POSCO Group does its best to develop technologies that contribute to safety and carbon neutrality. We introduce POSCO Group’s excellent new technologies to create a better world!
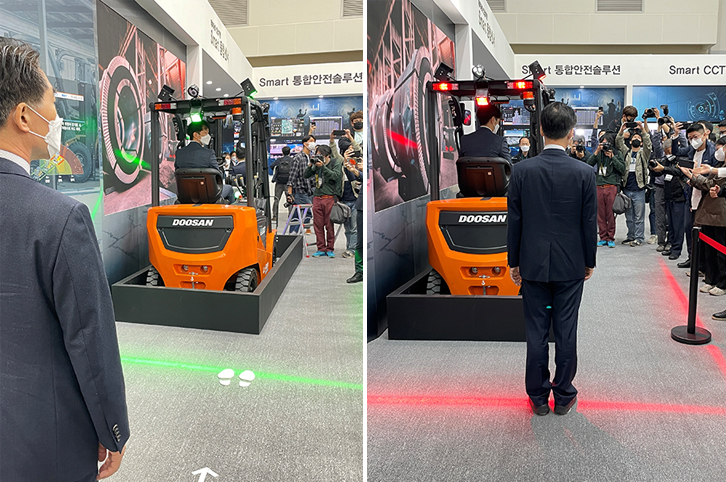
▲Seong-ho Kim, Vice Minister for Disaster and Safety Management, Ministry of the Interior and Safety, visits POSCO’s exhibition booth at K-Safety Expo 2022 and tests the safety braking system for forklifts.
POSCO’s technology was recognized for its excellence by winning the Minister of the Interior and Safety Award at K-Safety Expo 2022. POSCO Group’s safety braking system for Forklifts, which received the Minister’s Award, integrates a detection and warning system based on image recognition technology* using AI and a speed control system based on automatic stop control technology.**
The safety braking AI system for forklifts applies image recognition and automatic stop-speed control technologies to prevent disasters from collisions at the source. When a forklift equipped with the system approaches a worker, it automatically stops in stages even when the forklift operator does not apply the brake. When the collision risk distance is within 6 meters, an alarm sounds in Stage 1, deceleration begins in Stage 2 at 4 meters, and the forklift automatically stops in Stage 3 when the collision risk distance is within 2 meters. Its purpose is to automatically control the forklift’s speed to prevent an accident if the operator or worker is unaware of the situation during an unexpected emergency.
* Image recognition: The AI/deep learning technology separately recognizes people and objects from images and provides an accurate distance between the forklift and the person by converting an image taken with a wide-angle lens installed on the forklift into a coordinate system. Unlike existing technologies, it can easily recognize the risk of a collision without attaching separate tags to the forklift and worker.
** Automatic stop control: The technology automatically stops the forklift even if the driver does not apply the brake when a person approaches the forklift.
Background for development of the safety braking system for forklifts
According to the analysis of serious injury and fatality (SIF)* factors of industrial disasters released by the Ministry of Employment and Labor (MoEL), the number of deaths in accidents over the past six years is 4,432. Among these, 632 cases were accidental deaths caused by 12 original cause materials* selected by the MoEL, and 124 of them were caused by forklifts, accounting for about 20% of the total and making it the most dangerous cause in that category. The MoEL conducts unannounced site inspections, supervises high-risk business sites and intensively checks the risk of accidents caused by work on vehicles, machinery, etc. It recommended the “active introduction and use of smart safety equipment.”
*SIF: High-risk work/situations and disaster-causing factors that can result in death or fatal disruption of normal life.
**Twelve original cause materials of accident deaths: forklifts, cranes, conveyors, roofs/girders, ladders, mixers, excavators, cargo transport trucks, rope hangers, industrial robots, crushers/shredders, and injection molding machines
In general, the safety technology applied to forklifts is limited to sending a warning notification to the driver when there is a risk of collision. People may have difficulty recognizing the warnings in noisy workplaces, so there is a limit to fundamentally preventing accidents. Although the MoEL has implemented the Smart Safety Equipment Support Program to reduce forklift accidents in domestic industries according to its roadmap to reduce serious accidents, the program has technical limitations, such as only detecting workers who wear separate tags. Even if a worker is detected, there is always a risk of a secondary accident because of uneven stopping distance due to inertia, being pushed on a slope, etc.
POSCO recognized the seriousness of forklift accidents and the limitations of existing safety technology and began developing a safety braking system for forklifts to participate in solving the safety problems facing our society and to practice its corporate citizenship management philosophy.
Development process for the safety braking system for forklifts
In November 2021, a task force (TF) created by RIST and local small and medium-sized enterprises began developing the safety braking system for forklifts and completed development in May 2022. After the technology development, POSCO’s Safety Planning Office and POSCO DX collaborated for its pilot application in a steel works. POSCO DX is a POSCO Group affiliate that leads POSCO Group’s smart and automation technologies, including a smart factory platform (PosFrame), smart scheduled maintenance system (PIMS), and process automation using big data and AI technology.
Empirical testing to apply the technology to steel works sites began in April 2023. POSCO DX, a smart technology specializing affiliate in POSCO Group and Taeyang Electric, a local SME specializing in motors and prime movers, began the joint technology development. By diversifying the steel works work environment and forklift brands, four locations, two each for Pohang Pohang Works rolling process and steel wire process, were selected for empirical testing.
In May 2024, POSCO’s Safety Planning Office and POSCO DX selected a forklift each from Pohang Works 3FINEX Maintenance Section, group affiliate POSCO M-TECH, and suppliers YEONGNAM Industry and DAEMYUNG, considering the characteristics of a wide range of work environments, and began the field pilot application. A field pilot application plan for automatic control of forklifts was established, and the full-scale application began in collaboration with POSCO DX with the goal of completion in August.
However, the schedule was postponed several times due to many technical difficulties. These difficulties included the lowered human recognition rate of the AI camera depending on the lighting in the factory and having to develop a control algorithm specifically for each forklift model, as there were nine models from different manufacturers such as Hyundai, Doosan, and Clark, and all models had different circuit configurations. In addition, there were problems with ECU programming that caused errors and made forklift repairs difficult. Field workers found it inconvenient to use additional devices related to the automatic control system of the forklift. So how could these problems be solved?
Process of improving the safety braking system for forklifts
POSCO identified areas for improvement with employees using forklifts in the field and began to supplement technology with POSCO DX. Forklifts using technologies from Taeyang Electric (AI camera) and FAE (LiDAR sensor) were installed in Electrical Steel Sheet Factory 2 and Cold Rolling Mill 1, respectively, to compare the performance of various sensors, and Taeyang Electric formed a separate research team to improve the recognition rate of the AI camera.
In addition, after extensive testing with various forklift models, we customized the core devices that make up the automatic control for each manufacturer. The overall system structure was changed to meet the conditions of “excluding ECU programming and unconditional repair service by the manufacturer.” We significantly improved usability by taking into account the driver’s working environment and convenience with a thorough site check in advance, surveying the desired detection distance for each department, and reflecting it during installation. We also took care of the convenience of field workers by installing a highly visible alarm and a button to temporarily release the braking system. POSCO Group’s smart safety technology, “safety braking system for forklifts,” was improved based on a meticulous preliminary survey and began operation in the field in November.
Site-specific system development for diffusion throughout the company
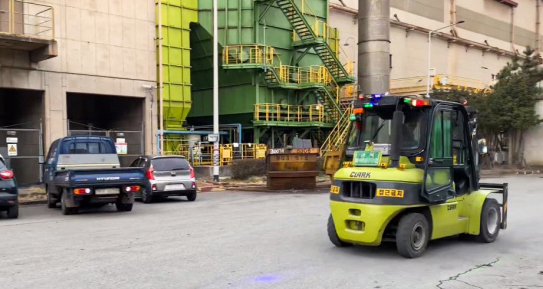
▲Forklift equipped with ‘Safe Braking AI System’.
The safety braking system for forklifts is a technology developed to prevent the risk of workers being hit or crushed, but since it also adjusts control, a momentary technical error can cause a secondary accident. The recognition rate of the improved camera is also 97%, which is less than 100%, so it is not a perfect automation technology.
In the future, POSCO Group plans to legally review secondary accidents and risks of the automatic control system for forklifts and establish a maintenance and repair support system while continuously increasing the camera recognition rate. Furthermore, POSCO will strive to reduce accidents caused by vehicles and machinery by expanding and operating the safety braking system for forklifts throughout POSCO Group.