POSCO Group does its best to develop technologies that contribute to safety and carbon neutrality. We introduce POSCO Group’s excellent new technologies to create a better world! In this edition, we introduce POSCO’s steel vertiport, an urban UAM takeoff and landing hub that not only has strength, durability, and cost effectiveness, but also incorporates prefab construction for enhanced usability.
With worsening urban traffic congestion and environmental issues around the world, urban air mobility (UAM) is gaining attention as a solution. The most notable UAM vehicle is the electric vertical takeoff and landing aircraft (eVTOL).
It requires a specialized structure, called a “vertiport,” for safe urban takeoff and landing of eVTOL. A vertiport is more than just a landing pad, it serves as an urban airport that provides terminal spaces for passenger boarding, as well as facilities for aircraft charging and maintenance, as a vital part of the UAM infrastructure.
In aviation, there is a critical time known as the “fatal 11 minutes when accidents are most likely to occur, which is 3 minutes during takeoff and 8 minutes before landing. UAM flights are also vulnerable to the turbulence created by airflows interacting with the vertiport during takeoff and landing, which poses a risk of collision with obstacles. This highlights the need for a vertiport structure designed with superior durability to withstand unexpected situations. Until now, aluminum has been the main material for vertiports due to its light weight and durable properties. However, aluminum was difficult to commercialize because it was expensive.
POSCO developed the “steel vertiport” with the goal of creating a lightweight yet robust vertiport using steel. By leveraging this material, they achieved a product with similar strength to aluminum, but with a thinner structure and at less than half the cost of aluminum alternatives. Furthermore, they incorporated PosMAC, POSCO’s high-corrosion-resistant steel, which has 10 times the corrosion resistance of conventional galvanized steel and significantly reduces maintenance concerns.
Vertiports that are typically installed on top of buildings, rather than on the ground, are referred to as elevated vertiports. These structures are characterized by modular assembly, minimizing the need for heavy equipment and assembly because materials must be lifted to higher floors. POSCO’s steel vertiport is designed as a 15-meter square platform divided into 18 modules, which are pre-fabricated in the factory and assembled on-site. This prefab construction method enhances the efficiency of both the installation and dismantling processes.
*Prefab (short for pre-fabrication): A construction method where components are manufactured in a factory beforehand and the structure is completed on site by assembly alone.
Steel Vertiport Technology Validated With Public Performance Testing
Last June, POSCO conducted the first-ever public performance verification of its steel vertiport in Goheung, South Korea. POSCO proved its technological expertise by successfully completing the entire process of the steel vertiport, from design to construction, for performance verification in only 20 days. It was a challenging feat, but POSCO was able to complete it within the tight timeline thanks to proactive collaboration with manufacturing plants and construction partners during the development phase. A key feature of POSCO’s steel vertiport is its enhanced construction efficiency, achieved by integrating DfMA* and modularization technologies. Let’s take a closer look at the public performance verification of POSCO’s steel vertiport.
*DfMA (Design for Manufacture and Assembly): A design approach that considers the manufacturing, transportation, and installation of components and modules at the outset of structural or architectural planning.
During the public performance test, real-time data were collected to measure the durability of the steel as a 5-ton helicopter landed on the vertiport. Remarkably, the steel exhibited outstanding strength, with no deformation even to a tolerance of 1 cm. Observers from the Korea Aerospace Research Institute and Lotte E&C consortium praised the steel vertiport and acknowledged its potential for application in the future UAM industry. Additionally, feedback from the helicopter pilot affirmed that the steel vertiport matched conventional helipads in terms of robustness, noise, and vibration, which once again showed the stability and superiority of POSCO’s steel vertiport.
Steel Vertiport Potential Recognized in the Global Market
The potential of the steel vertiport has been showcased not only domestically, but also internationally. At last month’s 2024 World Smart City Expo (WSCE) Vertiport International Forum, POSCO presented real-world applications of its steel vertiport design and received global attention to this innovative solution. Following POSCO’s presentation, there was a flurry of questions from the audience, including inquiries about commercial partnership opportunities. After the forum, a steel vertiport mock-up was displayed at the Airport Corporation’s promotional booth. This model, featuring a frame and columns integrated with POSCO’s high-strength trusses, attracted considerable interest from attendees for its structural performance as well as its architectural aesthetics and sense of openness.
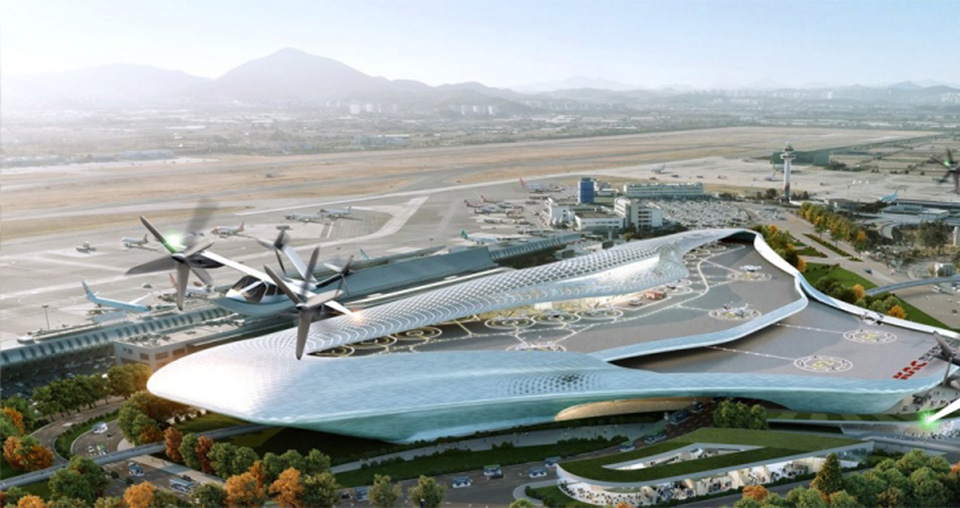
▲ A virtual image of a vertiport ©Korea Airports Corporation.
Building a Sustainable Vertiport Operating System with POSCO’s Products and Solutions
Since a vertiport is a structure in its own right, it must also address the demand for improved energy efficiency, a focal point in modern construction. In light of this, POSCO is exploring options to integrate solar panels directly onto the vertiport and is evaluating the application of BIPV* systems, which would combine solar energy generation with the terminal’s exterior cladding. POSCO is also considering an innovative wind energy solution by harnessing the strong downdraft, or “downwash,” generated as helicopters descend. The implementation of such ideas will require the steel vertiport to have exceptional durability and structural integrity, and POSCO is committed to conducting thorough research to realize these concepts. With these advancements, POSCO’s steel vertiport is ready to shape the future of UAM infrastructure. We thank you for your support.
*BIPV (Building Integrated Photovoltaic): A power generation system that seamlessly combines energy production with architectural design by incorporating solar modules as building materials.
Part 1. Prevent safety accidents at the source! Safety braking system for forklifts
Part 2. Capturing Minute Cracks with Drones! Apartment Exterior Wall Management Solution: POS-VISION
Part 3. Dreaming of independence in battery core materials! Localized artificial graphite anode material technology