On February 20, POSCO held a ceremony to celebrate the expansion of its non-oriented silicon steel facility, which will provide environmentally-friendly electric vehicle drive motors. Clients, suppliers, and more than 100 officials from affiliates such as POSCO E&C and POSCO ICT joined POSCO CEO Ohjoon Kwon to celebrate the completion of its production capacity expansion project at Pohang Steel Works.
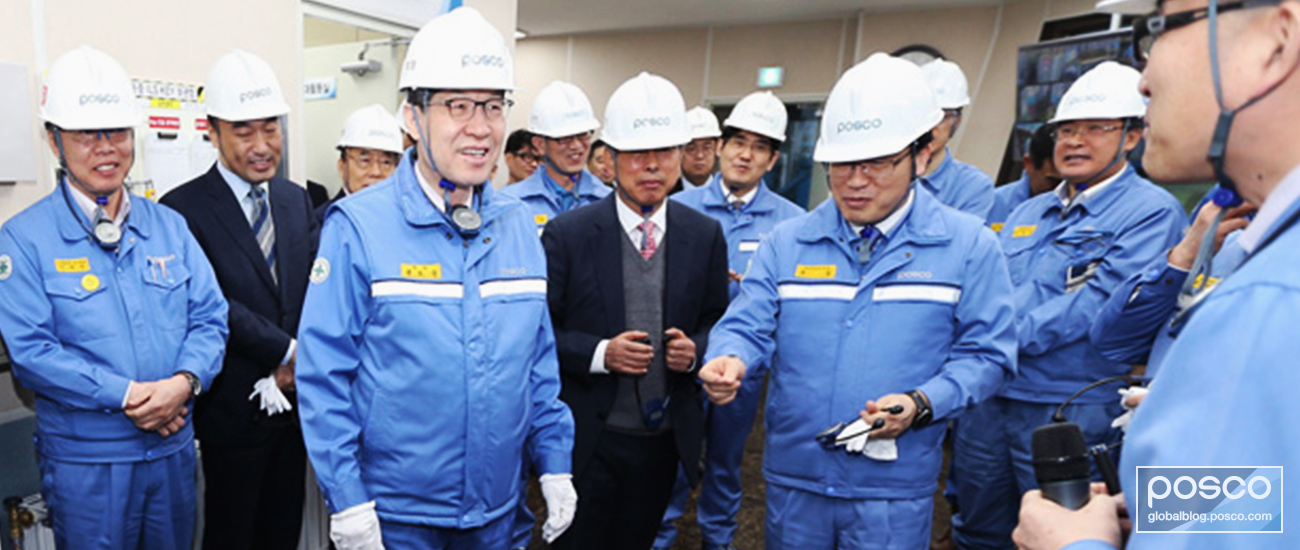
From left to right: Seong Yu, VP of POSCO; Young-hoon Lee, CEO of POSCO Chemtech; Dae-woo Lee, employee representative of the labor-management committee; POSCO CEO Ohjoon Kwon; Won-ho Choi, Chairman of Taehwa; In-hwa Jang, VP of Taehwa; and Tong-il An, General Manager of Pohang Steel Works.
With the completion of the project, POSCO’s top-grade non-oriented silicon steel (Hyper NO) production has increased from 80,000 to 160,000 tons, which is enough to supply parts for approximately 2.6 million electric vehicle drive motors.
Electric steel plates are made by adding 1-4% silicon to iron. They possess excellent electromagnetic properties and consist of high-grade steel material. Depending on the crystallographic direction of the metal, they are categorized as either grain-oriented silicon steel or non-oriented silicon steel. Grain-oriented steel is used as a material for the core of stators like transformers, whereas non-oriented silicon steel is used as a material for rotors like motors and generators as it contains nearly identical electromagnetic properties in all directions.
This capacity expansion project successfully met its goal of producing more top-grade non-oriented silicon steel, which is a core ingredient in high-efficiency premium consumer electronics and electric vehicles. It is an environmentally-friendly material that saves energy and reduces CO2 emissions.
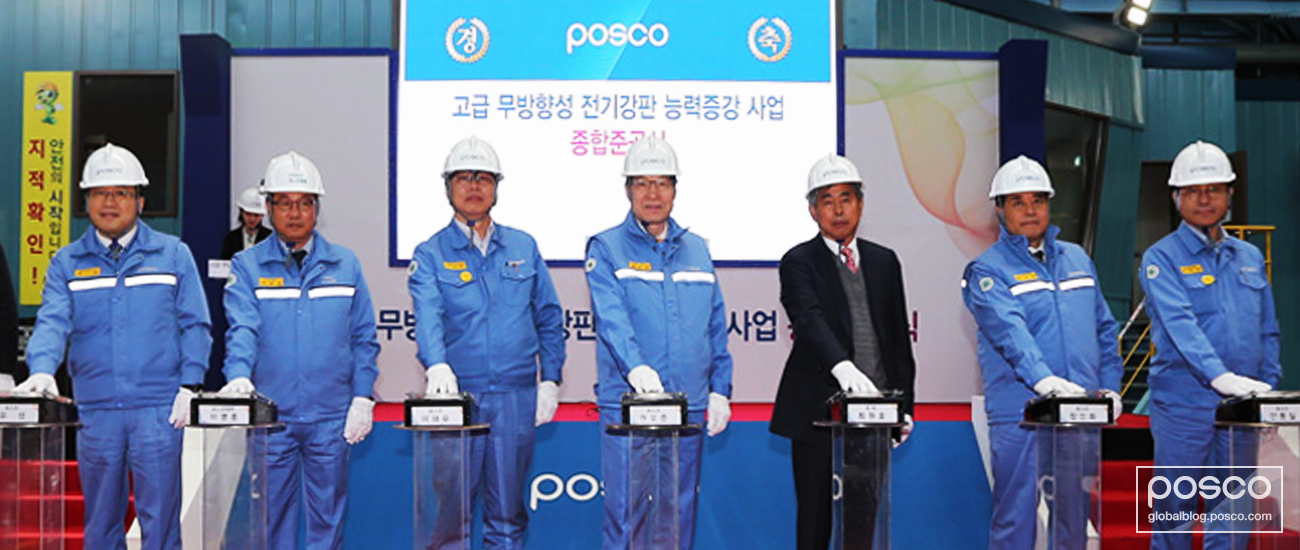
POSCO CEO Ohjoon Kwon encourages employees to continue striving towards becoming a leader supplier of high-quality, non-oriented silicon steel.
As demand for environmentally friendly vehicles and high-efficiency consumer products continue to increase, the demand for top-grade electric steel plates (the materials for core parts) is also expected to rise from last year’s 800,000 tons to more than 1 million tons in 2020. POSCO aims to increase its market share by developing customized products for individual electric vehicle manufacturers and providing specialized services. As the quality of consumer electronics improves at home and abroad, POSCO is hoping to see a spike in profit through increased sales of its top-grade non-oriented steel and premium-grade materials for high-efficiency motors.
This project required an investment of KRW 124.1 billion and helped boost the local economy as a total of 200,000 construction workers were employed during the construction period. POSCO was also able to reduce the total cost of the project by shortening the construction period, recycling equipment, and optimizing the design.
POSCO CEO Ohjoon Kwon said, “With the completion of this project, POSCO is now able to proactively meet the increasing demands for environmentally-friendly cars and high-efficiency premium consumer electronics. We will continue to do our best to give our customers top-quality electric steel plates and lead the premium market with technologically-advanced, high-quality products. ”
With the successful completion of the high-grade material capacity expansion project, the installation of additional equipment, and a stable production system, POSCO is now better equipped to meet domestic and overseas demands for non-oriented silicon steel.
This project is just one of many that POSCO has carried out in order to secure its position as a leading supplier to meet the needs of the ever-expanding high-efficiency premium consumer electronics and electric vehicle market. Other projects have included making improvements to the APL (Annealing & Pickling Line), ACL (Annealing & Coating Line), and the ZRM (Sendzimir Reverse Mill), which is capable of producing 0.15mm steel sheets. This particular project resulted in the production of 0.15mm electric steel plates, which contributes to minimizing power loss in customers’ end products.
Don’t miss any of the exciting stories from The Steel Wire – subscribe via email today.