Innovation is critical in today’s business market. New technology, new products, and new systems must constantly be developed, improved, and maintained in order to remain competitive. At POSCO, to ensure that its facilities, systems, and production lines were running smoothly, and at full capacity, they developed Quick Six Sigma Plus (QSS+). QSS+ worked to streamline its factories helping it to provide some of the most advanced steel products in the industry.
What is QSS+?
QSS is a tailored and upgraded version of Six Sigma, a popular technique used in many businesses to reduce defects and variabilities in manufacturing and business processes. Moving beyond creating a clean workplace and restoring facility performance, POSCO further upgraded QSS to QSS+ in August 2014 to include My M&S (Machine & Safety) activities, designed specifically to build a more efficient and safer working environment.
Through QSS+, POSCO has been able to drastically improve its facilities by establishing standard manufacturing processes. They worked to make raw material and inventory management more efficient and reallocated working spaces for increased productivity. Since 2006, POSCO’s unique innovation program has helped its employees to complete over 8,000 assignments designed to improve the production line. Such efforts resulted in reducing the concentration of fine dust, equipment failures, and improving the operation rate up to 95%.
QSS+ Success Story
POSCO applied QSS not only to its steel mills but also to its family companies and overseas subsidiaries. In China, the first QSS leadership training and master workshop were launched in 2011, and after one year, Qingdao Pohang Stainless Steel became the first overseas subsidiaries to be QSS-certified. In 2015, POSCO China chose four representative branches to lead My M&S activities.
In 2013, POSCO Vietnam successfully completed facility restoration activities named ‘My Machine’ at 11 different facilities as well as 19 other QSS assignments. In 2016, It became the first facility in Southeast Asia to begin using QSS+, tailoring it for their multiple branches.
In Pohang, Korea, four plants drastically lowered the concentration of fine dust in the steelworks from 80mg/m2 in 2007 to 50.3mg/m2 in 2013. Also, in 2016, they launched ‘Smart M&S’ – a program that works to integrate ‘My M&S’ safety improvements with its smart factory, helping it to become safer and more efficient at the same time.
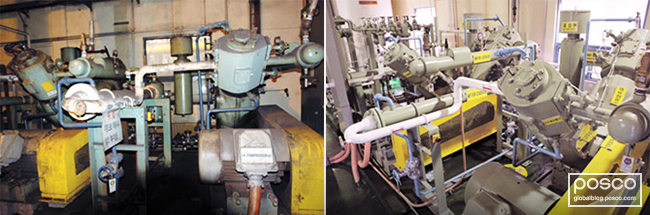
Facilities before (left) and after (right) carrying out a systematic inspection through My M&S Activities.
Initiating programs like QSS are not easy. Because factories are running 24 hours a day, it can be difficult for workers and management to see how individual steps can improve an entire system. According to Kim Dukbae, POSCO’s first QSS Master, “QSS+ was able to become a strong pillar of POSCO’s operations because the leadership team and employees took the initiative to constantly improve and transform our operations…”
QSS+ is now established as a goal-oriented and innovative program that focuses on the three elements of quality, stability, and safety. Thanks to QSS+ and its advancement over the past decade from Six Sigma and QSS, POSCO has been able to establish safe and healthy manufacturing sites. POSCO will continue to apply QSS+ in every level of its organization in order to ensure its position as an industry leading steelmaker.
Don’t miss any of the exciting stories from The Steel Wire – subscribe via email today.