With increasingly strict car emissions & safety standards, car makers have been looking for new ways to make cars lighter, stronger, and more eco-friendly. In doing so, they have begun experimenting with new materials to manufacture their cars. Aluminum, magnesium, and carbon fiber all offer certain benefits to car makers and owners; however, they also present new barriers in the form of price, supply, and production emissions.
Since the inception of the auto industry, steel has been used to manufacture cars because it is strong, manufacturable, and durable. Also, because roughly 55-60% of a car’s weight comes from steel, it is an obvious place to make lightweighting a priority, which is exactly what has happened. Recent innovations in steel production technologies have created solutions that are lighter, stronger, and more environmentally friendly to produce.
Steel Alternatives Present New Obstacles for Car Manufacturers
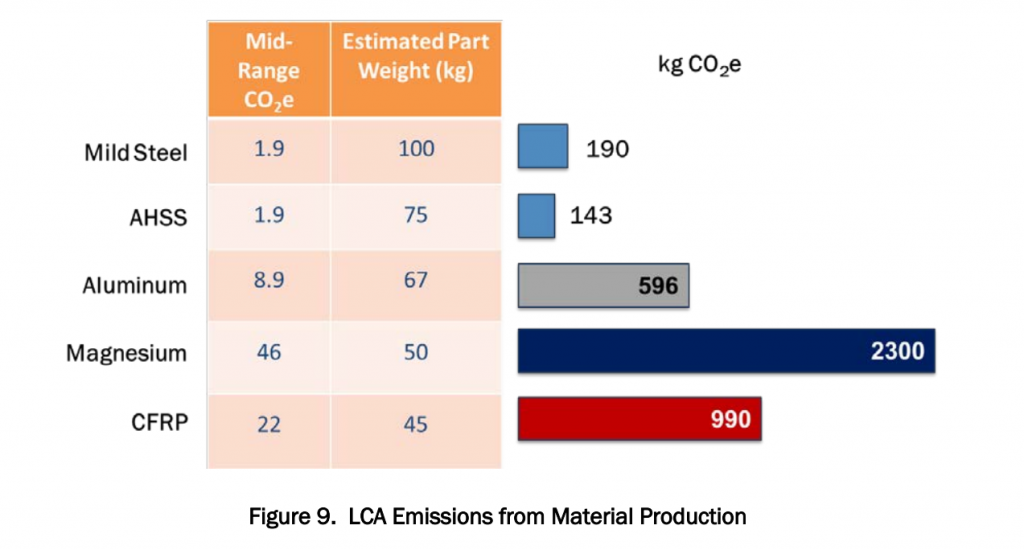
Advanced High Strength Steels (AHSS) provide the most eco-friendly alternative for car makers in material production. (Chart courtesy of AutoSteel)
As the auto industry adapts to new government regulations and consumer expectations, many have been looking toward alternative materials to step in as a substitute for steel. However, each material carries both benefits and drawbacks that they must constantly weigh as they seek to strike a balance that adheres to safety & emissions regulations and consumer demand.
Aluminum, magnesium, and carbon fiber composites are all being used to various degrees in recent auto designs. They have become attractive as lightweighting has become more of a priority for car manufacturers; however, there are tradeoffs.
Certain types of aluminum can be weaker, more expensive, and less formable than some steels. Magnesium, while lighter than both steel and aluminum, is also more expensive. In addition, extraction of magnesium can emit more than 20 times more carbon emissions than steel. Lastly, while carbon fiber composites offer the most in lightweighting potential, it is still prohibitively expensive for mass produced cars, and producing carbon fiber is 14 times more energy intensive than steel.
Advanced High Strength Steel Offers Lightweighting Solution
Typically, to make steel lighter, sacrifices had to be made in strength and ductility. However, recent innovations in advanced high-strength steels (AHSS) have been able to bridge that gap. AHSS offers lightweight solutions with high ductility coupled with high tensile strengths that can go beyond 1,000 MPa – meaning it can withstand more than 100 kilograms-force per square millimeter.
In addition, compared to alternative materials used in autos, AHSS offers the most eco-friendly option for car markers. It has the lowest production emissions and because it is infinitely recyclable and durable, it can be used in multiple applications throughout its life cycle.
AHSS grades allow car manufacturers to achieve a new level of strength, ductility, and durability in steel that is also lighter and more eco-friendly due to improved production efficiencies.
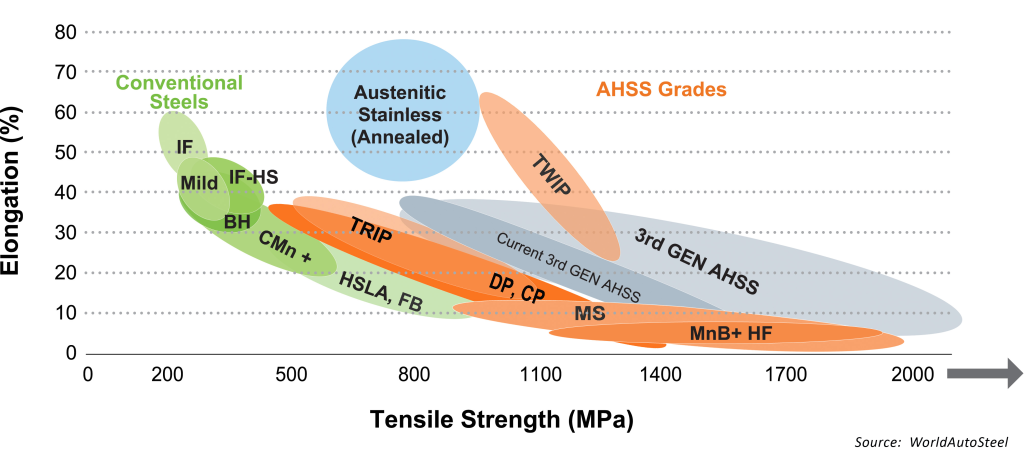
Third generation AHSS provides both high tensile strength and elongation. (Chart courtesy of World Autosteel)
The Third Generation of AHSS
Recently, engineers and researchers have been working to improve the balance between strength and elongation in AHSS. Typically, conventional mild steels offer superior elongation with less strength, whereas previous AHSS offered superior strength with more elongation and ductility.
The third generation of AHSS is bridging that gap, producing steel that is both incredibly strong and ductile at the same time. Typical mild steels have a tensile strength of around 300 MPa, which means it can withstand up to 67 pounds per force per square millimeter. On the other hand, new third-generation AHSS typically have a tensile strength of 800-1500 MPa (up to 300 pounds per force per square millimeter) with a similar amount of ductility.
In tensile strength measurements, 1,000 megapascals equals 1 gigapascal. Steel that has a tensile strength over 1,000 MPa is often referred to as GigaPascal steel. This type of AHSS is both super strong and also lightweight.
GigaPascal Steel and the Future of Auto Manufacturing
GigaPascal steel represents the cutting edge of steel technology and the future of auto manufacturing. Its high strength and lightweight properties make it safe and efficient. It provides car makers the material they need to meet efficiency and safety standards, with significantly fewer production emissions.
Two weeks ago SsangYong Motor unveiled their new G4 Rexton SUV at the Seoul Motor Show. They partnered with POSCO to develop the core body frame parts using its new POSCO GIGA STEEL. The SUV was designed so that 63% of the body contains POSCO GIGA STEEL – a first for the auto industry, but not the last.
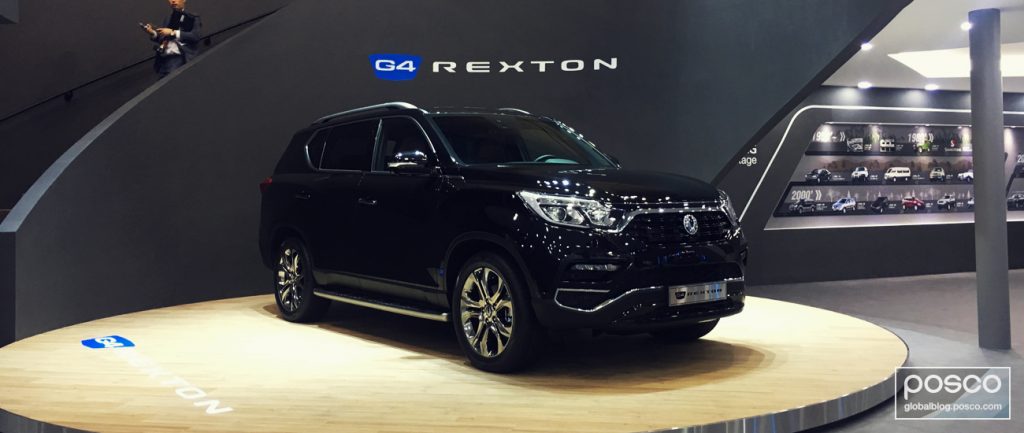
SsangYong Motor’s G4 Rexton is unveiled at the Seoul Motor Show in March 2017. It is the first vehicle to be made with up to 63% giga steel.
As the auto industry seeks to build more efficient and safe vehicles, advancements in steel technology have emerged to meet their needs. Balancing efficiency, strength, weight, and price – steel continues to be the preferred material in auto manufacturing.
Throughout April & May, The Steel Wire will explore the uses and benefits of AHSS, POSCO GIGA STEEL, and what POSCO is doing to lead the industry with new automotive steel solutions.