotive material. The first of the 4-part campaign is called #steelyourweight, and covers one of the best features of AHSS – its light weight.
Contrary to popular belief, mass reduction does not automatically equal fuel savings, especially when it comes to urban driving. There are other factors that determine the fuel efficiency of a vehicle such as driving cycle, vehicle size and its powertrain. Until recently, there was a lack of variety in engine types and powertrains, so even though automakers reduced the weight of car frames, they could not apply a complementary engine or powertrain to the lighter parts.
So, have automakers been lightweighting for nothing?
Of course not, in the past decade alone, engines and powertrains have also become extremely efficient through advancements in start-stop-systems and downsizing, and newer options including hybrids, electric batteries and range extenders that now allow automakers to capitalize on their lightweight materials.
Although there are several lightweight materials, below are 5 reasons why AHSS continues to be the lightweight material of choice for automakers:
1. Decision Makers Care About the Environment
Well, not everyone, but many countries around the world have started the process to phase out gasoline and diesel-fueled cars, including India and China, the two largest automotive markets in the world. Governments are taking serious action against climate change and it will reflect in their policies. Automakers are choosing to lightweight their vehicles for lower emission rates with AHSS, because not only is AHSS lightweight, there are no trade-offs with other vital features such as safety and cost-effectiveness.
2. Everyone’s Going Electric
Globally, automakers are investing in electric vehicles (EVs) in line with national and international environmental policies. However, EVs still have a ways to go before they become the norm. EVs will face the same safety requirements as regular cars, but with the added responsibility of protecting the battery and its flammable components during a crash.
In 2016 there were several car accidents involving the Tesla Model S, where leaked battery fluids caused fires. Automakers need to find a solution to make EVs as safe, and eventually, safer than traditional cars. As an innovative automotive material, AHSS was built for safety.
3. Safety is Always First
Safety is and should always be the number one priority for automakers, material providers and policymakers alike. Even with all the hype about autonomous driving and sensors, there is very little chance that policymakers will reverse the stringent safety regulations in place today. People want to feel safe, no matter what type of car they are getting into.
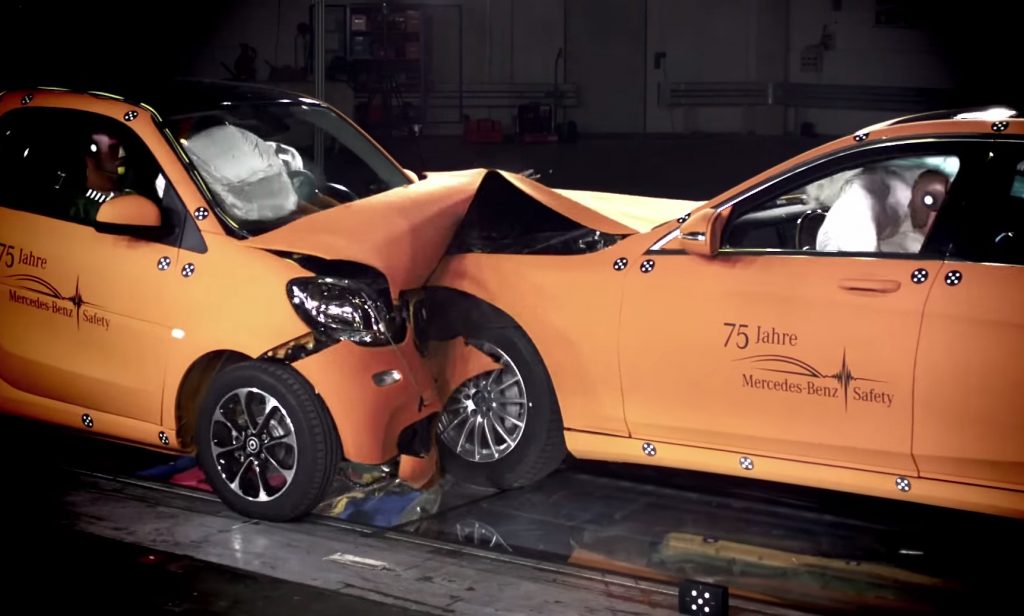
2016 Smart Fortwo and the Mercedes S Class take part in a crash test (Source: Green Car Reports)
One possible material solution is Complex Phase (CP) steel, a type of POSCO GIGA STEEL for the vehicle’s side panels, bumper rails and door impact bars- the parts that determine the safety ratings of the vehicle. It has superior strength and shock-absorbing qualities, without the added weight of traditional high-strength materials, and that’s why carmakers such as GM Korea, Ssangyong Motors and Renault Samsung Motors all use POSCO GIGA STEEL.
4. Cost is Always Second
This goes for automakers as well as drivers on the consuming end. Drivers want lower costs without compromising safety and performance ratings, and desire fuel efficiency- a major reason why automakers are lightweighting.
Some automakers choose alternative materials such as aluminum and carbon fiber to meet lightweight requirements to find that not only are the materials more costly over steel, factories need an equipment overhaul to work with them. Moreover, there are additional costs related to training employees to work with new materials, whereas all auto manufacturers are familiar with welding and forming steel.
Take a look at this infographic and see how AHSS stacks up against other lightweight materials in terms of cost and performance.
5. It’s Not Over Till It’s Over
No two lightweight materials are the same when observed under the life-cycle approach, a comprehensive life cycle assessment of a material’s automotive carbon emissions from production to disposal. Often times, the process of manufacturing lightweight materials and improved powertrains result in more carbon emissions than they are saving.
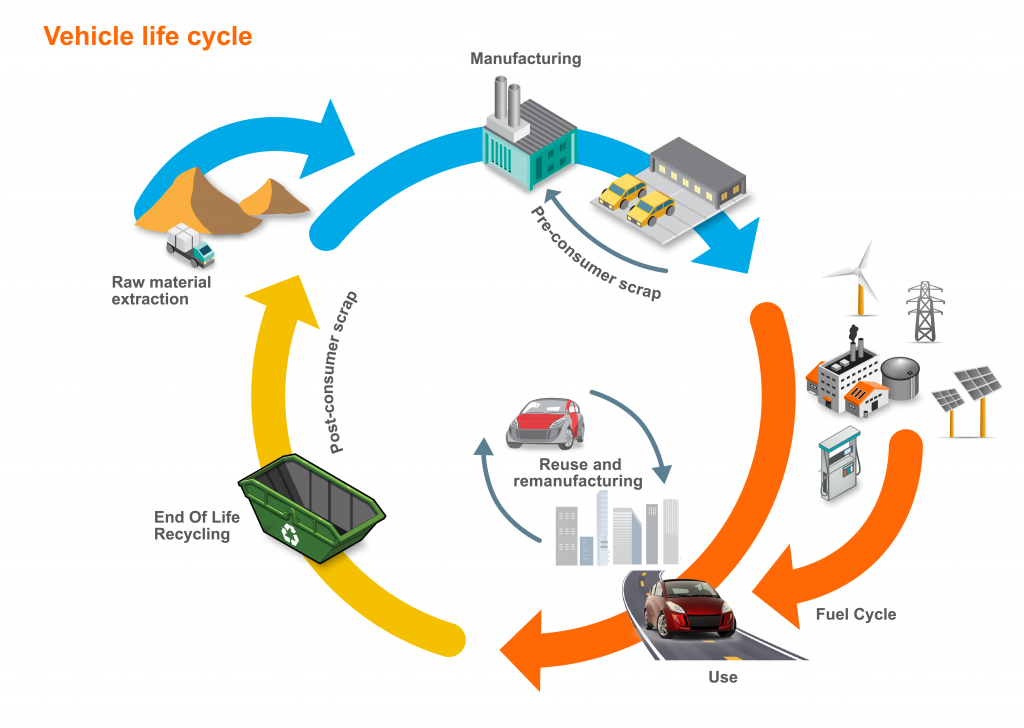
The life cycle assessment can be used to determine the carbon output of a vehicle. (Source: World Auto Steel)
At the end of the day, steel has the lowest production-related emissions and can be recycled at the end of its lifecycle. Steel remains the most recycled material because it can be reapplied in different forms almost infinitely.
Automakers are increasingly incorporating lightweight materials to their new models. Although competition for the greatest market share of lightweight materials is fierce, AHSS is by far the leading material when it comes to lightweight solutions. According to McKinsey & Company’s Lightweight, Heavy Impact report, the percentage of high-strength materials used for cars will increase to 38 percent by 2030, compared to 15 percent in 2010. Steel continues to evolve according to the changing demands of the auto market, and for now, there is no other multi-solution material that can compete.
Cover photo courtesy of Hyundai.
Don’t miss any of the exciting stories from The Steel Wire – subscribe via email today.
- advanced high strength steel
- AHSS
- auto
- auto market
- auto producer
- automaker
- automakers
- automobile
- automotive
- automotive steel
- car manufacturer
- carbon emissions
- carmaker
- cars
- complex phase steel
- CP steel
- GM Korea
- Going Electric
- high-strength steel
- LCA
- life cycle approach
- life cycle assessment
- light steel
- lightweight
- lightweight car
- lightweight material
- material
- posco ahss
- posco automotive steel
- posco car
- POSCO GIGA STEEL
- Renault Samsung Motors
- safety
- Ssangyong Motors
- steelyourweight
- steelyourworld
- vehicle
- vehicle life cycle
- was
- World Steel Association
- WSA