POSCO, the only ‘Lighthouse Factory’ in Korea selected by WEF (The World Economic Forum), is now focusing on promoting ‘Smart Safety’ that supports safety activities to build a disaster-free workplace. They say that they are working day and night to improve the working environment of the steel mill where various types of risk factors exist and to prevent safety accidents.
POSCO has already introduced cutting-edge technologies such as artificial intelligence, smart wearable devices, and automated robots, and is trying to fulfill its social responsibilities by implementing safe steel mills based on ESG management. POSCO, you’ve got a plan!
POSCO, which recently declared safety first management, is implementing six major safety management measures including △shifting the process from production priority to safety priority, △thoroughly implementing work stoppage rights, △establishing a Safety e-Report, △expanding safety smart infrastructure, △strengthening safety management support for partners △substantializing safety training for employees.
POSCO judged that there is a limit to disaster prevention just by supplementing existing safety facilities or strengthening institutional strategies for safety compliance. Therefore, it is focusing on preventing safety accidents by applying Smart technology to existing safety activities such as ‘mechanization and automation of dangerous work’, ‘application of Smart Technology for danger prediction’, and ‘smartification of safety management’.
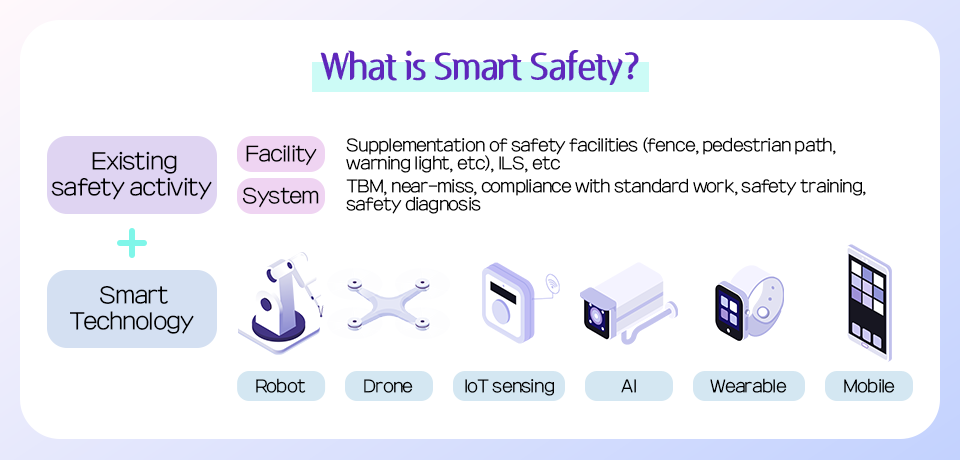
▲Safety activities incorporating smart technology that POSCO aims for
Now, let’s take a closer look at POSCO Smart Safety from A to Z.
l Mechanization and automation of dangerous work
First, POSCO is pushing for the development of automated devices incorporating smart technologies to replace manual work with a high risk of safety accidents and the ‘mechanization and automation of dangerous work’ by applying robots.
•Sticking coal removing Robot: Prevents falling risk
•Brushing Robot: removes impurities from slab surface at high temperature
•Quadruped robot: Detects underground culvert fire and daily inspection of blast furnace from an explosion
POSCO will also apply drones and expand its usage to inspect facilities at high places with high safety danger for workers, such as a chimney, pipe, and fuel & material inventory measurements. In addition, in the case of steelmaking processes that deal with molten metal at 1,500℃ or higher, the process of removing impurities and putting them into transport containers) was automated through image recognition and IoT.
Other continuous casting operations including refractory tube connecting operation (connecting molten metal to intermediate containers called Tundish before pouring it into molds), putting thermal insulation materials work, temperature measurement and sampling operation are also in the development of robots, and the operation of unloading iron ore and coal at 40m above ground is also being studied for automation.
l Danger Prediction Smart Technology
Smart solutions such as Smart Safety Ball, Smart Watch, Smart CCTV, and Smart Safety Vest are also in the process of application. They are all ‘Danger Prediction Smart Technology’ that can early detect workers’ insecure behaviors and dangerous situations and prevent disasters through prompt sharing.
Smart Safety Ball is the world’s first technology developed by POSCO, and it is a detector that indicates the presence of harmful gas by throwing the ball into the workspace before workers enter the enclosed workspace.
The size of the Safety Ball is similar to a tennis ball (60mm in diameter and 100g in weight), and the concentration of three gases including oxygen, carbon monoxide, and hydrogen sulfide can be determined. The measurements can be checked in real-time in a dedicated application on a smartphone or tablet, and the message is delivered to colleagues and managers at the risk level.
POSCO is demonstrating the device to the choking hazard site of the steel mill and plans to distribute the entire steel mill site and expand it to local industries and communities after legal certification is completed by June.
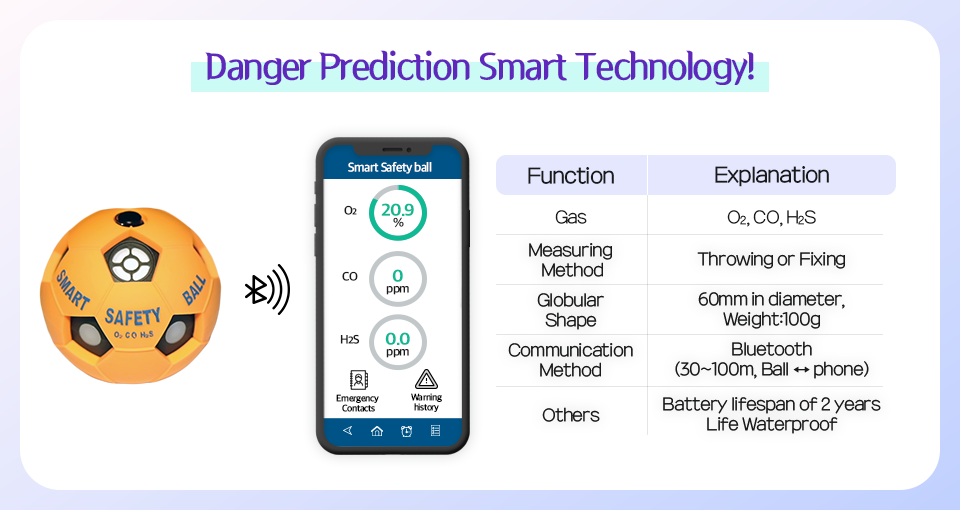
▲Real-time data transfer schematic and key functions of Smart Safety Ball
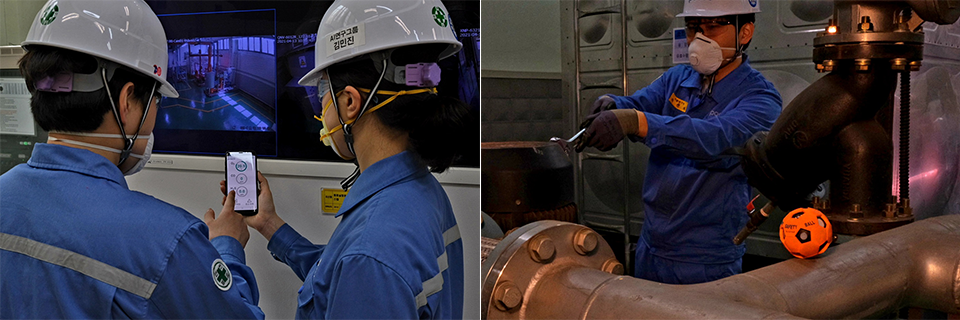
▲POSCO employees are working on real-time harmful gas measurements through smart safety balls and linked apps at the site.
In the case of Smart Watch, it has been distributed since last year to the steel mill and partner employees, as well as staff members who need health care. Its key function is to secure golden time by immediately sending rescue signals to colleagues around by detecting falls, heart problems, and falls in real-time. Through this, it is possible to supplement the system that used to periodically contact wirelessly or check safety through CCTV video during the fieldwork.
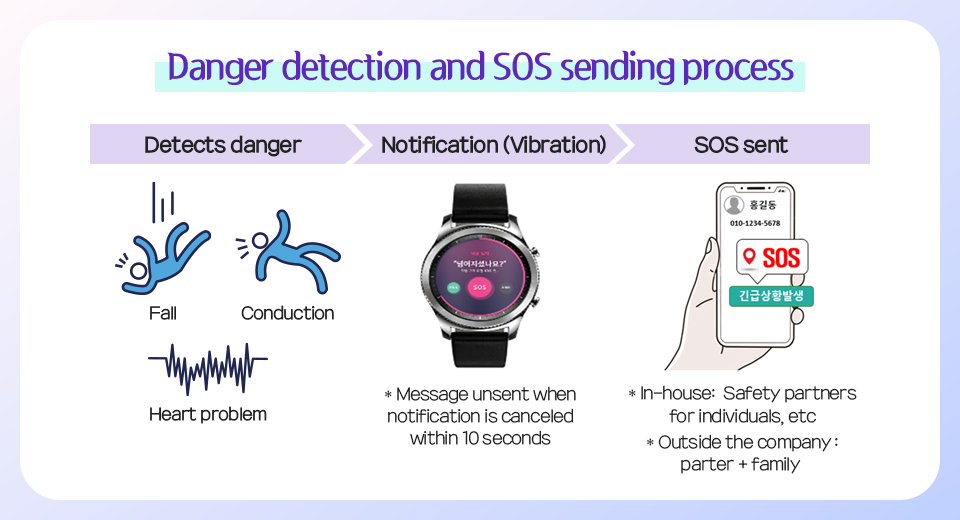
▲Danger detection and SOS sending process of Smart Watch
In addition, CCTVs are being installed in all repair operations in the steel mill, and Smart CCTVs equipped with AI image recognition models are developed to detect workers’ safeguards, entry into dangerous areas, and workers’ insecure Not wearing safeguards, intrusion into dangerous areas, abnormal behavior detection, behavior in real-time.
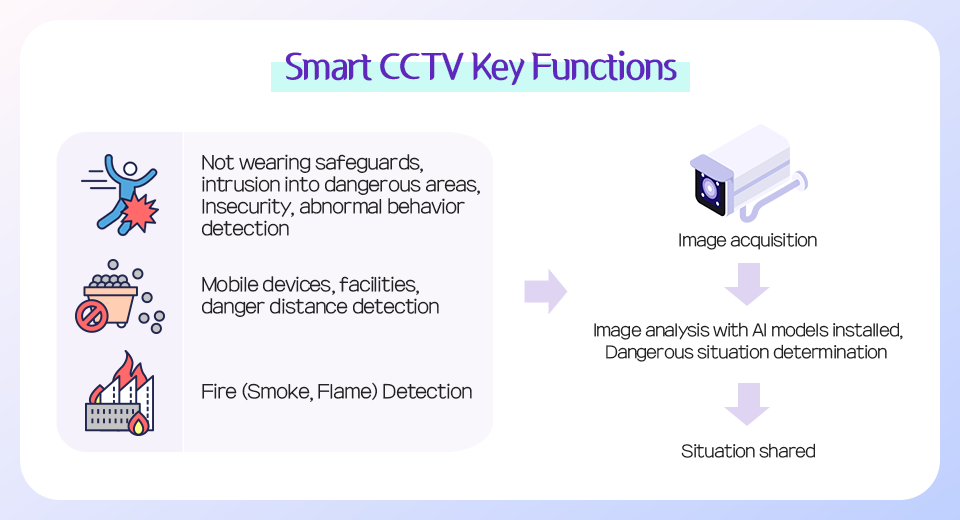
▲Smart CCTV Key Functions
It is also promoting to introduce Smart safety vests to remove workers’ safety blind spots during the field inspection. The Smart safety vest consists of a front-back camera, lantern, and LTE radio, and shares images in the cab in real-time through front back cameras. In case of emergency, the SOS sending function can be activated immediately, and in the future, the company plans to develop and install functions that allow drivers and workers to mutually recognize mobile (cranes, forklifts, etc) access situations.
l Smartification of safety management
Lastly, POSCO is promoting the establishment of an integrated safety management system and the smartification of safe work permits.
As the policy on industrial safety is strengthened, the target of safety management is expanded to suppliers (cooperation, service, and construction), and the asymmetry of information will be resolved by sharing and utilizing safety-related information horizontally.
In response, POSCO is establishing a Smart Safety Management Integrated System that can be shared by everyone who enters and leaves the steel mill. This system, which will be operated in earnest around next year, is connected to all safety-related in-house systems and is being developed to immediately recognize abnormal situations transmitted from gas detectors and wearable devices.
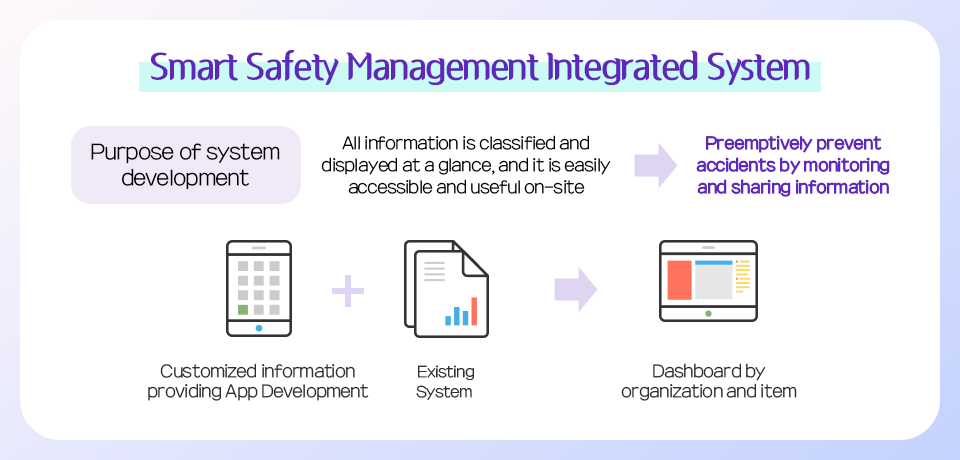
▲Smart Safety Management Integrated System Concept
It is also developing tool mechanization and automation for the safety of employees at actual work sites. To this end, it is pushing for 1,500 improvements such as forming a cooperative win-win support group to discover risk factors all at once and improving safety facilities, as well as designing and manufacturing jig & fixtures for heavyweight transportation and manual work assistance.
Also, it discovers QSS(Quick Six Sigma) improvement tasks to raise safety awareness and enhance safety improvement capabilities of partners and it supports total solutions to materialization, design, manufacture, and field application of ideas using *Design Thinking technique.
*Design Thinking: A problem-solving process that creates solutions from a consumer perspective
In addition, FINEX 3 plant, which has potential risk factors such as high temperature, high pressure, and gas, has been selected as a smart safety model plant and is pushing for the completion of construction by the end of this year. Applied technologies include a gas leakage monitoring system using gas detectors and thermal imaging cameras, connecting various wearable devices such as Safety Ball and Smart safety vest and monitoring systems in the cab, workers’ access control and flow in dangerous areas, and digital safety work procedures. POSCO plans to build a safe working environment by spreading it to all the steel mill plants through supplementation of technology once the FINEX 3 model plant is established.
POSCO plans to introduce Smart Safety with the belief that all of our safe work sites will soon lead to POSCO people’s happiness. Smart Safety technology that to be applied in the future is gradually spreading to domestic industries and local governments.
POSCO continues its efforts to lead to “a workplace where safety is a top priority becomes the driving force of a happy life.”