POSCO Group does its best to develop technologies that contribute to safety and carbon neutrality. We introduce POSCO Group’s excellent new technologies to create a better world! In this edition, we spotlight POSCO’s revolutionary One-Touch Converter Operation Automation Technology. With a single press of a button, this cutting-edge innovation fully automates converter operations to ensure operator safety while maintaining consistently superior operating quality.
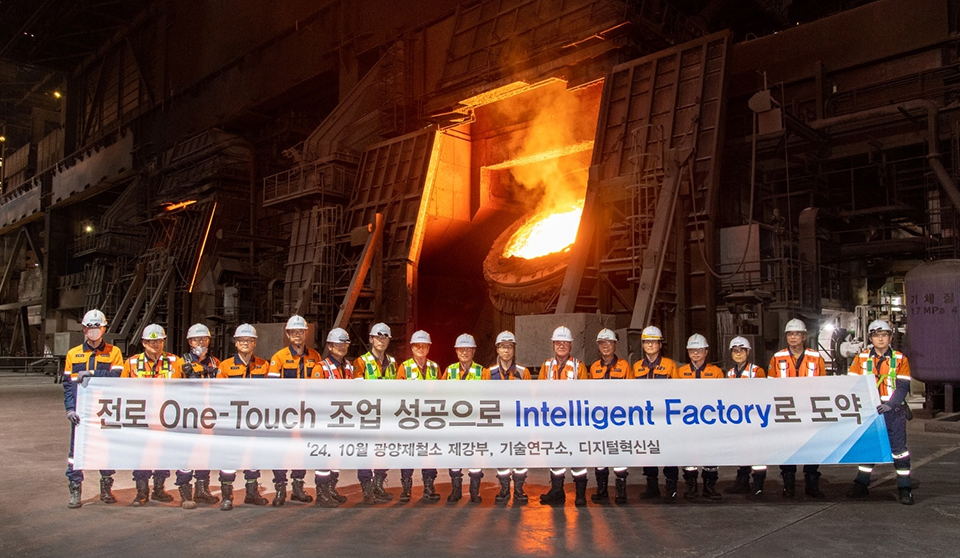
▲ After successfully completing one-touch operation of the No. 2 steelmaking furnace at Gwangyang works on October 24, Head, Gwangyang Works Dong-ryeol Lee and employees are taking a commemorative photo.
Have you heard of the term Intelligent Factory? An Intelligent Factory actively introduces core technologies of the Fourth Industrial Revolution, such as IoT, AI, and big data, to redefine efficiency and innovation. Unlike traditional “lighthouse factories,” Intelligent Factories take things further by autonomously collecting, integrating, and analyzing data in all processes for smart, data-driven decision making. In October, POSCO made a significant stride toward realizing the Intelligent Factory vision by developing One-Touch Converter Operation Automation Technology. This innovation automates the entire steelmaking process, removing impurities from molten iron from the blast furnace to produce clean steel with just a single press of a button.
POSCO’s one-touch technology applies AI to complete all converter operations without human intervention. The system also automates post-conversion processes such as tapping, slag separation, and coating, by integrating IoT-enabled vision measurement systems that collect and analyze visual data, which is then processed through AI. With this technology development, operators can monitor and manage operations remotely anytime, anywhere without manual control for safety, efficiency, and convenience.
The Need for Digital Transformation in Operating Environments
At Gwangyang works, which produces 22 million tons of crude steel annually, the converter operations in the steelmaking plant demand meticulous control by skilled operators. Each set of three converters required the involvement of 11 operators to manage the processes effectively. Molten steel reaches temperatures exceeding 1600°C and weighs up to 300 tons, which puts immense pressure on operators who must perform their tasks with the utmost care in very demanding conditions. This raised concerns about workplace safety and the need for automation technologies to ensure worker safety. Moreover, digital transformation of traditional operating methods was needed to adapt to the evolving steel industry paradigm. In 2018, POSCO’s Gwangyang works Steelmaking Division teamed up with POSCO’s Research Institute of Technology to develop intelligent, autonomous manufacturing processes that prioritize cost efficiency, quality, and safety.
Gwangyang works’ steelmaking plant had confidence in its ability to develop automation technologies due to the large number of experienced operators and vast operational data accumulated over years of production. After seven years of relentless effort, the team achieved the remarkable milestone of automating the process and reducing the 25 existing manual operations to just a single touch of a button. Let’s take a look at the three key pillars of One-Touch Converter Operation Automation Technology.
IoT-Powered Vision Measurement and Control System Automates Tapping Operations
In converter operations, where 1.5 tons of molten steel are tapped every second, the extreme heat and weight required operators to visually monitor and manually control equipment. To solve this problem, POSCO focused on automating the tapping process, one of the most complex stages in converter operations. IoT-based cameras and vision measurement devices were installed around the converter to collect years of data. This data was processed using computer vision technology, and control logic incorporated the extensive expertise of experienced operators. As a result, POSCO achieved full automation of tapping operations. Additionally, a system was established to monitor blind spots and high-risk areas to replace manual observation and prevent hazardous situations.
POSCO’s Signature AI Converter Model Hits 97% Accuracy in Temperature and Composition
Converter heat matching involves calculating the total thermal energy of molten iron, scrap, and auxiliary materials introduced into the converter. POSCO has improved this critical task by harnessing three years of accumulated operational big data and seamlessly integrating it with AI to develop a sophisticated algorithm. This innovation made it possible to produce consistent, high-quality steel, even in dynamic and variable operating environments. The developed model achieved a remarkable 97% accuracy in temperature and composition prediction, a level comparable to the expertise of top-grade operators.
Digital Twin-Enabled One-Touch Automation Integrates and Remotely Controls Processes
The digital twin system digitally replicates physical objects for real-time synchronization and interaction between virtual and physical environments. By implementing a virtual converter synchronized with real-time operations, POSCO achieved integrated management and monitoring capabilities. This advancement also enabled the creation of a system where operators can remotely control the converter process with a single touch anytime, anywhere.
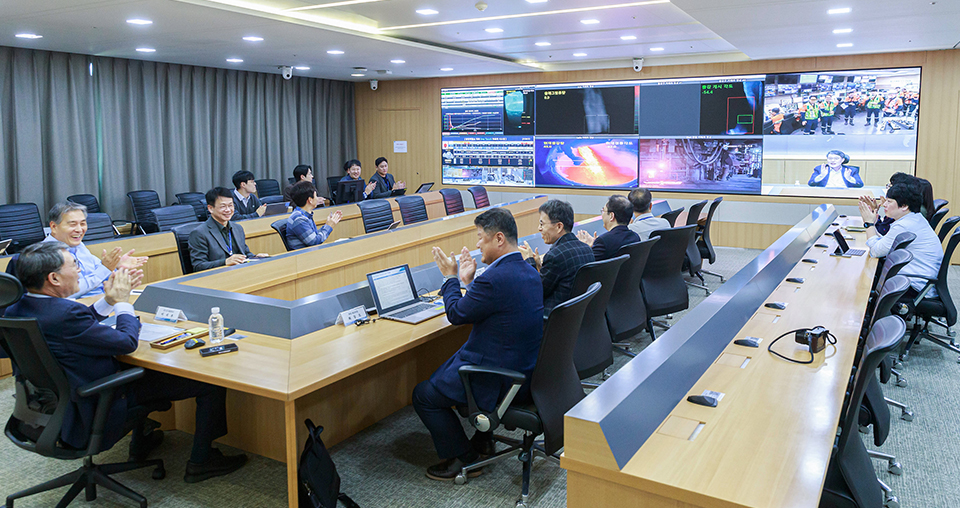
▲A demonstration of the one-touch automation system held at the POSCO Center in Seoul on October 24.
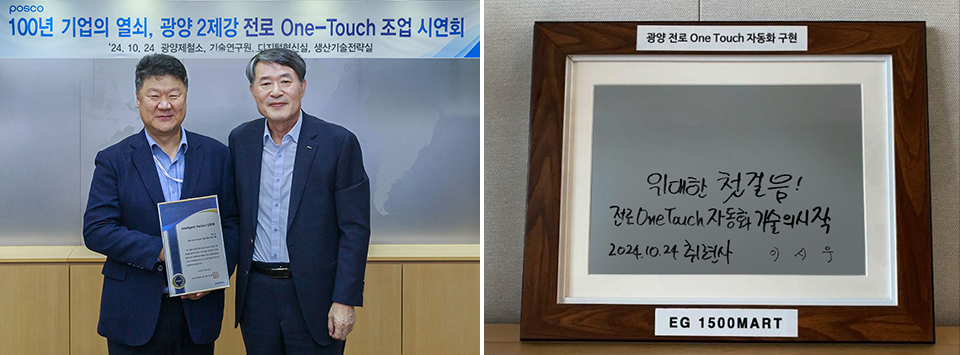
▲(left) After the system demonstration, POSCO President Si-woo Lee is taking a photo with Gwangyang works Steel Department General Technical Manager Deung-mo Choi. (right) galvanized steel sheet (EG 1500Mart steel) produced through remote Converter one-touch operation.
On October 24, a demonstration of the One-Touch Automation System was held at POSCO Center in Seoul. POSCO President Si-woo Lee successfully initiated the remote operation of Gwangyang works’ No. 2 converter to produce top-grade automotive steel.
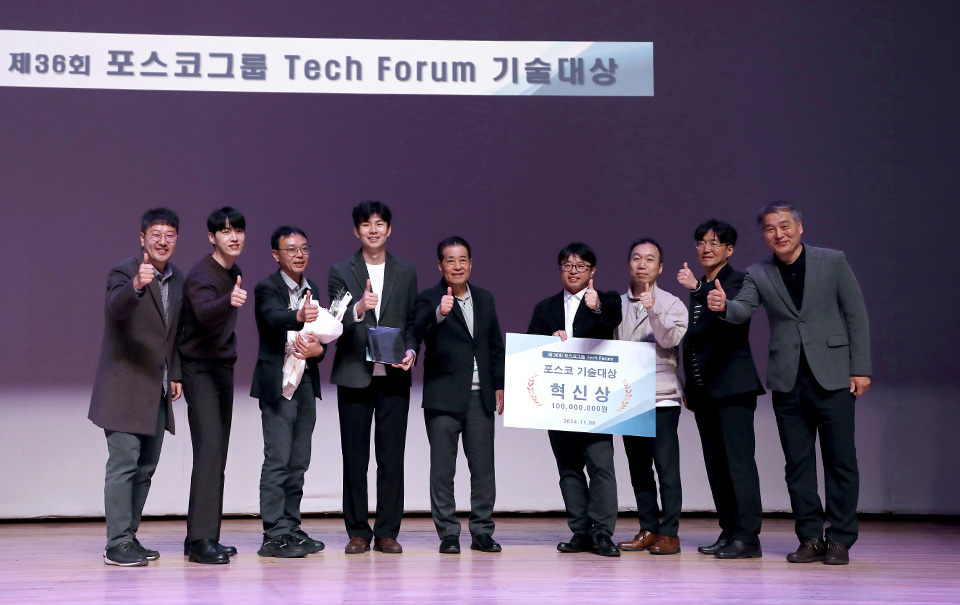
▲ The Gwangyang works Steelmaking Department team won the grand prize, the ‘Innovation Award’, at the ‘2024 POSCO Technology Awards’ (Fifth from the left, In-hwa Chang, Chairman of POSCO Group)
One-Touch Converter Operation Automation Technology is a cornerstone of POSCO’s transformation into an Intelligent Factory. It was recognized for its innovative capabilities by winning the Innovation Award at the ‘2024 POSCO Group Tech Forum’ held in POSTECH’s main auditorium on November 6.
The introduction of this technology has transformed the work environment for operators by alleviating their workload and reducing concerns about safety risks. Beyond these benefits, the accuracy of the temperature and composition of molten steel was improved from 94% to 97%, while the error rate in steelmaking decreased to maintain consistent product quality. These advancements are projected to yield annual economic benefits of approximately KRW 33.8 billion.
POSCO has also unveiled a roadmap to expand the use of One-Touch Converter Operation Automation Technology from Gwangyang works to Pohang works and its Indonesian works in the near future. Get ready to witness POSCO redefine the future by spearheading groundbreaking innovation and making a bold leap into the era of Intelligent Factories!
Part 1. Prevent safety accidents at the source! Safety braking system for forklifts
Part 2. Capturing Minute Cracks with Drones! Apartment Exterior Wall Management Solution: POS-VISION
Part 3. Dreaming of independence in battery core materials! Localized artificial graphite anode material technology
Part 4. An Urban Airport That Safeguards UAM Operations! POSCO Steel Vertiport