With the Trump administration recently easing restrictions on LNG exports and actively leveraging tariffs in trade negotiations, the entire LNG value chain—production, storage, transportation, and utilization—is gaining attention. Back in 2008, POSCO anticipated a steady increase in LNG demand as a response to tightening global environmental regulations. POSCO recognized the need for new materials to secure a competitive edge in the materials market for LNG storage and transportation. For this reason, it turned its focus to manganese alloy steel, and thus began the development of high-manganese steel. We sat down with Senior Researcher Soon-gi Lee, who is at the heart of the development, certification, and commercialization of this next-generation material.
Q. POSCO’s high-value-added steel, developed in-house, is drawing attention. What exactly is POSCO’s high-manganese steel, and what makes its manufacturing process unique?
POSCO’s high-manganese steel is a new type of steel alloyed with a high content of manganese (Mn, 22.5–25.5%). Compared to conventional materials such as stainless steel, 9% nickel steel, and Invar alloy, POSCO’s high-manganese steel offers comparable performance, but significantly better cost competitiveness. Most importantly, it retains excellent mechanical properties even at cryogenic temperatures as low as -196°C, making it ideal for LNG storage tanks and carriers.
When manganese is added to steel, introducing solid manganese directly into the molten metal can cause a drop in temperature. To prevent this, we melt the manganese before adding it, rather than inputting it in solid form. Typically, adding manganese increases wear resistance and strength, but this comes at the cost of ductility (the property of stretching easily without breaking). However, thanks to POSCO’s decades of accumulated know-how in controlled rolling and cooling techniques, we have succeeded in producing a ductile product despite the high manganese content. Production is currently taking place at our heavy plate plant, and both the material composition and manufacturing method have been bundled into a single patented package.
Q. You said POSCO melts the manganese first to avoid lowering the temperature of the molten steel. But if your competitors build similar melting facilities, won’t they be able to catch up?
Though it sounds simple, POSCO’s proprietary technology is embedded throughout the process. Manganese alloys often contain impurities, so refining during the intermediate stages is critical. Predicting the behavior of molten manganese is also one of our hidden core technologies. Our facilities for producing molten manganese and storing it in insulated furnaces will not be easy for our competitors to replicate.
Q. Is POSCO the only company that can produce high-manganese steel?
Some steelmakers produce general-purpose high-manganese steel. However, in applications requiring higher manganese content, such as the cryogenic (24%) and slurry pipe (18%) grades used in the energy industry, POSCO leads in technological capability.
Q. How does POSCO’s high-manganese steel compare with competing materials?
POSCO’s high-manganese steel meets all the requirements for LNG transport and storage, and offers several advantages over existing materials. It exhibits high strength and excellent elongation* properties.
While most steel materials used for LNG transport and storage contain a high amount of expensive nickel, nickel has been completely replaced with manganese in POSCO’s high-manganese steel. The manganese used in high-manganese steel is abundant worldwide and relatively low in cost, making the final product approximately 30% cheaper than conventional alternatives. Its high elongation makes it easy to process, and it is also highly resistant to hydrogen embrittlement. Having recently been approved for ammonia applications, it can now be used for most liquefied gases, including natural gas, ammonia, and CO₂.
*Elongation: The ratio by which a metal can stretch before breaking; it indicates ductility.
Q. What are some current applications of POSCO’s high-manganese steel?
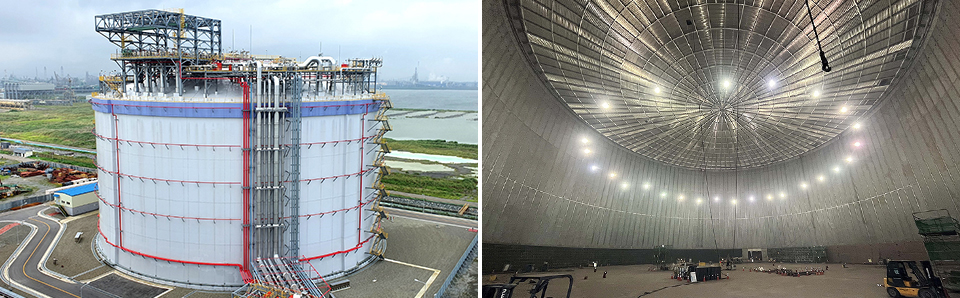
▲POSCO International’s Gwangyang LNG Terminal tank using POSCO high-manganese steel.
Currently, it is being used in Gwangyang LNG Terminal units 5 and 6, Hanwha Ocean’s VLCCs, container ship LNG fuel tanks, and onshore LNG storage tanks. We are working toward expanding its use in LNG carriers and other applications. Beyond LNG, POSCO aims to promote high-manganese steel across various industries as a symbol of Korea’s technological strength.
Q. Could this steel eventually be used in LNG carriers, not just LNG-fueled ships? Doesn’t using thick plates reduce capacity?
POSCO manufactures high-manganese steel as thick plates. Onshore storage tanks are built with thick plates, and LNG carriers can be built using either thin membrane sheets (about 0.7–1.2 mm) or thick plates (6–40 mm). Compared to membrane systems, thick-plate LNG carriers are structurally more robust and better withstand sloshing from LNG motion, providing superior safety under various conditions. Recently, President Trump mentioned Korea’s potential involvement in the Alaska LNG project. To navigate through thick Arctic ice, LNG carriers would need to be icebreaking LNG ships. In such cases, high-manganese steel made in thick plates offers a clear advantage.
There is no reduction in capacity. Shipbuilders simply redesign the hull based on the plate thickness. The standard capacity is 174,000 m³, and designs are adjusted accordingly.
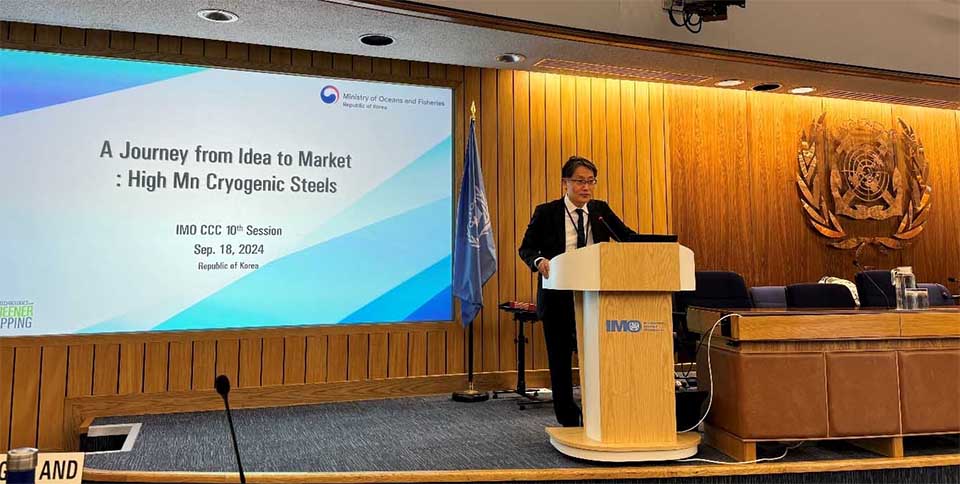
▲The 2024 IMO General Assembly in London invited Korea to present POSCO’s achievements.
Q. We read that POSCO’s high-manganese steel is setting global standards. What does that mean?
Materials for energy applications must adhere to strict international standards. For example, ships sail through international waters, so they aren’t subject to just regional or national regulations—they must comply with global standards. Since POSCO’s high-manganese steel was the first of its kind, no existing standards applied, so we had to create them ourselves. Despite continued resistance from our competitors, we succeeded in registering the material with ASTM, API, ISO, and IMO standards. These international standards are based on POSCO’s technology, meaning that other companies must follow our specifications—effectively making POSCO’s technology the global benchmark.
In particular, the International Maritime Organization (IMO), a UN-affiliated body that sets standards for shipbuilding and operation, formally requested the Korean government to present at the 2023 General Assembly when POSCO’s high-manganese steel received final approval. The IMO viewed the 10-year approval journey led by POSCO and the Korean government as a highly successful and exemplary case, and wanted to share it with member states.
Q. There seems to be a longstanding connection between Chairman In-hwa Chang and high-manganese steel.
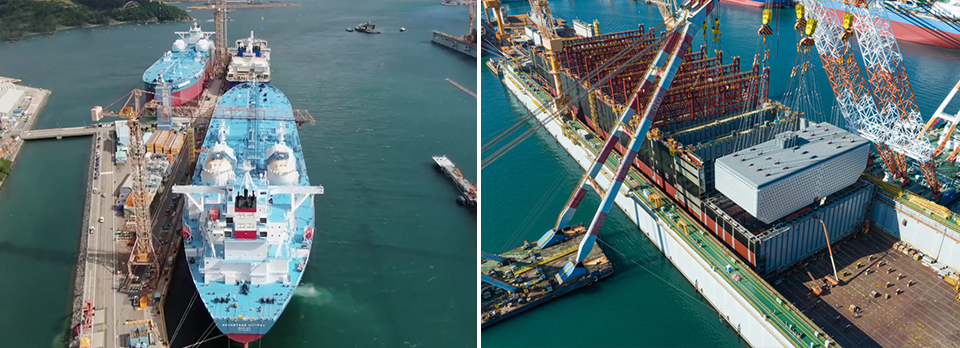
▲(Left) Hanwha Ocean’s crude oil carrier equipped with a high-manganese steel LNG fuel tank in 2022 (Right) Hanwha Ocean’s ultra-large container ship equipped with a high-manganese steel LNG fuel tank in 2024.
Chairman In-hwa Chang has a deep understanding of both shipbuilding and steelmaking, having majored in naval architecture and marine engineering as a student and later worked as a researcher in the steel industry. This unique background has allowed him to make significant contributions to the development and broader adoption of high-manganese steel.
He played a key role in our solid track record* by ensuring the material was actually used in onshore and marine storage tanks, which laid the foundation for future sales growth. Back in 2017, when POSCO was planning to construct the No. 5 LNG terminal in Gwangyang, the initial plan was to use conventional materials. However, as executive vice president at the time, Chairman Chang personally made the decision to use POSCO’s high-manganese steel instead.
His strategy was to create a proven reference case using POSCO’s own material, thereby paving the way to enter new markets. He also believed that involving POSCO E&C for construction and POSCO International for operations would maximize group-wide synergy. He further helped open a new market for ship applications by driving the use of high-manganese steel in LNG fuel tanks for LNG-powered vessels.
Hanwha Ocean (formerly DSME) was initially hesitant to adopt the new material for LNG-powered ships, as safety assurance is critical for such large-scale vessels. During his term as POSCO CEO in 2020, Chairman Chang met directly with Hanwha Ocean’s top management and strongly advocated for the safety and reliability of the steel. As a result, in 2022, Hanwha Ocean became the first in the world to use high-manganese steel in LNG fuel tanks for a very large crude carrier (VLCC), which was followed by its application in container vessels.
* Track Record: Operational data collected after applying newly developed technologies or products under real working conditions
Q. Beyond the current market, what are the growth prospects for high-manganese steel?
Outside the LNG value chain, POSCO is leveraging the wear resistance and non-magnetic properties of high-manganese steel to explore new markets. Despite severe deformation, its non-magnetic properties do not deteriorate, which enhances stealth capabilities when applied to submarines, warships, and military tanks, thereby pushing for demand expansion as a material for the defense industry.