POSCO Group does its best to develop technologies that contribute to safety and carbon Reduction. We introduce POSCO Group’s excellent new technologies to create a better world! In this episode, we explore POS-VISION, a solution from POSCO E&C that utilizes drones equipped with high-definition imaging equipment to manage the concrete exterior walls of apartments.
Developed by POSCO E&C in January 2024, POS-VISION utilizes drones equipped with high-definition imaging equipment to precisely identify and manage the width, length, and location of cracks in the concrete exterior walls of structures such as apartments and bridges.
POS-VISION combines drone operation technology with artificial intelligence to enable crack recognition, high-definition image processing, and the elimination of false detection elements. This integration allows construction managers to access detailed information about the exterior walls of buildings, facilitating seamless quality management.
In January 2022, an incident involving the collapse of an apartment by Company H highlighted the crucial need for enhanced quality management of large concrete structures at POSCO E&C’s New Growth Future Technology Research Institute, Construction Automation Section.
Quality checks were thorough in indoor areas such as underground parking lots and individual units where cracks were visible, but the exterior walls presented challenges due to less visible cracks. These exterior wall cracks are significant not only for structural stability but also for their potential to cause leaks and corrosion. Unaddressed, they could lead to concrete deterioration and exposed rebar, jeopardizing the brand’s reputation. Prompted by these risks, the team embarked on an in-depth investigation of these quality management challenges, developed the concept of POS-VISION, and initiated full-scale technical development.
Initially, the team conducted thorough research on the condition and management of cracks in large concrete structures, such as apartment buildings. According to standards for assessing defects in residential housing, cracks measuring 0.3 mm or wider are classified as defects. Moreover, any penetrating cracks,* even those under 0.3 mm wide, also qualify as construction defects. This highlights the need for precise crack measurement technology, as different widths of cracks require different repair methods.
*Penetrating Cracks: These are cracks that run from an exterior to an interior surface within the same section and are often seen as temperature-related in thick walls or as shrinkage cracks in slabs.
In response, the team developed a sophisticated AI-driven image analysis technology. They refined POS-VISION’s accuracy through tests with real-world field data. For estimating the dimensions of cracks in images taken by drones, they applied geometric principles inherent to the camera’s functioning, enabling precise measurements of the distance between pixels.
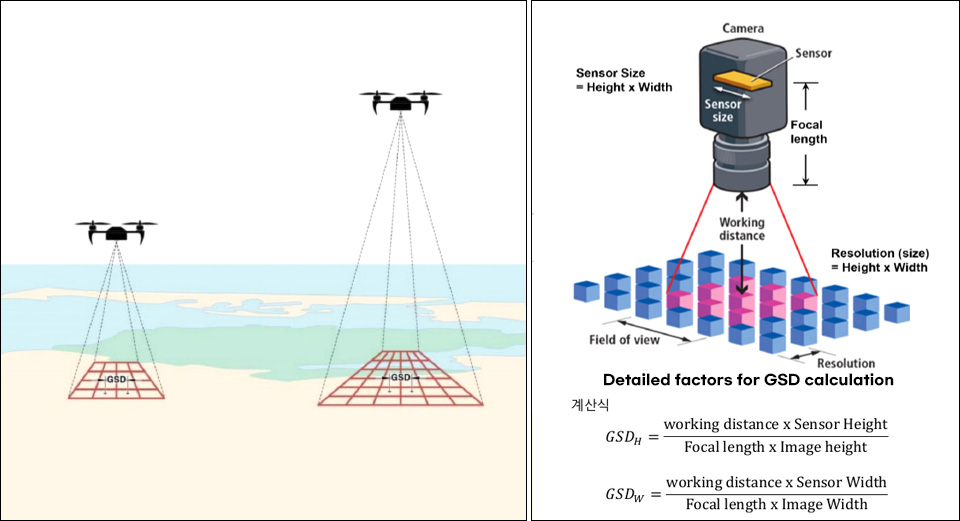
▲Conceptual diagram (left) and GSD calculation formula that formed the basis for the development of POS-VISION technology.
To measure the actual distance between pixels, the ground sample distance (GSD) concept was utilized. This term describes the distance between the centers of two adjacent pixels A smaller GSD indicates higher precision and accuracy of the data. Nonetheless, there were challenges due to the physical constraints encountered when drones flew close to buildings for detailed shots. To address these issues, the team implemented a super-resolution algorithm that upgraded the images to a resolution superior to their original quality. They used the outcomes from field trials as a foundation for further validation and enhancement, thus improving the system’s reliability. Through multiple tests, it was established that the best distance for the drone from the building should be 4 meters. This distance allowed for accurately distinguishing between cracks measuring 0.3 mm and 0.5 mm, which is vital for selecting the correct concrete repair and reinforcement techniques.
*Ground Sample Distance (GSD): Measures the distance between the centers of two consecutive pixels.
Besides considering the shooting distance, several other factors were important. Drones, which rely on satellite signals to navigate and determine their positions, face challenges within high-rise apartment complexes where these signals are often weak. This increases the potential for drones to collide with buildings. Therefore, the expertise and proficiency of the drone operators play a vital role in achieving safe and precise measurements.
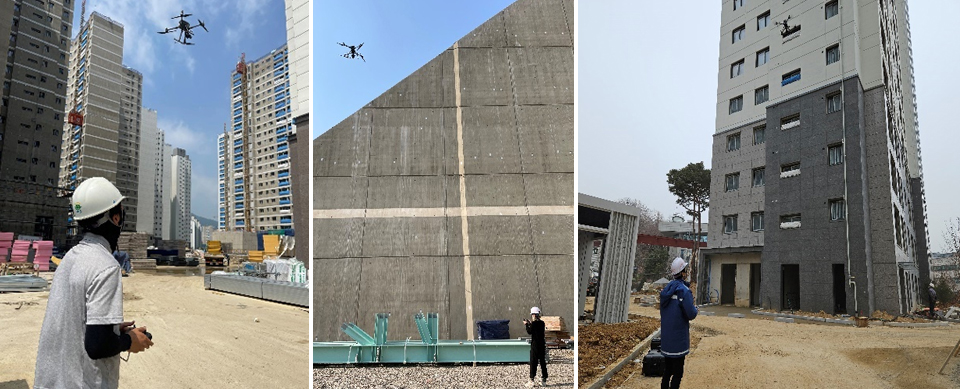
▲Inspecting cracks while maneuvering the drone.
Given that the operations take place outdoors, weather significantly influences the process. Windy conditions heighten the risk of drone collisions, while cloudy, rainy, or snowy weather complicates visibility. Additionally, operating drones for extended periods in extremely hot or cold temperatures is challenging. In response, POSCO E&C is considering the development of autonomous drones designed to handle these challenges and environmental factors effectively.
To help users swiftly pinpoint crack locations in numerous images, the team innovated a user-friendly technology. Initially, they used a crack positioning method on a 3D site model, which involved extra aerial photography and model creation, consuming over a day.
This approach was impractical for urgent on-site needs related to crack detection. Therefore, the team abandoned the 3D method in favor of a more efficient technique, displaying crack positions on elevation views by unit. This adjustment significantly sped up the process of investigating cracks and deriving results. For a conventional multi-story residential complex of about 25 floors, typically, image stitching* of more than 300 front-view images is required to secure a photo overlap rate above 50%. By employing the POS-VISION technique, marking crack positions on elevation views is achievable without the need for overlapping images. This method decreases the total number of required images by over 40% and greatly diminishes the time spent on post-processing.
*Image Stitching: This technique combines several images to create a single panoramic photo.
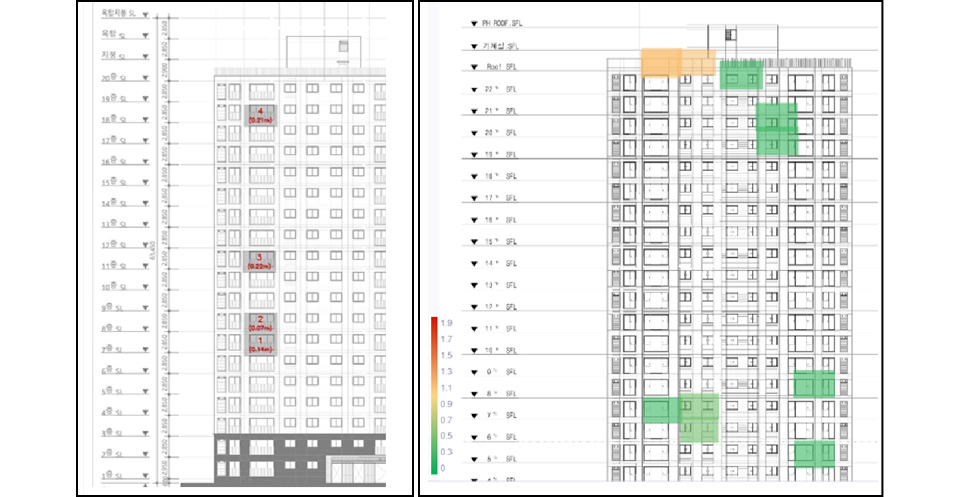
▲Elevation view showing crack display (left) and another elevation view enhanced with a heat map for improved crack visualization.
POS-VISION has enhanced user convenience by implementing heat maps* based on the volume of crack occurrences, helping users quickly pinpoint areas needing urgent inspection. This method assigns different colors to each segment according to the severity of the cracks. Previously, crack detection images and occurrence counts were displayed on the site elevation view, offering users the option to click on images for more detailed information. However, the increase in crack data made this process cumbersome. The adoption of heat maps solved this problem by facilitating the efficient management of data and accentuating critical areas, even with the proliferation of data. This modification has been well-received in the field for its notable improvement in efficiency.
*Heat map: This visualization tool uses color coding—red to indicate areas requiring review and green for areas without issues—to assist users in easily identifying sections needing attention.
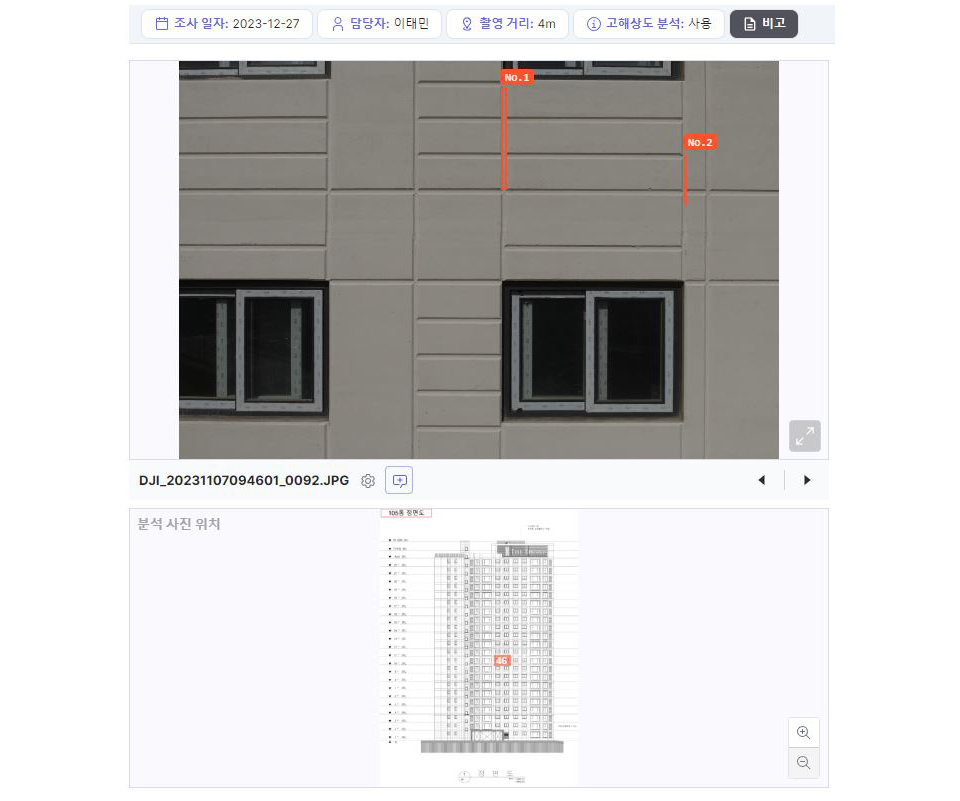
▲Crack images analyzed by POS-VISION on exterior walls.
POS-VISION has been utilized across nine sites involving 41 concrete structures, which include 39 buildings at seven construction sites, bridge slabs at one infrastructure site, and a coal storage facility at a single plant site. Having captured 24,641 images, the system has effectively identified cracks in areas that were challenging to detect before, thereby markedly enhancing construction quality at POSCO E&C.
The launch of POS-VISION has successfully addressed the oversight issues in managing the quality of building exteriors. This technology, suitable for various structures such as residential complexes, bridges, and highways, enables crack detection in areas difficult for humans to reach, thereby preventing potential risks ahead of time. Looking forward, POS-VISION aims to widen its scope and act as a “third eye” in identifying and mending quality issues in welding among other sectors.
POSCO E&C is advancing the development of autonomous flying drones to enhance the reach and efficacy of POS-VISION. Equipped with autonomous image-capturing capabilities, this technology promises to expand to more sites and boost operational efficiency. Moreover, employing autonomous drones equipped with vision sensors might solve the limitations associated with indoor crack detection and human errors. POSCO E&C is dedicated to maintaining quality and safety on-site through continued technological advancements and venturing into new domains.