The steel industry understands and considers the urgency of the issues surrounding emissions to air and their effect on air quality, human health, and the environment.
For several years, the steel industry has taken measures to eliminate these issues, and the effort is ongoing. What are some of the key issues surrounding the industry’s air quality management? POSCO Newsroom presents worldsteel, “Air Quality Management.”
The steel industry recognises the importance of the issues surrounding emissions to air and their impact on ambient air quality, human health and the environment.
For decades, the steel industry has taken measures to address these issues, thereby significantly and demonstrably reducing emissions per tonne of steel.
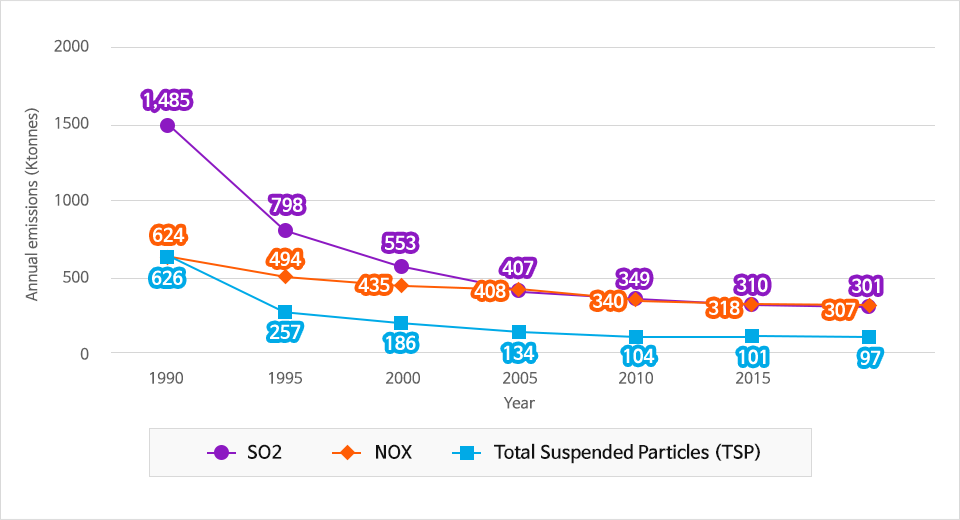
▲ worldsteel.org – Source: UNECE Convention on long-range transboundary air pollution
Steel, whether produced via the integrated, direct reduced iron or electric arc furnace route, requires the transport, storage, handling, heating and transformation of raw materials.
All these processes have the potential to generate emissions to air *, primarily in the form of dust (or particulate matter (PM), sulphur dioxide (SO2), and nitrous oxides (NOx). Other emissions generated in small quantities include dioxins and heavy metals, typically attached to dust particles.
Today, all steel plants are subject to environmental regulation, which set requirements to restrict emissions to air. This regulatory framework is translated into an environmental permit (or licence to operate), which establishes plant-specific Emission Limit Values (ELVs) covering the primary emissions to air, dust, SO2, and NOx, and in most cases other
emissions.
The environmental permit also sets monitoring requirements and it is common for steel plants to have additional requirements within the permit, such as maximum production capacity, emission ceilings for specific emissions, taxes or fees on emissions or specific reduction targets.
l Emissions from Stacks versus Diffuse and Fugitive Sources
Stack emissions are released at height from identifiable sources (point sources) and are dispersed in the atmosphere. Diffuse and fugitive emissions (non-point sources), contrary to stack emissions, originate from an area, such as a stockpile or a road.
Stack emissions are managed using a variety of controls, such as beneficiation (i.e. removing potential contaminants before further processing), yield/process optimisation (‘more with less’), combustion control, abatement technologies (i.e. bag filters, electrostatic precipitators (ESPs), wet scrubbing systems, activated carbon adsorbers, cyclones, mist eliminators, etc.), source monitoring, incident investigation, plant inspections, source modelling and targeted plant maintenance regimes.
Stack emissions from the steel industry are managed to be well below prescribed ELVs. Exceedances are infrequent and occur in most cases during process disturbances. In these cases, authorities are informed and investigations carried out to identify the root cause, prevent recurrence and drive continuous improvement.
Emissions from iron and steelmaking operations, including cast house floor emissions from blast furnaces, are controlled via secondary dedusting systems (i.e. bag filters, wet scrubbers, ESPs, etc.) with a collection point inside the building. Occasionally, for safety reasons, the flaring of process gases is required. In this case the gases will have been filtered beforehand.
Diffuse emissions are mainly associated with material handling, stockpiling and transport activities. A variety of controls are used to manage potential emissions from these activities, such as minimising volumes of material stored, stockpile design, watering of stockpiles and roads, application of surface sealants, use of enclosures for bulk material storage, paving and sweeping of roads, dedusting of transport belts or use of closed belts, windbreaks/vegetation and video surveillance.
In addition to these measures, several tools are used to proactively manage emissions, such as weather alert systems, ambient monitoring, plant inspections/audits and risk/incident management systems.
Fugitive emissions, such as emissions generated from the roof of some buildings or emissions escaping from valves and evaporation of solvents are typically controlled and managed through maintenance and monitoring.
Diffuse and fugitive emissions are commonly regulated through the application of regional ambient air quality standards, which are based on an assessment of modelled or potential impact on the ambient air quality at selected ambient monitoring locations in the neighbouring area.
l Regulatory Framework
An environmental permit is a requirement for the operation of a steel plant. The permit is based on an assessment of the environmental impacts of
activities and most permits set ELVs in addition to defining monitoring and reporting requirements.
Environmental permits are typically reviewed periodically, or in case of production increase, construction of new facilities, new/revised environmental standards, or when new substances are identified.
- Environmental permits and ELVs must be based on sound science with respect to the potential risk to human health and the environment, and they need to be achievable.
- Environmental permits should never prescribe the use of a specific technology but should allow requirements to be met with a technology/practice of choice. To guarantee the smooth operation of the plant and the optimal protection of the environment, the permitting process must ensure legal and planning certainty.
l Holistic Environmental Assessment
Advanced abatement technologies require energy and other operational supplies to provide effective emission control. For example, wet dedusting technology requires significant amounts of water and electricity as well as chemical additives. To ensure an optimal environmental outcome, it is necessary to consider the impact of the prospective air emission abatement control technology on other environmental aspects (i.e. water pollution, waste generation/treatment requirements, energy requirements and greenhouse gas emissions), commonly known as the cross-media effects.
- When considering a suitable abatement technology for a specific emission source or production process, it is essential to take a holistic approach to the potential environmental impacts and consider the overall sustainability of the technology.
l Application of Emission Reduction Technologies
Every steel plant is unique, for example, in relation to geographic location, the proximity of sensitive receivers, the scale of operation and production processes. Therefore, a robust environmental risk assessment, including analysis of potential cross-media effects, is essential to ensure that identified emission reduction technologies are fit for purpose and sustainable for application at a specific steel plant.
Technical considerations should contemplate aspects such as the applicability to new and/or existing plants, specific operating conditions and types of raw materials and fuels.
- Since every steel plant is unique, it is essential to assess and ensure that identified emission reduction technologies are fit for purpose and sustainable for each application.
Stack emissions from power generation, industrial processes and the steel industry contribute to general background levels of air pollutants and form part of a larger set of physical agents found in the atmosphere. Emissions from natural sources such as forest fires, soil, pollen and sea spray also make up a large part of the background levels.
- Reducing emission generation from point sources improves regional air quality.
Diffuse and fugitive emissions, particularly dust emissions, are typically emitted close to ground level, and as such predominantly contribute to local air quality and tend to raise visual amenity issues.
Other emission sources impacting on local air quality include road traffic, transport, domestic heating, construction and demolition, bulk material handling and agriculture.
- Effective control of emissions closer to ground level drive improvements in local air quality.
l Monitoring of Air Emissions
The steel industry conducts extensive air emissions monitoring to follow up on permit requirements and identify opportunities for continuous improvement.
Monitoring in a typical steel facility includes source monitoring of emissions to identify potential sources of dust, NOx, SO2, and heavy metals. This monitoring combines extractive testing and continuous or online monitoring and reporting to the authorities.
Many steel plants also maintain, or support, broader ambient monitoring networks on the perimeter of the facility or in the neighbouring community of total suspended particles (TSPs), PM10, PM2.5, NOx, SO2 and sometimes heavy metals. Other types of monitoring include deposition monitoring and biomonitoring.
In addition, most steel plants have invested in air quality modelling and other established management activities such as targeted audits/inspections, video surveillance, environmental readiness and community hotlines.
These management practices are designed to determine the steel industry’s ambient air quality contribution, assist in identifying the sources of emissions and drive improvement.
l Health and Environmental Effects
Air pollution has recognised environmental and health effects. Air quality standards are therefore established to prevent, reduce or avoid adverse impacts on human health and the environment.
Through the application of advanced abatement technologies, comprehensive management practices and a drive for continuous improvement, the industry aims to minimise emissions to air and thereby their impact.
- The steel industry engages proactively and constructively with permitting authorities and its stakeholders to respond to emerging health and environmental issues.
l Going Forward, What Are Our Key Focus Areas?
Diffuse dust (dust from material handling, stockpiling and transport activities) is the most visible particulate matter generated by the steel industry. While significant technology and management improvements have been made in the past decades, managing diffuse dust remains a challenge.
Because steel plants are often surrounded by residential areas, either for historical reasons or due to growing rapid urbanisation, the steel industry needs to further engage with local communities to discuss any concerns they may have, leading to an ongoing partnership.
Another area of critical importance is the further refining of sophisticated air quality modelling systems (dispersion modelling), which can determine the share of steel industry activities on ambient air quality and demonstrate improvement over time.
* Emissions to air have the particularity of having a local or regional reach as opposed to CO2 emissions, which have a global impact, and are therefore not covered in this report.
The full length of the worldsteel’s position paper, “Air Quality Management” can be downloaded here.