Now more than ever, advanced technology in smart factories is playing a central role in making the steel industry more efficient and sustainable. The introduction of artificial intelligence, Internet of Things (IoT) and Big Data is looking to change the way manufacturers traditionally produce and manage steel.
Here’s a look at how steel is produced in a steel mill or factory, and what the “smartization” of steel factories will look like.
So, how is steel made?
Iron Making
To make steel, manufacturers first need molten iron. Molten iron comes from two raw materials; iron ore and coal. Iron ore is converted into sinter ore in a sintering plant and coal is converted into raw coke using a coke oven. The processed materials are poured into a blast furnace where hot air reaching 1200℃ is blown in from the bottom through tuyeres, causing a chemical reaction. This process oxidizes the coke and reduces the sintered ore, creating molten iron.
Steelmaking
In the steelmaking stage, the molten iron is transported to the steel making plant via a torpedo car, where the liquid is poured into a converter. Then, oxygen is blown into the converter to burn off all the impurities. All that is left is pure molten steel.
Continuous Casting
This is where steel finally becomes solidified into different shapes such as slab, bloom and billet. Liquid steel is poured into molds and cooled as it passes through a continuous casting machine until it solidifies into the desired shape.
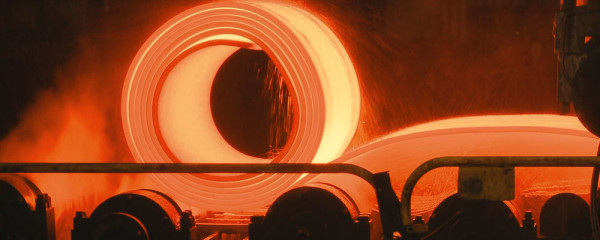
Hot steel passes through rolling machines to be rolled into specific sizes and thicknesses. (Source: Global Sourcing Blog)
Rolling Process
During the rolling process, steel is heated once more to achieve various sizes and thicknesses. Steel slabs are heated to over 1100℃, then pass through rolling machines. This results in hot-rolled coils that can be shaped for different uses such as thick plates. They can also be processed into long, wire-shaped rods for billets. Often, the hot-rolled coils are rolled at room temperature for cold-rolled coils. Cold-rolled coils can be fabricated to produce galvanized and electrical steel products.
“Smartizating” these processes will involve converging IoT, Big Data, and AI to connect the different facilities, IT systems and workers in order to collect and analyze data for optimization.
POSCO is “smartizing” the steel-production process
POSCO is a steel company looking to lead the industry in adopting smart factories. CEO Kwon Ohjoon made “smartization” one of the 4 key priorities for POSCO starting back in 2014, and Kwon will continue to increase those investments.
SEE ALSO: How Smart Factories are Changing the Manufacturing Industry
In 2016, POSCO established its Smart Solution Council in order to research AI, big data and IoT applications. In the same year, POSCO ICT’s smart factory platform, PosFrame, was completed and installed in POSCO’s Gwangyang Steel Mill. PosFrame allows engineers to collect and monitor big data. So far, the company has saved over USD 14 million by incorporating the new technology in its production practices.
Here are some other features of POSCO’s Smart Factory.
POSCO’s Smart Blast Furnace
The Pohang Blast Furnace No.3 became a smart furnace in 2017, following a 102-day repair period. The furnace is now equipped with automated sensors that monitor and control its internal conditions using AI technology. Smart sensors monitor the blast furnace for factors like raw material quality and ventilator status, preventing breakdowns and ensuring a much longer lifecycle.
SEE ALSO: Will Artificial Intelligence Lead to Breakthroughs in the Steel Industry?
Worker Safety
Smart sensors can be used for more than just process monitoring. The company is working toward a full implementation of smart sensors for safety purposes, using IoT to create a better working environment.
Steel manufacturing involves high temperatures and high pressure levels, which is dangerous for workers who come in close contact with the equipment. With smart sensors monitoring all of the factory information, workers will instead be monitoring operation from a safe distance.
Wearable sensors, in conjunction with factory smart sensors, will be able to detect if and when workers are approaching potentially dangerous areas, and will alert them. These sensors will also detect and alert with regards to any impending accidents, or life-threatening situations like gas leaks, explosions, or fires.
Also, dust, sulfur, and nitrogen compounds will be removed via a high-plasma method, creating an eco-friendly steel plant and a healthier environment for workers.
POSCO will continue to add more smart features to its steel mills to increase efficiency, safety and sustainability. In efforts to learn and implement new technologies, POSCO CEO Kwon Ohjoon visited GE’s smart factories to learn about their technology earlier this year. POSCO also held the 2017 Smart POSCO Forum to share its insights with clients and affiliates, all as part of its expanding smartization efforts.
- 2017 Smart POSCO Forum
- advanced technology
- artificial intelligence
- Big Data
- continuous casting
- factories
- how is steel made
- how is steel produced
- how make steel
- how produce steel
- how steel is made
- how to make steel
- how to produce steel
- internet of things
- iot
- iron making
- Kwon Ohjoon
- manufacturing
- manufacturing industry
- molten iron
- plant
- pohang blast furnace no.3
- POSCO CEO
- POSCO CEO Kwon Ohjoon
- POSCO ICT
- posco smart
- posco smart factory
- posfame
- produce steel
- rolling process
- Smart Blast Furnace
- Smart Factory
- smart factory platform
- smart sensors
- Smart Solution Council
- smart steel factory
- smartization
- steel factory
- steel industry
- steelmaking
- sustainability
- worker safety