Last week in Building Bridges for Megacities Part 1, bridge expert Marco Rosignoli shared his insights on emerging megacities, their biggest challenges and what kinds of transportation infrastructure to expect in the coming years. In part 2 of his article, Rosignoli explores the challenges of bridge construction and the different types of construction processes and materials to expect in light of the increasing demand for bridges that emerging megacities will bring.
Biggest Challenges in Bridge Construction
The major challenges for building urban bridges are the availability of skilled labor, access to urban areas and environmental compatibility.
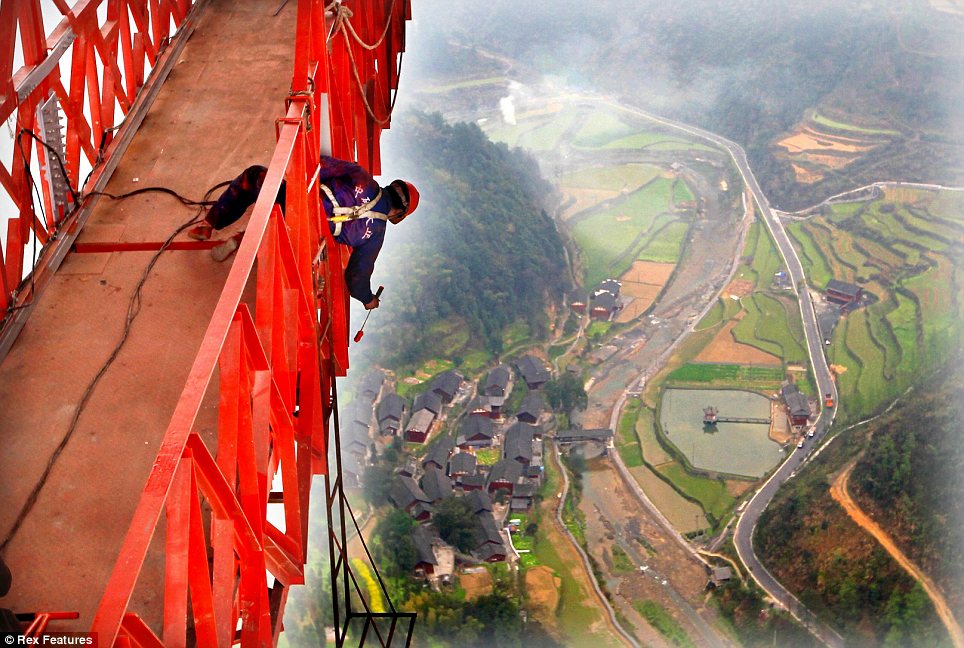
A worker paints the Anzhaite Long-span Suspension Bridge in Jishou, Hunan, China (Source: The Daily Mail)
Building bridges in megacities with the current scarcity of skilled labor will require a massive recourse to prefabrication. In a few circumstances, prefabricated bridge units will be transported on water with tugs and barges, which will allow the use of heavy, large units. In most cases, prefabricated bridge units will be transported on the ground through congested urban roads, which will lead to the use of light, modular units.
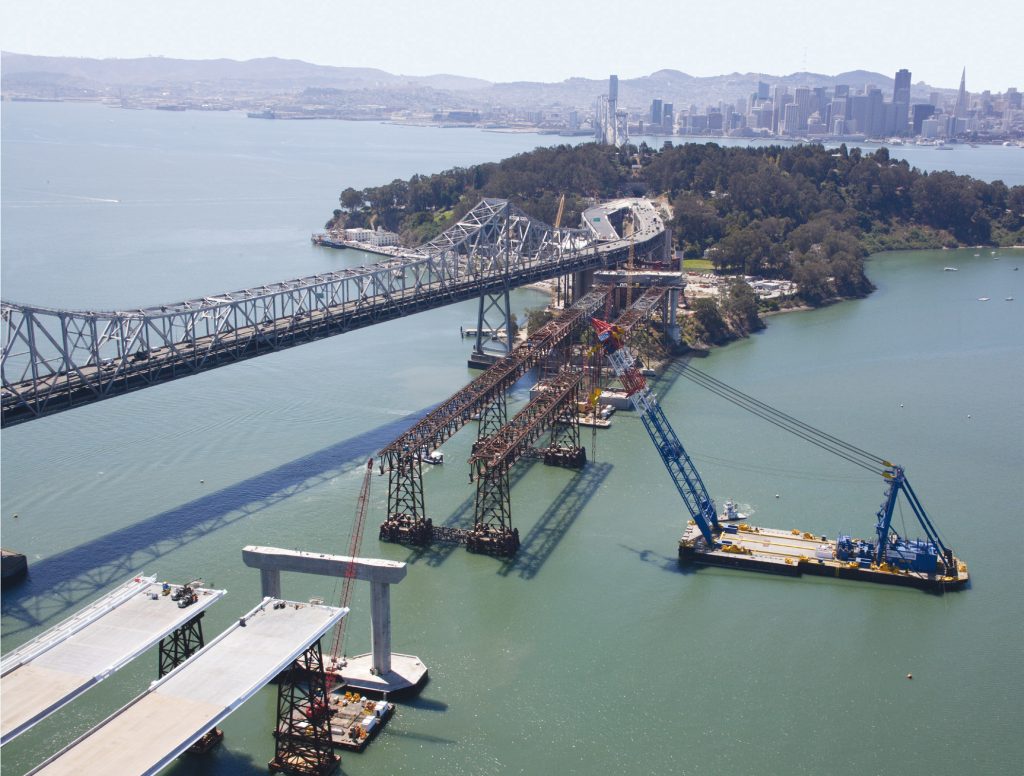
A floating crane lifts prefabricated deck sections onto the San Francisco-Oakland Bay Bridge (Source: San Francisco Public Press)
The availability of deck assembly areas and the interference of construction operations with adjacent infrastructure are additional challenges that will govern the bridge design process. As such, incremental launching construction from aerial platforms will see new applications, especially when combined with on-site welding of field splices among modular bridge units. The welding of field splices will also allow for optimized segmentation of bridge units, diminish the cost of field splices, and will relax the fabrication tolerances of the units.
Size Determines Cost, Cost Determines Everything Else
When constructing a bridge for an urban area, the size of a bridge governs the construction process. in turn, the construction cost of a bridge determines the materials and technology. Technology includes labor and investment in special construction equipment. The quantities of structural materials for a bridge depend on the design loads of the bridge, the flexural and shear span of the bridge units, and the mechanical strength of the material.
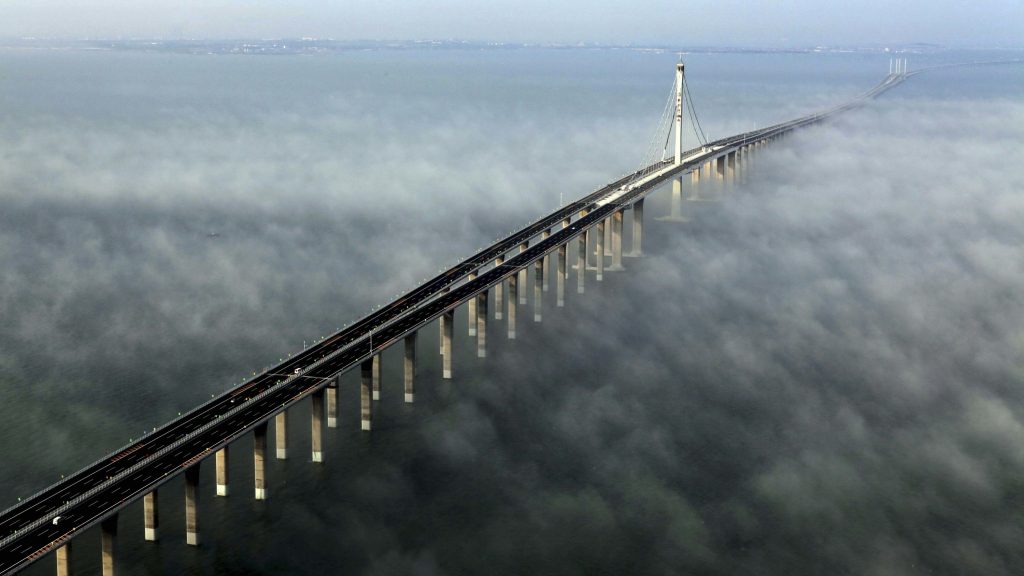
The Jiaozhou Bay Bridge in China is the longest sea-crossing bridge in the world (Source: The New York Times)
Small and large-scale bridge projects are both necessary in megacities and demand will only increase in light of the newly emerging megacities all over the world. When looking at both the construction of new bridges and the maintenance of existing bridges, the number of small-scale projects will definitely be larger than the number of large-scale projects. The impact these construction projects will have on the mobility of people and goods within a megacity is massive.
Although one may assume large-scale bridge projects with a larger budget will allow for design optimization and the efficient use of high-grade steels, scale economies in competition with other megacities will govern the availability of construction materials and workforce. Eventually, the scarcity of structural materials will lead to the efficient, eco-friendly use of steel and concrete in large and small-scale bridge projects alike.
Prefabrication and Incremental Launching for Bridge Construction
It is true that small-scale bridge projects have smaller budgets for technology, which limit design optimization and construction mechanization and increase the labor demand. Therefore, small-scale bridges will most likely be procured as packages of multiple bridges to acquire scale economies and a more efficient use of materials with the optimized design of modular units.
On the other hand, large-scale bridge projects allow for massive investment in special construction equipment, which will facilitate the prefabrication of modular bridge units in smart, eco-friendly factories. It will also diminish the labor demand of site assembly and the need for complementary infrastructure in an urban environment, as well as enhance the quality and durability of the final product.
Thus, large-scale bridge projects will be designed for modularity and have prefabricated standardized units with asynchronous production lines. Parts of the bridge will likely have different cycle times, just-in-time delivery, and require minimal site operations. Overall, construction technology and risk management of the trans-disciplinary relationships of mechanized construction will dictate the design of large-scale bridge projects in megacities.
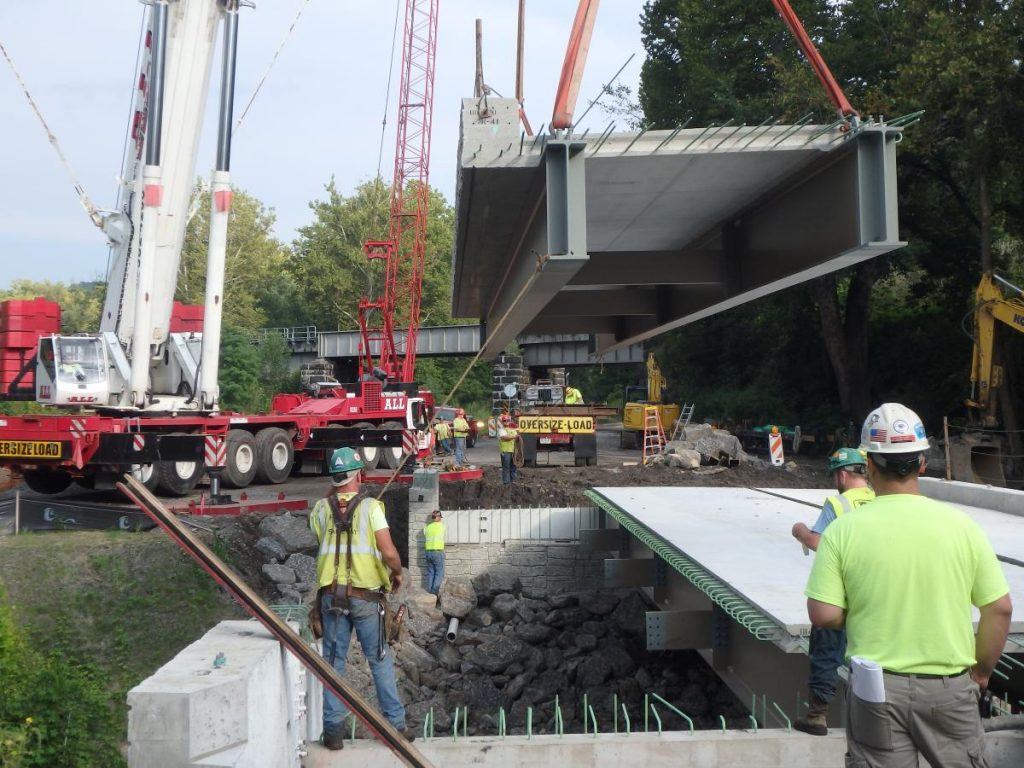
Workers assemble a prefabricated bridge in Pennsylvania, U.S. (Source: Roads and Bridges)
Small-scale bridge projects will take advantage of incremental launching technologies. Launched bridges minimize the interference between deck construction and the obstruction to overpass, and this is a major advantage for urban bridges designed to overpass congested infrastructure. Launched bridges do not require extra clearance to support the deck during construction, which simplifies connecting the bridge with existing roads and railways. Launched bridges do not require additional right-of-way as the deck is built behind the abutment and incrementally pushed into position. Additionally, the construction area is far from the infrastructure to overpass, which minimizes the risk for workers and the traveling public.
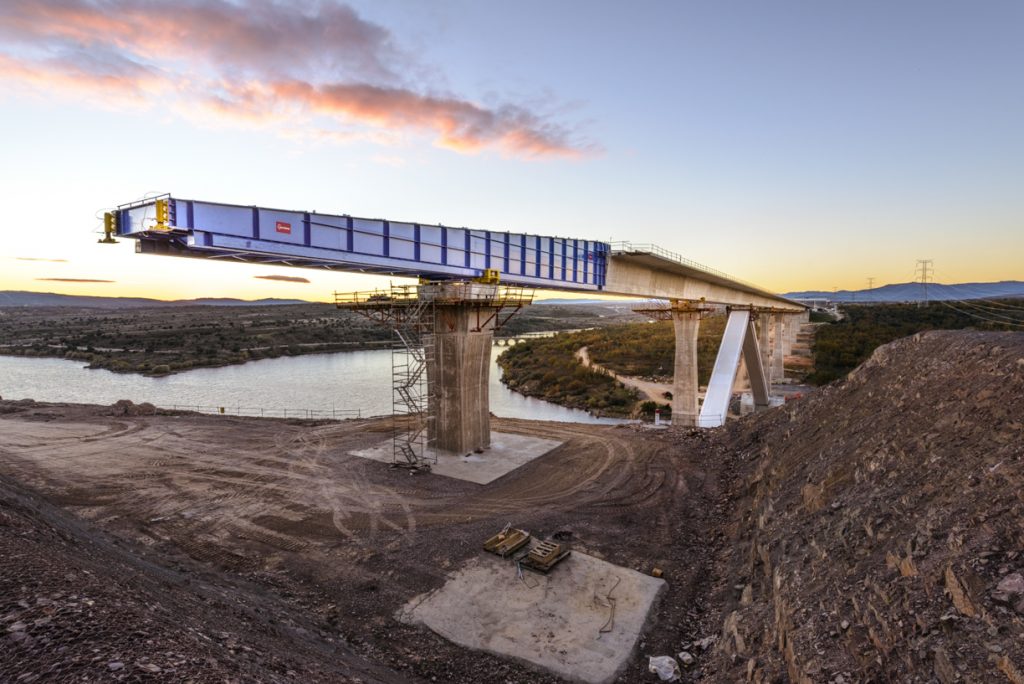
Incremental launching applied to a bridge deck construction process (Source: CARLOS FERNANDEZ CASADO S.L)
Materials For the Future Generation of Urban Bridges
Steel and concrete are the most common materials for bridges. In the field of steel bridges, high-grade steel will reduce the self-weight of bridge superstructures and the cost of piers and foundations. New composite systems and mechanized plate corrugation will increase the buckling capacity of unstiffened web panels and compression flanges to avoid the use of welded stiffeners.
In the field of prestressed concrete, new steels for rebar will offer higher strength and corrosion resistance to increase the durability and service life of the next generation of urban bridges. Post-tensioning materials are already extremely efficient, and the challenge will revolve around finding new duct systems and passivating materials to able to avoid the quality concerns raised by cement grouts.
Full-span precasting has been employed in thousands of spans of high-speed railway projects and in hundreds of spans of light-rail transit projects. Both steel and prestressed concrete bridges will be present in the mass transit systems of megacities, and both types of bridges are perfectly compatible with steel decks should high-grade steel turn out financially competitive over prestressed concrete in the megacity-oriented life cycle cost analysis.
Modern large-scale bridge projects are designed for 75 or 100-year service life in the USA. The use of renewable protective materials can easily meet this target in steel bridges, but the evolution of design loads and service conditions of urban bridges is hard to predict. Steel bridges offer a major advantage over prestressed-concrete bridges from this point of view, as they are more adaptable and can be modified, strengthened and adapted to new use conditions.
Marco Rosignoli is an expert in bridge design, construction, forensic engineering, consulting and education, with over 37 years of experience in 21 countries. |
Don’t miss any of the exciting stories from The Steel Wire – subscribe via email today.
- Anzhaite Long-span Suspension Bridge
- Bay Bridge
- bridge
- bridge construction
- bridge material
- china bridge
- city bridge
- concrete
- construction
- design
- durability
- globilization
- hunan bridge
- infrastructure
- Jiaozhou Bay Bridge
- Jishou bridge
- Marco Rosignoli
- megacities
- megacity
- megacity bridge
- megacity infrastructure
- oakland bay bridge
- Prefabrication
- San Francisco
- san francisco oakland bay bridge
- sea bridge
- sea crossing bridge
- service
- steel
- Steel bridge
- steel construction
- steel infrastructure
- steel megacity
- steelcity
- strength
- technology
- urban bridges
- urban construction
- urban development
- urbanization