Park Jong-jae, a motorsport columnist, explores how POSCO GIGA STEEL provides the ideal solution to meet the needs of today’s auto industry and its increasingly strict demands. This article is part two of our POSCO GIGA STEEL series. Read Part one on how POSCO GIGA STEEL goes beyond the limits of traditional lightweight materials.
Auto Industry’s Challenge to Meet Consumer Demands
Mileage, design, and emissions. Which do you consider the most when purchasing a car? It is difficult to say that one is more important than the others, and fortunately, POSCO GIGA STEEL offers unique benefits for each one to meet the needs of today’s auto industry as it faces increasingly strict demands on safety and fuel efficiency.
More than ever, the industry is requiring that a vehicle goes longer distances with less fuel, which means the car must be lighter. Also, technological advances have enabled cars with more power, requiring them to be safer. Consumers also want a car that represents their personality, demanding vehicles with more sophisticated and elegant designs.
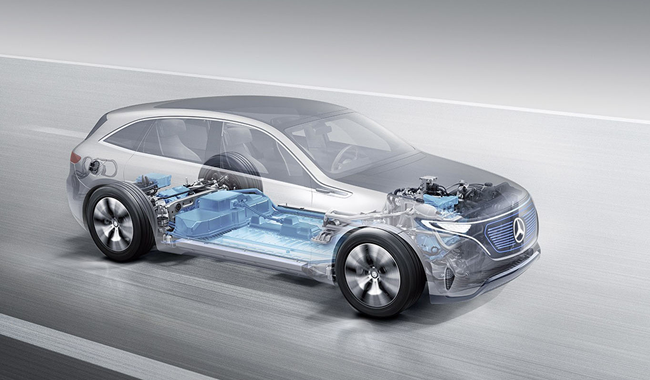
Cars now need to drive smoothly, burn less fuel, and ensure safety, all while boasting an elegant design (Image courtesy of Mercedes-Benz AG).
While there are other conditions that need to be considered, it is paramount that cars meet the following three conditions in order to satisfy consumers: fuel efficiency, safety, and design. But these demands are becoming increasingly difficult to meet, and the only solution is to discover a technology that enables all of the above. For safety considerations, in the event of a collision, parts of the car also need to absorb the kinetic energy and protect the passengers inside.
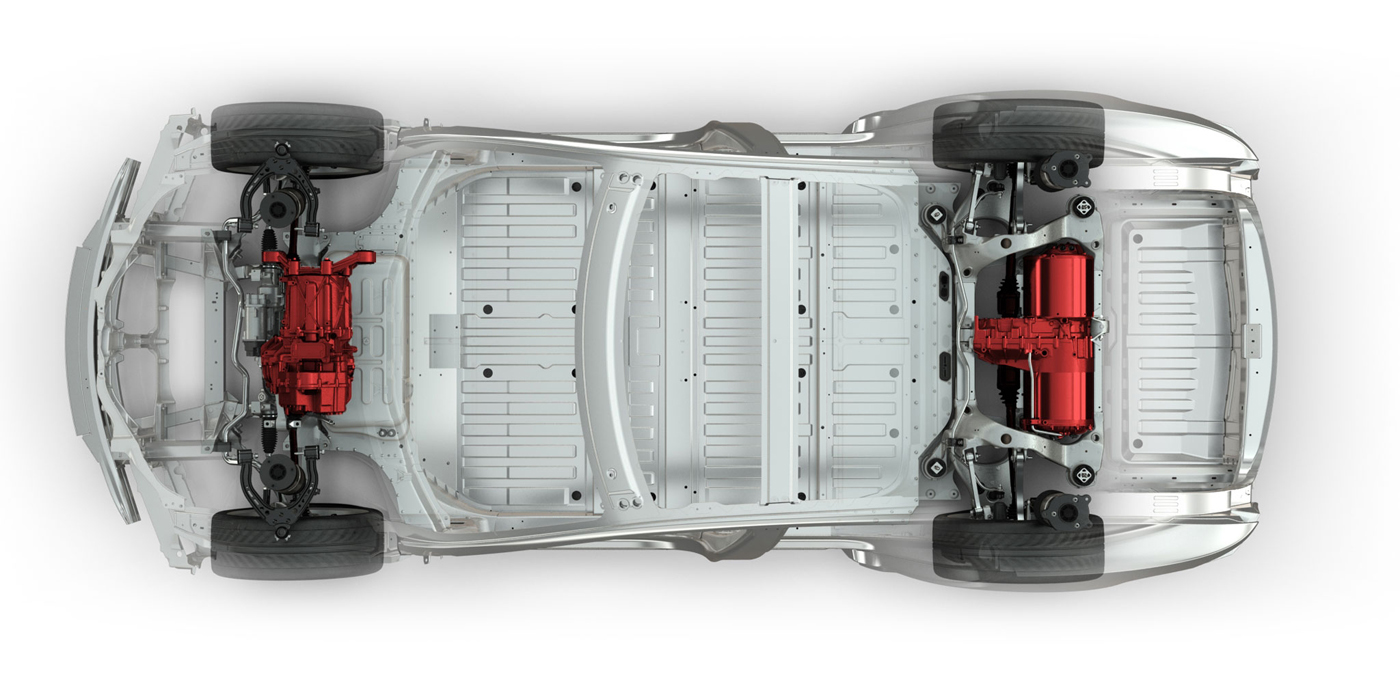
In addition to having a battery and electric motor, the electric car is different from standard cars because the battery is a part of the frame itself.
6 Types of POSCO GIGA STEEL Tailored for Different Auto Parts
POSCO GIGA STEEL is an advanced high-strength steel (AHSS) that can meet these various demands. Let’s take a look at the different types of POSCO GIGA STEEL products and how each one is being used in different parts of the car.
Complex Phase (CP) Steel
Complex Phase (CP) steel is often used to make reinforced auto parts that require high crashworthiness ratings, such as sill side panels, bumper rails, and door impact bars. It plays an extremely important role in the car frame as it is highly resistant to dents or bumps. In the past, the side panels of race cars were purposely made to be thicker in order to prevent dents and protect the driver inside and this naturally led to the vehicle becoming considerably heavier. However, CP steel minimizes these disadvantages. In the event of an impact, cars made with CP steel retain its original shape considerably better than other car frames due to its high strength and also has an exceptional ability to absorb all of the energy while still exhibiting an impressive thinness. It is often incorporated into the sill side panels and door impact bars to allow for a more spacious design.
Dual Phase (DP) Steel
Dual Phase (DP) steel can be easily welded and deformed and boasts a high level of total elongation (the rate at which the material is stretched without snapping). DP steel is commonly used in seat rails or other lower body reinforcements that run underneath the passenger seat. The tensile strength is at least 980MPa, but because it also exhibits impressive ductility, it can easily be used for random spare parts.
Transformation Induced Plasticity (TRIP) Steel
Transformation Induced Plasticity (TRIP) steel first made its way into the auto industry about six years ago. As the auto industry is beginning to value lightweight cars more and more, TRIP steel has received more attention. It is mainly used in the inner parts of the car body. This part of the car needs to absorb shock and impact and also be flexible enough to be fitted around the complex inner structure of the car. With TRIP steel’s outstanding combination of strength and ductility, it is one of the most commonly used high-strength automotive steels in the auto industry today.
Martensite Steel (MART)
Because Martensite steel is naturally high in strength, thinner sheets produced from roll forming (a metal forming process in which steel is continuously shaped or formed until it reaches a desired cross-section) still retain the same level of performance as conventional parts. Thinner parts also have the added benefit of reducing the weight.
Hot Press Forming (HPF) Steel
Hot Press Forming (HPF) steel is a different class of steel made with a unique steel production process. Typically, as steel becomes higher in strength, it is more difficult to mold into the desired shape through conventional processes. However, through the HPF process, the steel is heated to 950℃ before press forming. At high deformation temperatures, steel sheets are very soft so that difficult shapes can be obtained easily. During forming, the heated steel sheet cools down rapidly in the die block, so that the resulting pressed parts have a very high strength level. Due to its combination of high strength and formability, HPF steel is often used in the B-pillar of a car which requires intricately shaped parts as well as the A-pillar roof side rails which are prone to damage.
Post Heat Treatment (PHT) Steel
The chassis that supports the car frame needs to be extremely durable and resistant to impacts or shocks on the road as its main function is to improve the ride quality of the vehicle.
In order to increase the durability and torsional resistance, the material needs to be quenched and tempered. Before going through the heat treatment portion of the process (quenching), the material can be easily molded into spare parts due to its reduced strength. After being molded, it is heated up to 950°C and then rapidly cooled by water. This is why PHT is called “post-heat treatment steel”. Due to its ultra-high strength, it also has lightweighting benefits and is typically used in a vehicle’s chassis, stabilizer bars in a suspension system, and torsion beams.
These six types of POSCO GIGA STEEL each have their unique advantages in terms of processability & strength, production cost, and ease of application. Compared to conventional materials, thinner pieces can be used while still retaining the same level of performance and strength. Due to these incredible characteristics, POSCO GIGA STEEL is able to meet the increasingly stringent requirements of the auto industry for safety and efficiency.
Researchers in the auto industry are constantly looking for a stronger, more formable material. As the auto industry undergoes another paradigm shift, POSCO GIGA STEEL will continue to offer unique solutions that can satisfy both automakers and consumers.
Park Jong-jae is a motorsport columnist and the former editor-in-chief at F1 Racing Korea. |
Don’t miss any of the exciting stories from The Steel Wire – subscribe via email today.
- advanced high strength steel
- AHSS
- auto industry
- auto manufacturers
- auto parts
- automobile industry
- automobile manufacturers
- automotive industry
- automotive steel
- car
- car makers
- cars
- Complex Phase
- CP steel
- design
- DP Steel
- Dual Phase
- energy
- formability
- giga steel
- Hot Press Forming
- HPF
- HPF Steel
- lightweight
- MART
- Martensite Steel
- material
- PHT
- PHT Steel
- POSCO GIGA STEEL
- Post Heat Treatment
- safety
- steel production
- steel sheets
- strength
- Transformation Induced Plasticity
- TRIP steel
- vehicle