Over the last 60 years, consumers, automakers, and regulatory agencies have been looking for ways to build cars that are safer for their passengers. The steel industry has responded by offering material solutions that are stronger and able to absorb more powerful impacts. POSCO GIGA STEEL is one of those solutions. It offers automobile manufacturers a unique solution that is both extremely strong and easily formable – helping car makers build cars that are stronger and safer.
Increasing Safety Requirements Demand Stronger Steel
With an increasing awareness about car safety – governments and regulatory agencies have been passing stricter safety regulations for autos. At the same time, consumers began demanding better protections, and car makers began building safer vehicles. While there are many factors to consider in building a safer car – airbags, seatbelts, glass type – the crashworthiness, or structural integrity, of the car’s body frame is one of the most critical.
In 1975 the average vehicle was manufactured with 55.9% mild steel and just 3.6% medium and high strength steels. By 2007, the percentage of medium and high strength steels used in an average car had increased by more than 230%. In the seventies, steel companies simply did not have the technology to make the steel that they can produce today because while it was strong, it was brittle and difficult to work with. Today, innovations in steel technology have given car makers the ability to use a variety of advanced high-strength steels (AHSS) that exceed 1,000MPa – meaning it can withstand more than 100 kilograms-force per square millimeter – because they are both strong and formable.
To demonstrate how far we come in terms of building stronger, safer vehicles, watch this crash test performed by the IIHS for their 50th anniversary with a 1959 Chevrolet Bel Air and a 2009 Chevrolet Malibu.
POSCO GIGA STEEL, the Industry’s New Standard for Strength and Formability
With a tensile strength of more than 1,000MPa, POSCO GIGA STEEL falls in the strongest categories of steel available to auto manufacturers today. In addition to providing the strength needed to meet safety regulations, POSCO GIGA STEEL is also ideal because of its formability and processability.
While recent years have seen ultra strength steels come on to the market with tensile ratings above 1,000MPa, these have often been rigid and brittle, making them difficult to process and mold into workable parts. POSCO GIGA STEEL bridges that gap by offering an automotive steel solution with high ductility and high tensile strength. This unique technology makes POSCO GIGA STEEL a unique fit for automakers seeking materials that can be processed into complex parts while also offering the highest levels of strength and safety for consumers.
Because of the combination of both strength and formability, SsangYong Motor unveiled their new G4 Rexton SUV with a body frame that contains 63% POSCO GIGA STEEL – the highest ratio ever achieved in a body frame design. Manufacturers like SsangYong Motor can use such high ratios of AHSS because of the technological advancements that have improved its formability in line with its improvements in strength.
Testing the Strength of POSCO GIGA STEEL and Aluminum
As lightweighting has become a priority for car makers seeking to build more fuel efficient cars, many have been looking toward alternative materials to step in as a substitute for steel. However, while offering certain benefits in weight, these alternative materials offer tradeoffs in strength and formability. On the other hand, POSCO GIGA STEEL offers an ideal solution in terms of strength, weight, and formability for auto manufacturers that must adhere to safety and environmental regulations along with consumer demand.
To compare the strength and impact energy absorption of POSCO GIGA STEEL (CR1180TRIP) and aluminum (Al5083), researchers at the KAIST National Center for Standard Reference Data performed an experiment in which a projectile was fired at three equidistantly spaced pieces of POSCO GIGA STEEL and aluminum.
Traveling at 185 meters per second, researcher Park Myung-joon noted that “the projectile ripped through all three pieces of aluminum while not even breaking one sheet of the POSCO GIGA STEEL.” Saying, “This experiment helped demonstrate how POSCO GIGA STEEL is more than three times stronger than aluminum making it ideal for automotive applications.”
Watch the video below to see how the experiment was designed, set up, and carried out.
POSCO GIGA STEEL is seeing increasing demand with car makers as they realize the dual benefits of strength and formability. At the Seoul Motor Show last month, Renault Samsung Motors and Chevrolet both unveiled new vehicles that were made using POSCO GIGA STEEL instead of aluminum – boosting the car body’s strength and safety for passengers.
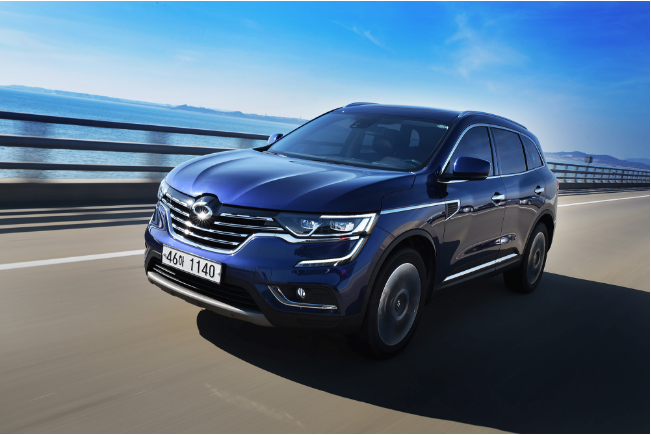
Due to POSCO GIGA STEEL’s increased strength and high formability, the new Renault Samsung QM6 was able to maintain excellent safety standards with easy integration into its production process.
POSCO GIGA STEEL is unique because it combines both strength and formability. With strength more than three times stronger than aluminum and with formability properties that allow it to be made into complex auto parts – POSCO GIGA STEEL is the most ideal solution for car makers today.
Throughout April & May, The Steel Wire will explore the uses and benefits of POSCO GIGA STEEL and what POSCO is doing to lead the industry with new automotive steel solutions.
Don’t miss any of the exciting stories from The Steel Wire – subscribe via email today.
- advanced high strength steel
- AHSS
- aluminum
- auto manufacturers
- automobile industry
- automotive industry
- automotive steel
- building
- car makers
- car safety standards
- cars
- crash safety
- crash test safety
- crashworthiness
- design
- efficient cars
- energy
- formability
- G4 Rexton
- IIHS
- injuries
- material
- NHTSA
- POSCO GIGA STEEL
- solution
- ssangyong
- Ssangyong Motor
- steel industry
- technology
- vehicle