A sturdy yet slender steel table? Sounds contradictory but for the designers of AirTable, Carlos Baňon and Felix Raspall, such contradiction was at the very core of their creation of the AirTable. They are both Assistant Professors at Singapore University of Technology and Design – and within the SUTD, they founded AirLab, an Artificial Intelligence Research Lab in 2016.
In just three years of founding the AirLab, they went on to compete in the prestigious 2019 Singapore Design Award with prominent contestants from across the globe. AirLab made it to the finalist on their first try – the stainless AirTable was one of their entries.
POSCO Newsroom reached out to the designers of the stainless AirTable, who shared stories about their design process and philosophy behind the table, their interest in 3D printing, and experimentation with different materials. POSCO Newsroom reports:

Designers of the stainless AirTable: Carlos Baňon (left) and Felix Raspall (right)
l Team AirLab, the Finalist on 2019 Singapore Design Award
Congratulations on becoming the Singapore Design Award Finalist! Tell us more about the award, and about your entries.
Thank you! Singapore Design Award has been acknowledging outstanding design practitioners and students from across the globe. The award itself has been around since 1988 and remains as one of the leading design awards in Southeast Asia. We are so thrilled to join the finalists along with a very qualified group of architectural and design firms.
For the SDA 2019, we presented a broad scope of risk-taking projects, exploring practical 3D-printing techniques applied to architecture and furniture design, in combination with parametric design thinking.
Our entry was a selection of built works that we designed and fabricated at our firm, AirLab at the Singapore University of Technology and Design. Via proof-of-concept designs, all the works, including the stainless AirTable explore relations amongst geometry, material, and workflows across a wide range of scales and functions.
l The Product: Stainless AirTable
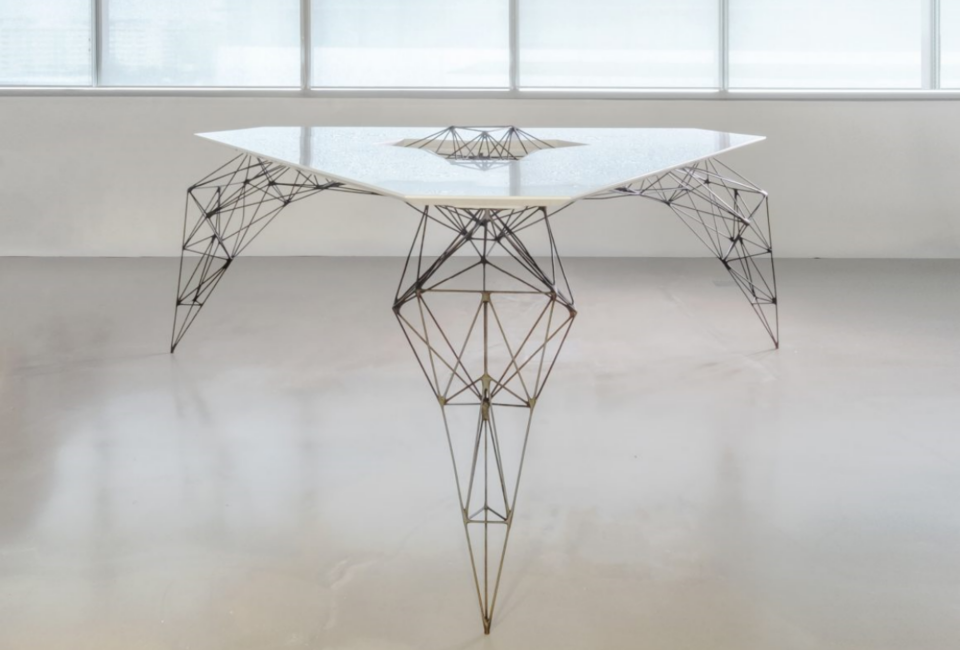
Stainless AirTable, structure (Source: AirLab @SUTD)
Let’s discuss the stainless steel AirTable, which was included as one of your submissions to the SDA 2019 Award. Looking at the photos of the stainless steel AirTable, it’s incredible how a massive tabletop of 120 kg can balance on just three small tips. How did you achieve this structural balance?
We always work with the idea of lightness and smooth load transfer as a premise. For the AirTable, the challenge was basically how to transfer the heavy load from the table top to just three small points on the floor.
So we developed a 3D mesh capable of carrying the weight in a distributed manner, trying to avoid overstressing any particular spots. We employed a structural strategy where the loads are transferred through very thin elements to the ground. In our initial concept models, we wanted to manifest the contrast between the heavy top piece of white Corian and the extreme lightness of the 6mm stainless steel profiles.
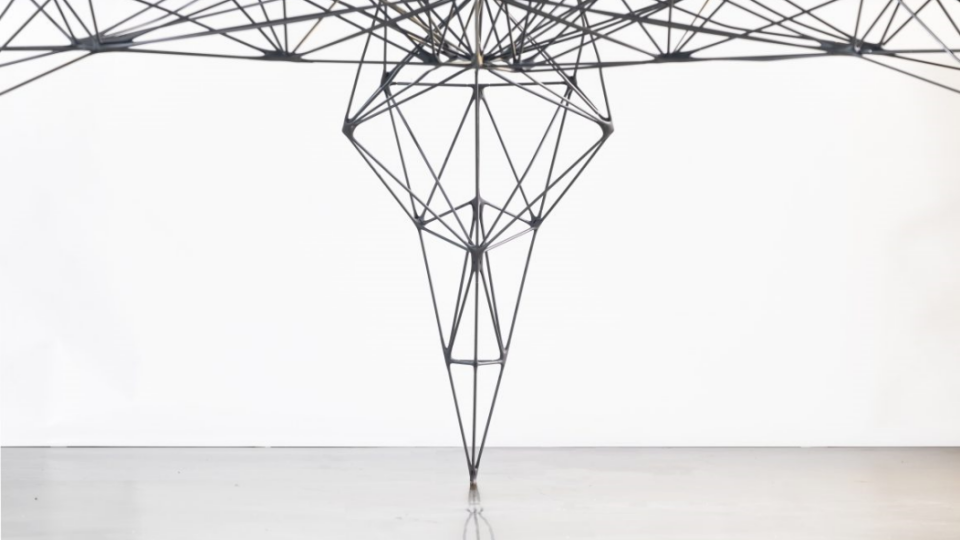
Stainless AirTable (Source: AirLab @SUTD)
For the overall strategy, we used a structural topology capable of transferring the loads gradually. We made design variations and tested the structural performance on the computer. Those that performed better were chosen, and we subsequently built variations out of them – not too dissimilar from the evolutionary process of natural selection. We also worked with physical models to actually feel the structure and to visualize its structural properties alongside aesthetics.
What were some of the advantages of working with stainless steel?
The good thing about stainless steel was its structural stability and performance. In our test, the structural performance of stainless steel was excellent, rendering surprisingly sturdy result. Deflections result was smaller than our initial calculations, so we were able to reduce the number of ‘divided’ sections for each component.
And any challenges? If yes, how did you overcome them?
This is always a key part, pertaining not only to our designs, however. Connecting different elements is sometimes the bottleneck of a system, and we have tried many alternatives using epoxy (high-performance adhesives widely used in buildings and constructions) – or we threaded components which was the case for the AirTable. The challenge when you are connecting more than 15 bars in a single node, you cannot slot inside the connector if the material is too rigid to bend. That problem is solved in the upcoming AirMesh stainless steel pavilion, where we conceal a bolt inside the structural bar, so it fits nicely with less than a millimeter tolerance.
The AirTable was initially designed as a hot desk. How is it being used now, by whom? Do you have any plans for broader distribution?
It is indeed being used as a hot desk. Mainly people from DmanD (SUTD Digital Manufacturing and Design Center, who was also behind the creation of the stainless AirTable) are using the desk to have quick conversations, using their laptops on it. The height of AirTable is 1.05 meters, taller than a standard desk. We believe it works very well for its purpose, being closer to the height of a bar counter than a typical desk.
As for the wider distribution, we got offers from LEGO and other industry partners that are interested in developing the prototype further, but it’s not yet crystallized, as it has just been presented to the public.
l White Spaces: The Seoul Connection
Back in 2017, AirLab participated in Seoul Biennale. Tell us about your experiences then.
‘White Spaces’ was the Singapore Pavilion exhibited at Seoul Biennale 2017. We designed the structure as a very lightweight mesh of thin bamboo poles. Conceptually, the mesh first occupies the whole room, but we carved it out to let the visitor pass and visit the content.
The whole pavilion was designed to be brought from Singapore in check-in luggage, so it had to be super light and compact when disassembled. Our students at the SUTD, as well as a group of students from Kookmin University, helped us with the assembly on site.
l What’s Next? Stainless Steel AirMesh
So what’s next for AirLab? Anything you can share with us at this time?
AirMesh is coming up. It’s a 3D-printed lantern — a contemporary interpretation of lantern in stainless steel. All the connective materials will be 3D-printed, and it is going to be the world’s first fully functional code-compliant structure of its kind. AirMesh will be erected in Gardens by the Bay in Singapore, this Fall.
l Creativity Charging at Full Speed
AirLab designers are not afraid of getting their hands dirty with new materials, constantly trying new approaches they firmly believe in, even if it largely remains an unchartered territory – like 3D printing. Thanks to the creative adventurers like the AirLab designers who’re tirelessly running at full speed even at this moment, the potential for our materials like stainless is endless.