The 4th Industrial Revolution is transforming the manufacturing industry. Artificial intelligence (AI) and robotics are being applied to production and distribution, and technologies are being merged to form new innovations. In the realm of manufacturing, artificial intelligence will take on various roles where human judgment and control are required. The existing boundaries between industries and businesses will collapse and some businesses and industries will disappear altogether. Companies that fail to accept these changes and adapt accordingly will lose their competitiveness.
What’s more, manufacturing is no longer a rigid industry that produces uniform, one-sided goods. There is constant communication between customers and businesses for hyper-customization. Not only that, machines and products communicate within a smart factory, and factories exchange data with other factories. Manufacturing is no longer limited to production plants. Moreover, the data generated in the manufacturing process is combined with customer information, and a new service can be created. This combination of manufacturing and services is resulting in creation of added value. In the midst of such drastic change, how can companies stay competitive?
Staying Competitive Through Connection and Convergence
Global manufacturing companies are at the forefront of the 4th Industrial Revolution, as evident in their smart factories. A smart factory collects data generated from the production process using ICT technology, and the system controls all processes from material input to the final product. This has led to flexible production systems with the ability to make various products in one factory or to expand the range of products on the basis of connectivity. Typically, when a company builds a smart factory, it can improve productivity by 20 to 30 percent. A 20 percent improvement in efficiency in the manufacturing sector is a significant, outright increase in global competitiveness.
SEE ALSO: How Smart Factories are Changing the Manufacturing Industry
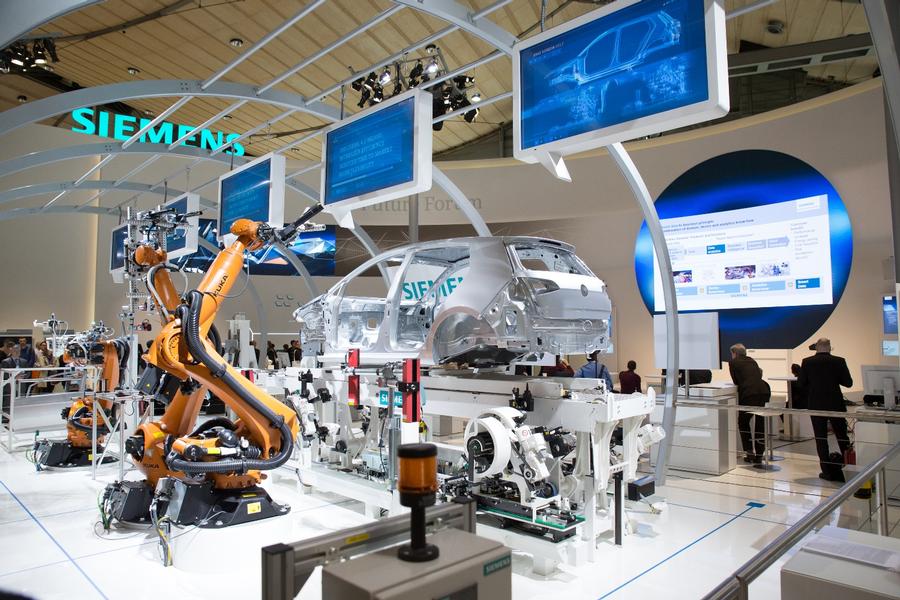
Siemens Electronics Manufacturing Plant incorporates robotics, AI and IoT to its production processes. (Source: Zawya)
If the productivity of a plant can be improved through smartization, it is important to also think about connectivity with the ecosystem that exists outside of the plant. Once a smart factory is built, all the data from customer orders to production and delivery are collected in a system via sensors. The customer, product and production data create meaningful connections with each other and provide extensive insight. Examples of added value creation through meaningful connections include hyper-customized goods, data-driven after-sales services to customers and collaboration among companies connected within the smart factory’s external ecosystem. Such advancements will lead greater product quality, production stability as well as shortened delivery times between value chain suppliers.
The Adidas Speed Factory and GE Brilliant Factory are examples of successful smart factories. Adidas customers choose the materials, colors and design of their sneakers, and have them manufactured and shipped within 24 hours in an automated factory.
GE has built a system that can produce all of their widely-diverse products in one factory. When the factory receives customer orders, it operates in a flexible production system which starts with the necessary raw materials, inputted by the automated scheduling system that controls the entire production process, including the final distribution system.
The Future of Manufacturing
Overall, the adoption of innovative changes in the manufacturing sector is likely to progress from lighter industries to the heavy industries, from B2C to B2B sectors. Small plants, quick manufacturing and B2C companies can more readily adapt to rapid technological and market changes. On the other hand, heavy industries like steel and B2B companies with continuous and heavy manufacturing, large production volume and numerous linked companies are likely to be slower to adapt to changes.
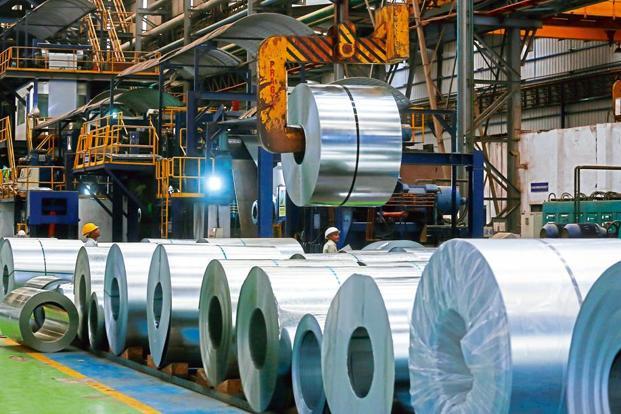
It is much more difficult for traditional, heavy industries to adapt to changes. (Source: Live Mint)
For example, adapting to the changes of the 4th Industrial Revolution in the steel industry may be slow, but it is inevitable. What’s more, the long-term adaptation process is more likely to be systematic and deliberate.
As a leading company in the global steel industry, POSCO is pursuing a long-term, systematic “Grand Design” to reinvent its systems to align with the changes of the 4th Industrial Revolution.
First, POSCO built a pilot smart factory in their steel mill, Gwangyang Steelworks, in 2015 that is currently in operation. The company used IoT to collect big data on site, analyze it in real time and build a smart factory that enables optimal control through AI and self-learning. As a result, the Gwangyang Steelworks is reaping the benefits of a smart factory not only in cost reduction but also in improved steel quality, minimized malfunctions and a safe and stable production environment. This year, POSCO plans to expand and apply smart factories to all of its production processes.
Smart factory application throughout the entire steel mill will improve overall efficiency through a flexible production system. In addition, the factory will be able to respond directly to various customers in real time based on platform construction with customers within the connected ecosystem. The customized characteristics and design of the steel grade for each customer can be applied to production in real time.
SEE ALSO: How Factories Produce Steel – the Smart Way
Ultimately, a smart ecosystem that links manufacturing, processing and distribution with customer input will lead to a new, innovative ecosystem within the steel industry. In Europe, some companies are experimenting with material libraries and steel distribution platforms. The material library displays a variety of materials for customers to see, touch and test the workability and performance of the materials, and get information about the characteristics, design and delivery times through the order platform. Customers can designate the shipment date on the spot. This will be one of the new promising business models that steel and other material companies will strive towards in the coming future.
POSCO’s Grand Design includes a step-by-step approach to smart factories to expand the use of IoT, AI and Big Data in its production systems. To this end, POSCO ICT has developed PosFrame, a standard software platform that collects basic data of production processes and collectively manages, controls and analyzes the information.
When the software becomes standardized and reliable enough to extend to other sectors, it will be applied to other business areas such as energy and construction, as well as to POSCO’s affiliates.
Manufacturers will have to take into account the heavy production environment, the slow industrial change cycle and the complexity of related industries and affiliates to implement the most effective, long-term, systematic upgrades to its production systems. This will result in a brand-new production and business model for manufacturing companies that will align with the new environment of the 4th Industrial Revolution.
Kim Sang-Yun is a Principal Researcher at POSCO Research Institute (POSRI) with a Ph.D. in Technology Management. He has been researching topics related to the 4th Industrial Revolution, manufacturing innovation and technology management for over 7 years at POSRI. He received his Ph.D. in Technology Management from Yonsei University in 2011 and is currently an Advisory Member of the National Science and Technology Council (NSTC). |
Cover photo courtesy of Sputnik International.
- 4th industrial revolution
- Adidas
- Adidas Factory
- Adidas Speed Factory
- AI
- artificial intelligence
- B2B company
- Big Data
- Brilliant Factory
- competitive
- competitive company
- competitive company of the year
- customer
- Electronics Manufacturing Plant
- environment
- GE Brilliant Factory
- GE Factory
- global
- Grand Design
- Gwangyang Steel Mill
- Gwangyang Steelworks
- heavy industries
- heavy manufacturing
- heavy production
- heavy production environment
- how is steel made
- how to produce steel
- hyper customization
- Industrial Revolution
- iot
- Kim Sang-Yun
- manufacturer
- manufacturing
- manufacturing company
- manufacturing industry
- Manufacturing Plant
- material
- National Science and Technology Council
- nstc
- posco Gwangyang
- POSCO Gwangyang Steelworks
- POSCO ICT
- posco mill
- POSCO Research Institute
- posco steel
- posco steel mill
- posco Steelworks
- PosFrame
- POSRI
- produce steel
- production
- robotics
- Siemens Electronics
- Siemens Electronics Manufacturing Plant
- smart factories
- Smart Factory
- Speed Factory
- steel mill
- Technology Management