Ssangyong Motors debuted their G4 Rexton SUV on March 30th of this year, at the 2017 Seoul Motor Show. The new SUV received five stars for collision safety from the Korean New Car Assessment Program (KNCAP) and is generating plenty of attention.
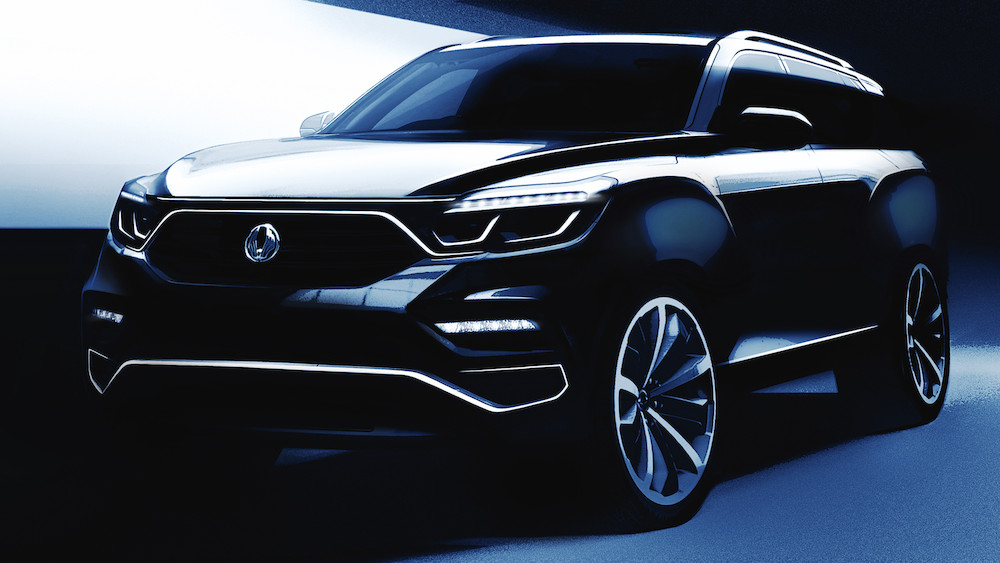
Ssangyong Motors G4 Rexton (Source: Ssangyong Motors)
A notable feature of the G4 is its quad frame body on chassis made of POSCO GIGA STEEL. These days, most SUVs opt for a monocoque frame because it requires less materials, and thus is lighter. However, Ssangyong chose to stick with their signature frame body to enhance safety and driving performance. In order to achieve high strength without adding extra weight, they applied POSCO GIGA STEEL to 81.7 percent of their frame.
The Steel Wire spoke to Ssangyong Motors Senior Researcher Shim JaeHong for an inside look at the 42-month development process worth 380 billion won and their cooperation with POSCO.
Q. How did you first decide to apply POSCO GIGA STEEL to the G4 Rexton?
When I first heard about the product, I was very impressed and knew that it would fit well with Ssangyong Motors’ philosophy of safety first. The only concern I had was moldability, a common problem with previous materials. I didn’t know if POSCO GIGA STEEL could be molded into the right parts for our frame.
Thankfully, POSCO had a very collaborative approach and we conducted joint research from the beginning to come up with the right solutions. POSCO also helped with shape and structure analysis for the final product and even suggested the best materials for each part. In the end, POSCO took care of our material burdens and saved us time and money along the way.
Q. Most vehicles these days have a monocoque chassis. Why did Ssangyong choose to stick with the body-on-frame chassis for its new G4 Rexton?
We went with the body-on-frame chassis because safety has always been the top priority for Ssangyong Motors. Plus, we believe that in order to have a genuine SUV, you need to have a body-on-frame chassis. Our consumers also acknowledge this, so we didn’t want to compromise on that.
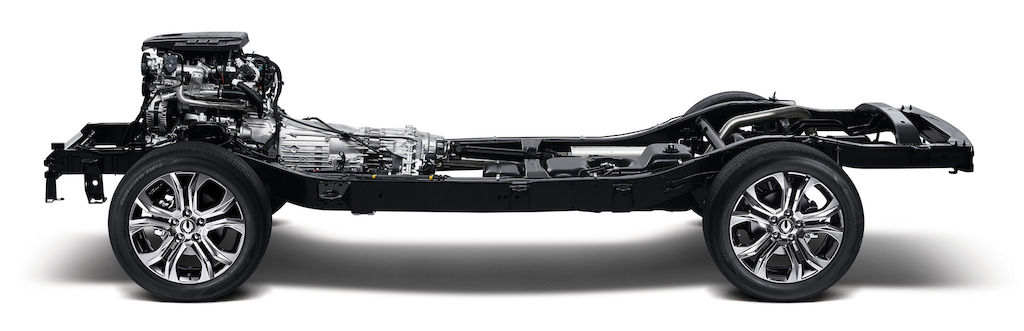
The base of the G4 Rexton quad frame (Source: Ssangyong Motors)
Q. Ssangyong emphasized the quad frame during the G4 Rexton’s release. What is different about the quad frame versus previous frames?
The biggest difference was that POSCO GIGA STEEL was applied to 81.7 percent of the entire frame. As a result, even though we added material to the cross section of each component, we were able to minimize the increase in weight. Especially for crash energy absorption, we applied a quad structure to the frame which lead to a 5-star rating for collision safety from the KNCAP. The G4 also has the best NVH (noise, vibration, harshness) rating of all previous models.
Q. How were you able to apply a quad structure to your frame without adding on weight?
POSCO GIGA STEEL was the material solution for our quad frame. Thanks to the quad frame, we were able to further reduce the weight of other parts. In particular, the application of high-strength steels allowed us to greatly reduce the thickness of parts without compromising safety in any way. The quad frame actually turned out to be lighter than or equal in weight of the monocoque chassis of other companies.
Q. What was the greatest technical challenge for you during the development process?
As mentioned before, moldability is always a challenge to get materials into the right shapes for different parts of our frame. It is possible to increase formability by using hot press forming or roll forming methods. The problem is, it takes a lot of time and money and the increased cost of production means a higher price on the final product for consumers.
This is why POSCO’s early involvement was crucial. Together, we were able to simplify the shapes of the applied parts as much as possible, optimize its thickness and came up with a way to apply conventional pressing methods to shape the parts. Again, this was crucial for us in saving time and costs.
Q. As a customer of GIGA STEEL, what can you say about the potential for growth and development for the product?
In the future, cars will face more and more demanding regulations regarding the environment, safety and performance. The use of advanced high-strength steel plates is inevitable in order to meet those new laws and regulations. That being said, I think GIGA STEEL will be used for more auto parts than now.
Q. Are there any additional projects you would like to pursue with POSCO?
So far, we have been able to find innovative solutions to technical challenges in our partnership. Going forward, I would like to collaborate on technology to cold form complex steel parts. The cost-effective and time-saving technology will benefit both POSCO and Ssangyong Motors mutually.
If our companies maintain a collaborative relationship that surpasses traditional supply-demand roles, I believe we will continue to develop innovative materials and improve cost-efficiency. I think it will be a chance for both companies to make huge advancements.
Ssangyong Motors is one of many automotive partners POSCO works closely with, including GM Korea and Renault Samsung Motors. POSCO GIGA STEEL is a breakthrough solution that allows automakers to meet stringent regulations, save costs and enhance performance. Matched with POSCO’s Marketing Solution 2.0, POSCO will continue to play a vital role as a partner to automakers and the successful sales of their vehicles.
Cover image source: Ssangyong Motors
Don’t miss any of the exciting stories from The Steel Wire – subscribe via email today.