Meet INNOVILT LAB, the place where the best INNOVILT products are created. It is a kind of a base camp where POSCO is undertaking R&D for the next generation INNOVILT products.
The INNOVILT product to be introduced today is “UL700 Steel-Aluminum Hybrid Jack Support”. POSCO Newsroom presents to you the story of a POSCO researcher who developed the product together with POSCO’s client, Daehan Scaffolding.
l Temporary Materials? Safety Materials!
I am Tae-Hyu Ha, a senior researcher at POSCO Steel Structure Research Group. I am working on developing construction materials using POSCO steel, and today I am going to tell you the development story of “temporary materials“.
Let’s picture the construction of a building. Laying down the base work, building a framework, installing floors and ceilings, applying interior and exterior materials, and decorating the interior — these might probably be the construction processes that come to mind. However, there is one crucial process missing here. It is none other than “temporary work”.
Temporary work is the phase where temporary and basic structures necessary for construction are installed. It includes bringing in electricity for the construction tools, installing water facilities for drinking and sanitizing, and establishing safety facilities to prevent accidents. And “temporary materials” are essential in this temporary work. Temporary materials include walk plates and passages installed to enable work at high areas, supports that temporarily hold the building framework, and a double-deck that allows vehicles and pedestrians to walk above the construction section. Put differently, proceeding with construction is impossible without temporary materials.
Temporary materials are especially important in that they directly affect the quality of construction and the safety of workers on site. However, in most cases, they aren’t paid much attention because they are demolished once the construction is complete. Since temporary materials are perceived to be materials that are used for a short time anyway, many try to shorten the construction period by setting them up quickly and reduce costs by utilizing cheap materials imported from overseas.
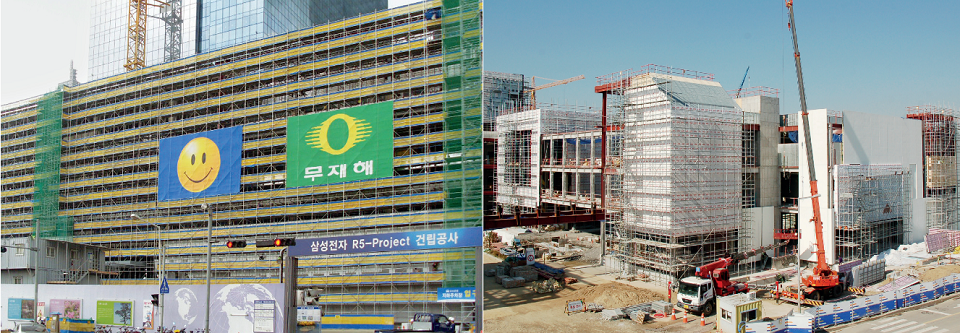
▲ High-strength system scaffolding installed on sites
In this situation, POSCO set to pioneer the temporary material market using premium steel materials with its clients from 2009 as a measure to secure the safety of construction sites. The goal was to bring about a change in perception that temporary materials are not just temporary but are safety-related materials that are directly connected to the safety of workers. As a result, POSCO developed the premium steel tube “UL700 (Ultra Light 700)” for “scaffolding”. POSCO’s high-strength steel PosH690 was applied as the material for UL700.
What is scaffolding? Well, when passing a remodeling site or a construction site, you might have seen a structure where narrow steel pipes are woven together vertically and horizontally as if they were wrapping the building. This is called scaffolding, and it is a kind of a walk plate that enables workers to safely climb up and down in the construction of high-rise buildings. Scaffolding made with UL700 adopts POSCO premium steel and has a tensile strength of 700 MPa, replacing conventional scaffolding that mainly uses general steel pipe of 400 MPa tensile strength.
In the beginning, expanding high-strength premium products in the price-oriented steel pipe market was not easy. However, after receiving positive feedback from construction sites and being recognized for its economic feasibility and safety, demands for the products began to expand gradually.
l Making the Temporary Column “Jack Support” as Premium
As recognition for UL700 with its safety and high strength performance grew, product inquiries rushed in not only about scaffolding but about various other temporary materials. Then one day in February 2016, Min-Young Jeong, CEO of Daehan Scaffolding, visited the POSCO R&D Center in Songdo and shared his story with us.
“We are a company that manufactures and supplies a product called Jack Support. Jack Support is used to distribute the load of the upper part of a building. When concrete is poured on the floor, its strength increases as the concrete hardens, but it usually takes more than a week for the concrete strength to become sufficient. So, to proceed with construction on the upper floor, temporary support must be installed under the floor plate while the concrete is hardening and the temporary support used here is Jack Support.”
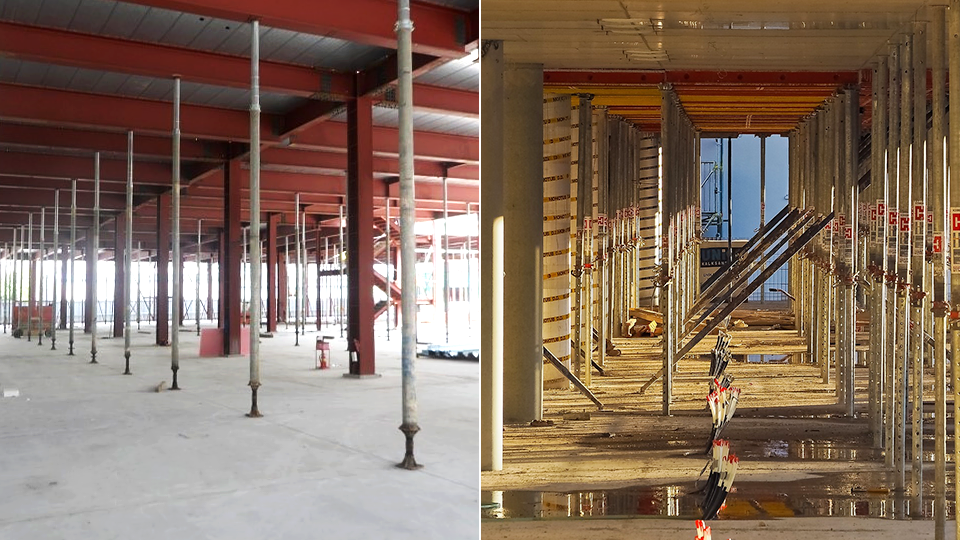
▲ Jack Support applied on construction sites
He went on, “However, we have a problem. For places with high ceilings, such as the lobby and public space on the first floor, a Jack Support of at least 5m is required, but the problem is that as the product length increases, the weight increases as well. Manufacturing and supplying aren’t a problem but installing a product weighing over 100kg is a definite issue. Imagine that workers have to lift, move, and install a material that weighs over 100kg. So, that’s why we need to develop a Jack Support that is light yet long enough. I heard that there is a steel pipe for scaffolding called UL700, and I wondered what if we apply such high-strength steel to Jack Support as well.”
Jeong’s suggestion was plausible, but I was not too sure. I could not help but think, “Oh, length issues. Again”. It was because I knew from my experience that when high-strength steel is applied to a long material, the performance does not come out properly due to “buckling”. Buckling is a phenomenon where a material, which has a long length compared to its cross-section, suddenly bends when the load is applied above the limit it can hold up. In the case of short types, high-strength steel can withstand much heavier loads without bending, but with the length increasing, even high-strength steel bends under similar loads as ordinary steels due to this buckling effect.
I said, “CEO Jeong, Since buckling occurs in long materials, it is highly likely that the results might be indifferent even in the case of high-strength steel. So, let’s design products by length using high-strength steel first, and then conduct performance tests with the prototypes. Detailed directions can be discussed later.”
First, as CEO Jeong suggested, I set on designing a standard-type Jack Support (with a height of 3 to 4m) and a high ceiling-type Jack Support (6 to 10m). The idea was to make four prototypes, two for each type — one with normal steel SS40 and the other with high-strength steel PosH690 — and check the maximum load each product can support. The design details were sent to Daehan Scaffolding and they were produced accordingly. Two months later, we met again at the Songdo R&D Center to evaluate the performance. After inspecting the completed prototype, we carefully started the testing. The results turned out as expected. The standard-type Jack Support adopting high-strength steel exhibited similar performance to conventional products while reducing the overall weight. However, in the case of the high ceiling-type Jack Support, both the high-strength prototype and the normal prototype didn’t meet the required performance, which is a maximum load of 30 tons.
Things didn’t work out as CEO Jeong had expected, and it was a little disappointing for us as well. We couldn’t attain the desired results, but we couldn’t stop there. We carefully made a new proposal.
“Developing a high ceiling-type Jack Support is difficult right now. How about applying high-strength steel to the standard-type Jack Support instead? As you could see in the testing, if high-strength steel is applied on the standard-type Jack Support, the product weight can be drastically reduced. It could enhance the price competitiveness of the product as well.” CEO Jeong considered our offer for a while and replied, “The product is widely applied, and the market is much larger, so it would be worth a shot. Let’s do it!” After that, we set on several detailed design and performance tests, and we finally launched a high-strength Jack Support with a maximum length of 3.8m.
It wasn’t a product of the initial plan, but the response from the market was hot! The secret was its lightweight, which is about half the weight of conventional products. It was an opportunity to capture the need for lightweight Jack Supports in the market. In construction sites, time and labor force are important, so the demand for high-strength lightweight products gradually increased, and the client company producing and supplying these products became busier than ever.
l Steel & Aluminum Together! The Advent of a Hybrid Jack Support
In November 2018, almost three years later, Daehan Scaffolding CEO Min-Young Jeong contacted us for another visit to the research center. Since the commercialization of the high-strength Jack Support, we hadn’t received any direct communication, so CEO Jeong’s contact was quite a surprise. Was there any problem? The story of CEO Jeong was as follows.
“Currently, our product is the lightest among domestic steel Jack Support products. The market has also expanded. But recently, more and more companies are making Jack Supports with aluminum. Aluminum is supposed to be expensive, but the price of these products aren’t very different from our products as well. So, I would like to take a chance to upgrade our products once again.”
There were two things that Daehan Scaffolding desired. The first was expanding the maximum length of use from 3.8m to 5m. CEO Jeong explained that the length of the product had to be increased than the present to respond to various demands on the field. The second was extending the range of length adjustment. The adjustment range of current products is only 30cm, and so to meet the length requirements of each construction site, the products have to be manufactured accordingly, resulting in over 10 different types of products, which is too many. CEO Jeong wanted to extend the adjustment range to 70cm with a single product that could be applied to more sites.
Listening to him, I realized that it was similar to what we had worked on three years ago. As I was going to say, “Let’s try a new method since it’s difficult to do that with high-strength steel.” CEO Jeong proposed an idea, “We designed a product where the length can be adjusted by inserting an aluminum inner tube into a UL700 steel pipe.”
Combining aluminum and steel? At first, it sounded like a non-realistic plan. I thought, ‘This product can be made with steel alone. Why should we apply aluminum here?’ But my thoughts soon changed as I saw the prototype sample. Since the aluminum inner tube allows precise machinability, it became easy to secure the straightness of the product, and the strength of the product was also steady thanks to the application of high-strength steel. Making the outer tube, which must withstand the load, with high-strength steel, while making the inner tube for length adjustment with aluminum to reduce the overall weight — it seemed like a workable idea.
We decided to come up with an optimal design based on the client’s prototype. First, we worked on finding the coefficient for the complex aluminum section design. Next, we calculated the buckling load of the steel pipe by length and improved the thickness of the steel pipe and the shape of the aluminum section accordingly.
Four types of test specimens were produced by different lengths, and load testing was conducted for each. The commercial product lineup was also complete taking into account the test results and the most required height at construction sites. Considering the buckling strength and field workability of the inner tube, the length of the aluminum inner tube was set to 1m, and it was produced in four different sizes. After a year of research and testing, we finally launched a high-strength hybrid Jack Support with aluminum inner tube in July 2019. It was such an achievement in 4 years since the first meeting with Daehan Scaffolding in 2016.
l Safety for Workers, Economics for Contractors
The collaboration of steel and aluminum — the two different competing materials — was embodied into this Hybrid Jack Support. And within a year of its introduction to the market, it has been applied to more than 30 apartment construction sites of leading domestic construction companies, such as Hyundai E&C, Daewoo E&C, and POSCO E&C.
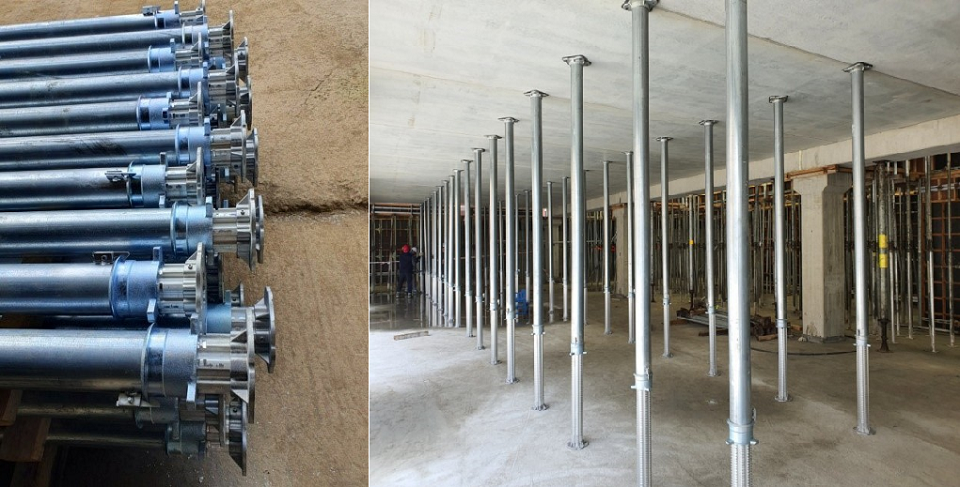
▲ The UL700-Al Hybrid Jack Support applied on site
CEO Jeong said, “The product is really good because it’s light — this is what I hear a lot when supplying the products.” We started with the application of high-strength steel to temporary construction materials, which led to the development of ultra-lightweight, high-strength Jack Supports, and, finally, here we were with Hybrid Jack Supports.
Compared to the conventional 5-inch product, the Hybrid Jack Support has the same strength but is 50% lighter. It also weighs about 80% of an aluminum product. Since UL700 is high strength steel, it is possible to reduce the outer cross-sectional area to one-third of that of aluminum, which results in remarkable weight reduction. Supposing that the conventional Jack Support is 60kg, an aluminum product is 35kg and the Hybrid product is merely 29kg. Other than the fact that it can be handled more safely by the workers, what meanings do this ‘lightweight’ feature have on sites?
The most crucial fact is that it can be installed quickly due to its weight reduction. 29kg is a weight that a single worker can easily handle. Also, unlike conventional products, the length can be adjusted up to 70cm without bolts, so it allows quick and convenient work.See how a worker installs a Hybrid Jack Support on site in just 35 seconds!
The simple and quick installation enables a reduction in labor costs and shortens the construction period. In fact, there was a case where labor costs were reduced by more than 30% as the time required to install and disassemble products was shortened. Also, since a more number of products can be loaded on the trucks to carry them, transportation costs are reduced by about 30%.
However, there may be doubts like, “Wouldn’t there be a problem with durability if it becomes so light?” There might be concerns about the inner tube made of aluminum being damaged on sites. But the product we aimed to manufacture was a ‘light yet strong temporary material’ — not just a light one. Unlike conventional products, the Hybrid Jack Support is designed to be separated by parts, so there is less risk of damage, and even if it is damaged, the damaged part can easily be replaced, so the maintenance cost is also low. The exterior of the Hybrid Jack Support is made of POSCO UL700, which makes it much more durable.
Four years have passed since developing Jack Supports using high-strength steel and improving them to meet the needs of the market. The market looks stagnant, but its trend is changing fast. That’s why we can’t just sit still in the lab and make an experiment to develop products.
In that sense, the Hybrid Jack Support is the result of POSCO and its client going back and forth between the lab and the field, constantly thinking about ideas to overcome the weaknesses of the product. In the second quarter of this year, it was listed as one of the INNOVILT certified products as well.
The temporary materials market is a place with unclear quality standards and a high temptation of low-cost goods. However, it is our mission to change this perception and eliminate the blind spots for the safety of workers with our products and technologies. At the same time, we should create solutions that can bring substantial benefits to the constructors as well. This is the reason why, even today, INNOVILT Lab is busy developing new solutions.