Providing satisfaction to customers with high-quality products and eco-friendly steel solutions and striving to reduce CO₂ emissions! Experts introduce POSCO’s new steel wire rod products.
Young-tae Oh, Section Leader
(Hot rolled steel & wire rod marketing office)
Background of non-heat treatable steel wire rod for automobile fastening CHQ
Wire rods are steel materials used in various industries, such as automobiles and construction. Among them, wire rods for CHQ are key steel parts for automobiles that are mostly used for fasteners that are directly related to human safety and thus automobile manufacturers demand strict quality standards for CHQ wire rods. It requires many complex processing stages to convert wire rods into automobile parts that satisfy customers. Before fabricating parts, cold drawing and spherodized annealing (SA) heat treatment are performed to ensure accurate sizing and enhance formability. Afterward, the automobile fastening part is completed by controlling the shape with cold forging and ensuring strength of the part with quenching and tempering (Q/T) heat treatment.
With the rapidly increasing need for low-carbon emissions as society places more importance on eco-friendliness and eco-friendly vehicles, the industry’s interest in eliminating the heat treatment process has grown quickly. In particular, domestic automobile part manufacturers pay attention to non-heat treatable steels since they need to expand into the global market to overcome stagnation in the domestic automobile market. Therefore, POSCO has focused its know-how and capabilities on eco-friendly wire rods with reduced carbon emissions to lead the future market.
Collaboration with a domestic fastener company resulting in application to a Japanese auto part for the first time
POSCO’s non-heat treatable steel series POSNH, which is POSCO’s leading non-heat treatable steel, is a group of steels with improved formability by optimizing alloy contents and refined grains by adding microalloying elements such as niobium (Nb) and vanadium (V) to increase impact toughness. POSCO’s POSNH series includes PONH4, POSNH6, and POSNH9S grades.
Among them, 0.9 GPa level (normally 9T level) POSNH9S is a product developed in 2017 as a material for automobile steering system parts. POSCO worked with Taeyang Metal Industrial Co., Ltd., Korea’s largest fastener manufacturer, to develop vehicle part products and conduct PR activities for them. As a result, the products met the stringent requirements of Japanese manufacturers and mass-produced parts for brake guide pins began to be supplied for the first time in the first half of 2021.
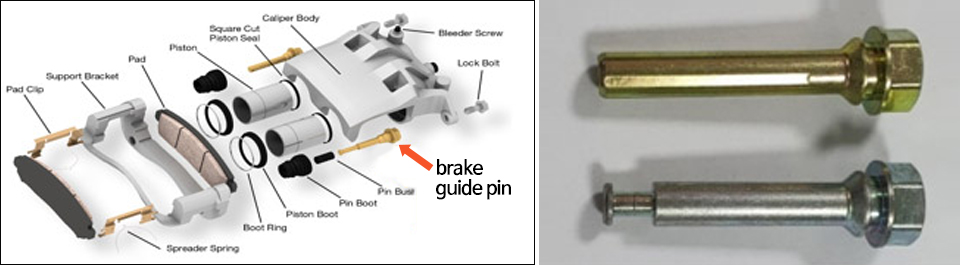
▲Car steering parts brake guide pin.
Application to steering parts for GM vehicles in North America
POSCO worked with Korean auto company CTR to propose the POSNH9S steel part for the tie rod of steering to be used in new pickup trucks for GM in North America in 2022. The company succeeded in mass production for GM finished automobiles in North America in 2022 because it gained a competitive edge over global part manufacturers by developing and providing a solution that applies non-heat treatable steel to auto part company needs such as optimal wire drawing and film conditions, and forging die life improvement technology.
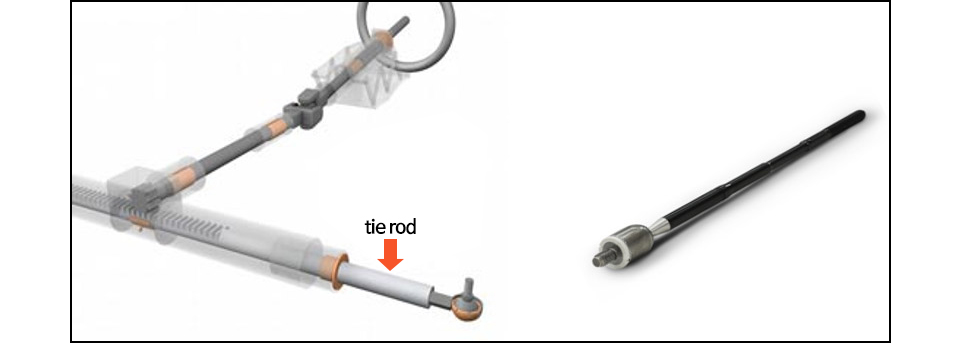
▲Car steering parts tie Rod.
POSCO solves Korean fastener manufacturer’s chronic problems with solutions using non-heat treatable steel
The demand for shoulder bolts for fastening electric vehicle batteries and battery packs has recently increased due to the rapid growth of eco-friendly vehicles such as global electric vehicles. Existing carbon steel (SWRCH45K) requires Q/T heat treatment to secure strength after final bolt processing, but bending after heat treatment requires additional correction work. To solve the problem, POSCO worked with its fastener partner to apply steels without Q/T heat treatment. POSCO achieved the required strength by increasing wire drawing, and its fastener partner optimized the forging process to mass produce PSNH9S, a non-heat treatable steel that can skip correction work. As a result, the fastener manufacturer reduced costs and improved productivity by omitting Q/T heat treatment and correction work. This enabled it to stably supply low-carbon, eco-friendly products to the market.

▲Supply chain processing for the application of heat-treated steel.
POSCO’s POSNH9S confirmed to be applied to a Korean electric vehicle for the first time in 2024
Korean automakers have also shown interest in POSCO’s carbon emission-reducing non-heat treatable steel after the 2045 Carbon Neutrality Roadmap was announced. POSCO proved the excellent quality of its products by conducting material and product durability and performance evaluations in collaboration with Korean automobile and its part manufacturers in the second half of 2022. As a result, the first application was confirmed for the tie rod, a steering part of a new electric vehicle scheduled to be released in 2024. It is expected to be a bridgehead for the company to expand its presence to vehicles produced domestically and overseas.