The Dawning Era of Metal 3D Printing
Traditionally, metal cutting methods have been used to manufacture machine components. The process would begin by shaping the metal through casting or welding, getting it to look as close as possible to the final product. To finalize the procedure, any unnecessary parts would be removed by a CNC (Computer Numerical Control) router. Using these types of cutting methods would accelerate the speed of production, but was considered wasteful since the majority of the starting material would be cut out and discarded. It is especially not appropriate for high-priced materials or materials that are difficult to cut.
Then there is additive manufacturing, which is a 3D printing technology that builds a final product through stacking layers of material, and then polished for a seamless appearance. The advantage of this method is that there is almost no waste of the material, which allows for the opportunity to create various prototypes without a separate mold or tool. A downside, however, is that it takes too long to manufacture, which makes it a tough choice for productivity.
Recently, General Electrics (GE), an American manufacturing corporation, officially joined the 3D printer business by assigning a merger of Arcam, a Swedish 3D printing specialized company, and the Germany-based SLM Solutions, to GE Aviation. Until now, 3D printing technology was primarily centered around plastic materials, but GE’s ambitious expansion into the 3D printing business indicates the rapid growth of new technology in producing major metal parts.
SLM solutions specializes in the Direct Metal Laser Sintering (DMLS) method – a printing technique that requires laser-firing a bed of powdered metal such as titanium, special steel, aluminum, cobalt chrome or nickel, melting together the powder to form a structure. Sweden’s Arcam has been manufacturing aircraft engine turbine blades by using the Electronic Beam Melting (EBM) method, which enables high-speed 3D printing by injecting 100 or so electron beams simultaneously into the metal. By combining the technologies of these two merging companies, a new high-speed 3D metal printer is surely to be developed in the near future.
Manufacturing Metal Parts with 3D Printing
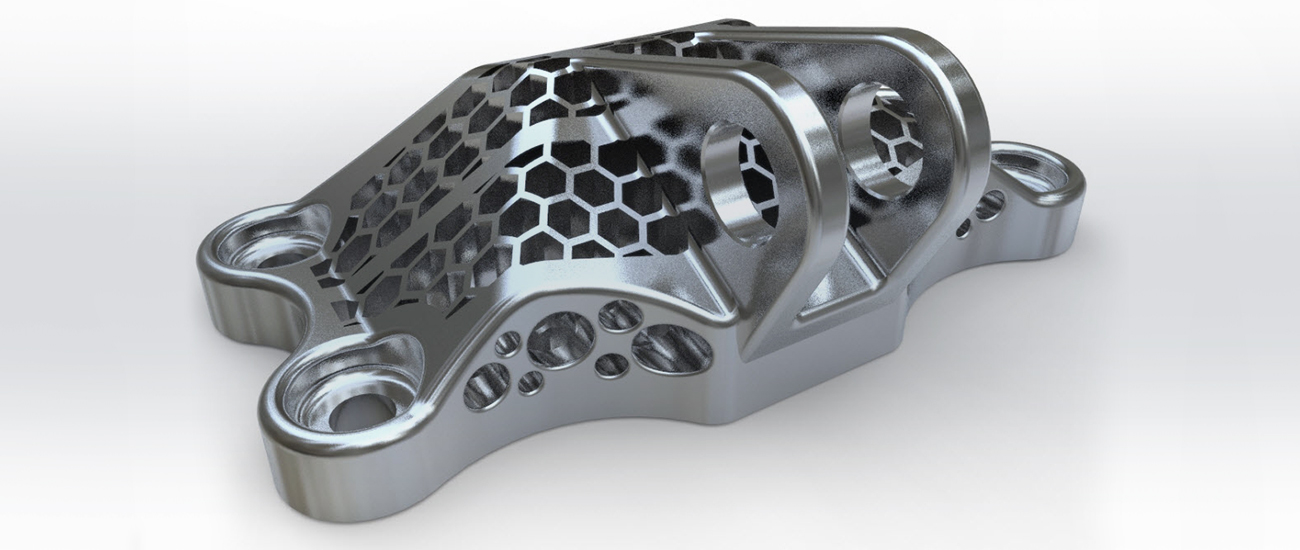
Image credit: WH Williams
The multinational special steel company, Voestalpine Group, recently established a new research and development center for the 3D printing of metal components. At this center, 3D printing manufacturing technology for automotive and aviation sectors, medical devices and complex metal parts will be researched.
Creating metal parts with 3D printing requires powdered metal of excellent quality. Raw metals initially undergo vacuum melting to become an alloy, which then becomes atomized by spraying high-pressure inert gas through a nozzle, turning into powder. The powder must appear very round and uniform, so the core of this technology is to meticulously control the nozzle’s injection amount, temperature, pressure, gas quantity and speed — all depending on the type of the alloy. The atomized powder is then classified by size, ranging from 20μm to 100μm, after several filtering processes.
Designing the metal components to be suitable for 3D printing is also important. Since the printer builds the part layer-by-layer, surfaces must fulfill the requirements for a laser or electron beam to scan through. As a fine diameter of light from the laser passes through the designed lines and surfaces, the powdered metal melts topically and creates a new layer on top of the previously laminated surface. At this point, the part may have an overall directional angle, so the order of drawing lines and angle within each layer is also very crucial.
During the 3D printing process, if the metal powder particles fail to melt completely or if there is a delay in clotting, minuscule bubbles could appear. The ability to withstand fatigue and fractures is important, as these metal components are supposed to support the weight of an object. Minor bubbles or gas pockets could be critical flaws. To achieve a perfect density by preventing bubble formation, the beam’s speed must be balanced and adjusted to suit different types of alloys.
This process demands additional attention when using metals of alloy elements. Unlike pure metals, alloys can experience a large gap in temperature and be able to exist in both solid and liquid states if their composing elements carry a great difference in melting points. In these cases, bubbles are easily made. Although alloy properties are very important, a composition of alloys with distinct melting points is required and the difference of these melting points must be maintained at a minimum.
That is, the development of suitable alloy metals for 3D printing, including technology for assigning a product’s cross section and designing a laser beam’s pass-through, is the bottom line of component manufacturing technology. In addition, the thickness of a component is closely related to the diameter of metal particles. Therefore, it is recommended to design the final product to be as thick as the particles it is made of, and vice versa.
The Future and Mission of 3D Printing
The 3D printing process creates an extremely complex structure that cannot be produced through conventional precision casting or processing methods. In that sense, even components of the same purpose can be designed with completely different structures using 3D printing. Thus, it is possible to reinforce the component’s functionality by reducing the component’s weight or enhancing its cooling performance.
It is now possible to manufacture components to produce their final shapes with special alloy metals, which had been impossible with conventional processing methods. As of recently, only a few types of metals were available for 3D printing. However, the low prices and excellent quality of metals now available will enable new developments of special steel 3D printing materials that meet the purpose of each component, expanding the spectrum of 3D printing.
As powdered metals accumulate together almost instantaneously, alloy elements do not diffuse or segregate. It is possible to obtain a supersaturated solid solution of alloy metal that has refined grains, which will allow for uniformity in texture.
Traditional metal component manufacturers, including GE, are now pursuing the 3D printing process as a transitioning path to digital manufacturing. They believe that 3D printing, a combination of precise mapping software, high-speed 3D printing devices and printing materials, will bring new solutions to their business.
Furthermore, enterprises are now being given the task to discover a multi-component special steel alloy that fits the manufacturing businesses’ demand. Various alloy powders are also expected to further develop so that 3D printing can be recognized as an optimized method for manufacturing components made of special steel in the future.
Written by science technology columnist Dr. Junjeong Lee
The opinions expressed in this POSCO Report piece are the author’s own and do not necessarily reflect the views of POSCO.