From a general point of view, the predominant understanding is that steel is far from eco-friendly. According to the World Steel Association (worldsteel), however, steel’s competitiveness and benefits to the environment can be highlighted especially when assessed in terms of the life cycle.
POSCO, at the forefront of assessing the impact of steel in its full life cycle, has been making a sizable investment to achieve ‘clean steel’ since its establishment. Yoon-Gih Ahn, the Senior Vice President of Energy and Environment Business Office at POSCO offers valuable insights for the company and the steel industry. POSCO Newsroom reports.
l Sustainable circular economy and steel products
We are now entering an era of “sustainable competitiveness” defined as looking beyond simple economic performance to pursue environmental soundness and balance with the social aspect. Considerable economic research, including Wernerfelt, B. (1984), M.E. Porter (1996), Prahalad, C. K. (2002), Wilson, M. (2003), and Y.G. Ahn (2007), has suggested this concept as a direction for corporate competitiveness. Given the imminent depletion of the natural resources that fueled the Industrial Revolution, such as oil, coal, and gas, and growing environmental concerns regarding the use of fossil fuels, both academia and industry are paying keen attention to sustainable competitiveness as a new means for achieving competitiveness. At the 2012 World Economic Forum, economists and scholars stressed the importance of a transition by the global economy to a circular economy to address pressing environmental issues such as resource scarcity, climate change, fine dust, wastes, and toxic chemicals—the key challenges for sustainable competitiveness.
When looking at the steel industry from the perspective of sustainability and a circular economy, process and product should be considered separately. In terms of the steel-making process, steel is not free from environmental concerns such as energy scarcity, CO2, fine dust, and wastes.
For the products, however, the drawbacks of the steel-making process can be overcome. Lightweight steel products help to reduce CO2 and NOx emissions and improve fuel efficiency and give a tremendous opportunity to the overall industrial ecosystem and society.
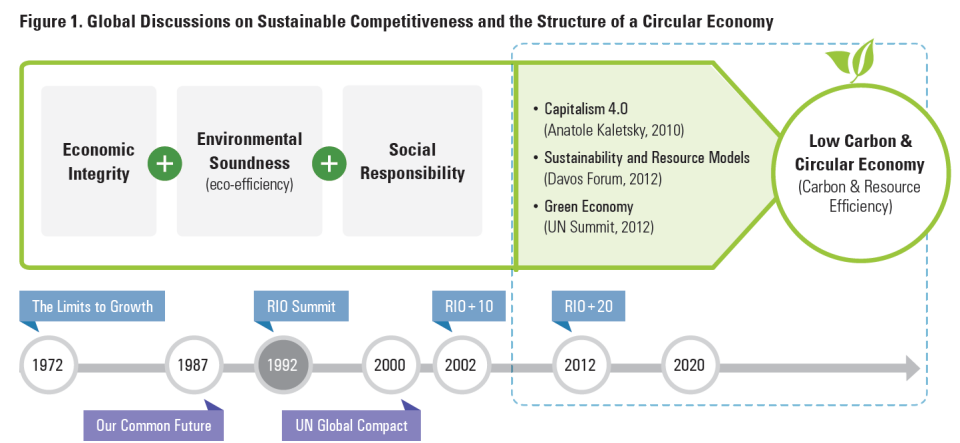
Source: compiled by the author
In particular, steel has a much longer service life than other materials, so it contributes greatly to improving efficiency in a circular economy. With its high recycling rate, infinite recyclability, and relatively easy removal of impurities, steel has proven to be a key material for addressing resource scarcity.
Considering the extent of current iron ore reserves, steel can become a cornerstone for a sustainable circular economy and industrial ecosystem. Steel slag, a by-product of steelmaking, provides an alternative to cement and can be used as a fertilizer to help increase agricultural production, demonstrating how steel can stand at the center of the shift to a new industrial ecosystem.
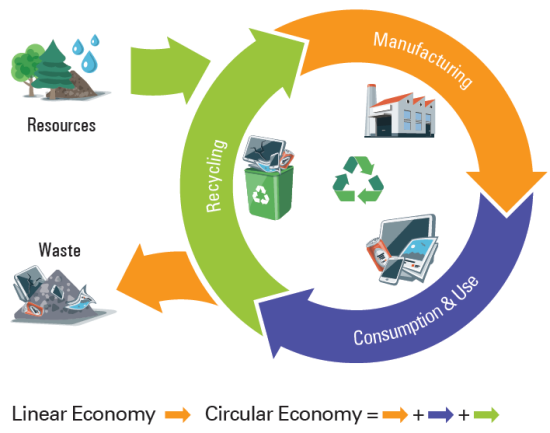
Source: Shutterstock
Life Cycle Assessment (LCA) is a technique used to determine the potential impacts of a product at all stages based on life cycle thinking. The global community uses this technique to identify products suitable for a circular economy. Ever since the International Organization for Standardization (ISO) adopted LCA as a global standard in the mid-1990s, it has been used for product development and marketing strategy. ISO is also discussing a new and improved global standard for a circular economy as a global standard.
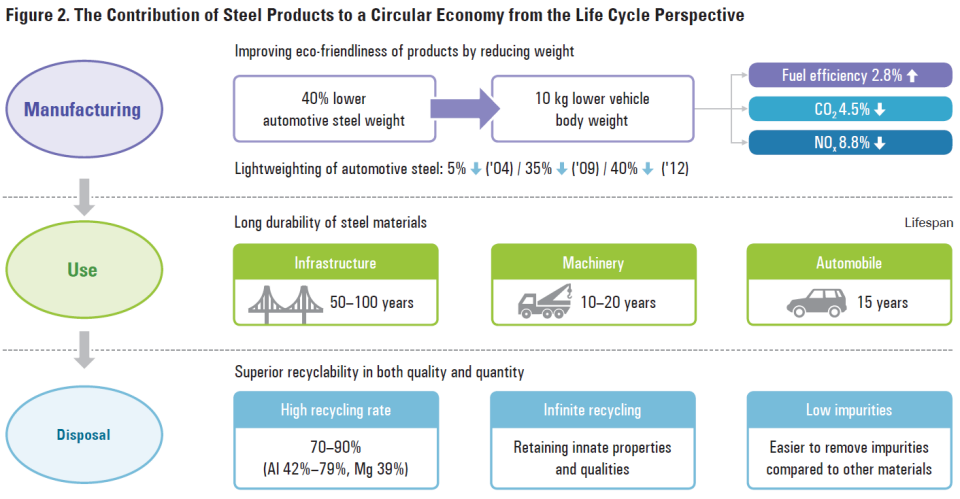
Source: POSRI
Taking up the OECD’s Polluter-Pays Principle(PPP) and Process and Product Methods (PPM), the European Community adopted its Integrated Product Policy (IPP) based on life cycle thinking and life cycle assessment in 2000. Several directives and regulations have taken effect based upon the IPP, including the Restriction of Hazardous Substances (RoHS) in Electric & Electronic Equipment, Waste Electrical and Electronic Equipment (WEEE), End-of-Life Vehicle (ELV), and Registration, Evaluation, Authorization, and Restriction of Chemicals (REACH).
These are already being used as a basis for global and domestic regulations and will become a sticking point in future trade concerns.
Clearly, steel products will be subject to more stringent regulations. This article discusses POSCO’s preparations and measures for improving its sustainable competitiveness in the face of shifting global and domestic market conditions.
l POSCO’s Responses for a Circular Economy Era
The economic system of the future will pursue not only traditional economic profits, but also environmental soundness and social needs for sustainable growth. This requires all economic players to cooperate on dealing with environmental and social challenges. In particular, sustainability will be highly dependent on the capability to alleviate or address resource scarcity. In this process, the recyclability or eco-friendliness of resources will have a significant influence. For these reasons, POSCO has been seeking the improvement of the steel-making process, product development, and utilization of by-products from the full life cycle perspective. Considering that the steel-making process is energy-intensive and burdensome to the environment, the company has been working to enhance energy and carbon efficiency and emplace eco-friendly process technologies. It has designed high-performance lightweight steel products with improved recyclabilityand circularity. By doing so, POSCO helps to make steel-consuming industries less carbon-producing and more eco-friendly. This contributes to the overall sustainable competitiveness of all global industry. Furthermore, it undergoes third-party monitoring and supervisions (conformity assessment) to assure the sustainability of products and ensure customer trust in a society seeking low-carbon eco-friendliness.
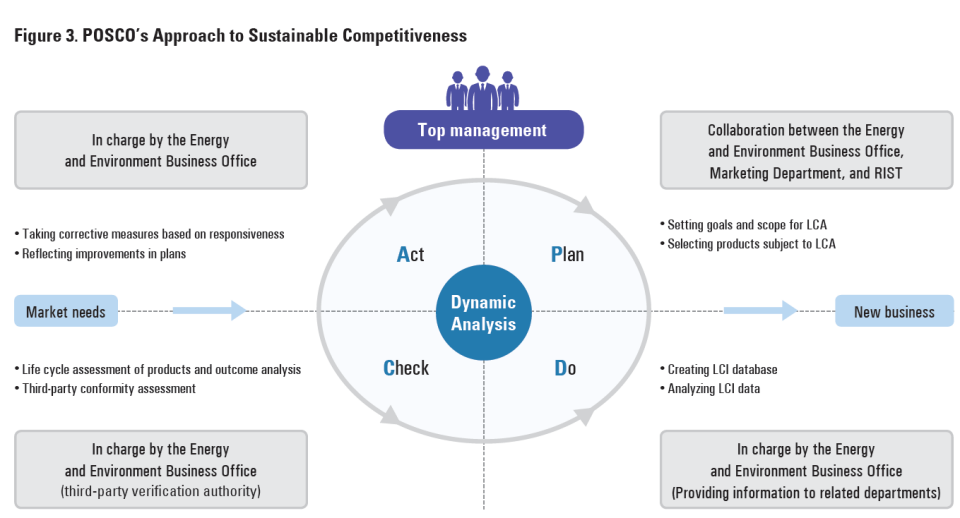
Source: Compiled by the author
To this end, POSCO has adopted Life Cycle Thinking and Analysis as a basic methodology and been interested in the global discussion on Life Cycle Analysis since the mid-1990s. POSCO has developed the Life Cycle Inventory (LCI) database and analytics suitable for steel-making processes and products. It has also actively participated in the global discussion surrounding Life Cycle Analysis, such as Environmental Labeling (ISO
14020) and Life Cycle Assessment (ISO 14040)under ISO/TC/207. In addition, it has developed products and improved recyclability of by-products from the sustainability perspective and it has been certified by international certification bodies to ensure customer trust in the eco-friendliness of its products and by-products. POSCO has a dynamic Plan-Do-Check-Act (PDCA) approach in place for continual improvement. It is conducting Life Cycle Thinking and Analysis from the PDCA perspective for improving circularity of products. The “Plan” phase sets the goals and scope for LCA and selects designated products.
During the “Do” phase, database is compiled for LCA. In this process, informatization by data analysis is important for interpretation of the environmental impacts from the perspective of whole life thinking.
The “Check” stage conducts Life Cycle Assessment for evaluation, and the outcomes are subject to third-party conformity assessment.
Finally, in the “Act” phase, the outcomes are reported to top management and used to take corrective action taking into account the original targets. The next plan phase is then initiated and the PDCA cycle is infinitely repeated for troubleshooting and continuous improvement.
These processes are conducted in close cooperation with the Energy and Environment Business Office, Department of Technology Management, RIST, and Marketing Department.
l POSCO products from a sustainability perspective
POSCO believes that sustainable competitiveness can be attained only when process and product are innovated in terms of eco-friendliness and recyclability. Therefore, it has spared no efforts in producing steel products offering higher performance and lighter weight. Based on whole life cycle thinking, it is applying LCA to develop products from the perspective of sustainable competitiveness and improve especially their eco-friendliness.
Representative products to which LCA was applied include advanced high strength steel (AHSS), Hyper NO electrical sheet, Giga Steel, and PosMAC. POSCO has also developed its PosMent cement with a higher slag content to improve overall resource efficiency and reduce CO2 emissions. Through the recycling of steel scrap and off-gas, it is strengthening its eco-friendliness and improving profitability. Below are details on some examples of POSCO’s preparations for a sustainable circular economy.
(1) Advanced high strength steel (AHSS) – Lighter car bodies to raise fuel efficiency
AHSS applied to gasoline vehicles reduces vehicle body weight, improving fuel efficiency and reducing greenhouse gas emissions.
In close cooperation with its domestic automaker partners, POSCO begins suggesting steel products from the design stage and has developed lightweight products that enhance fuel efficiency and reduce greenhouse gas emissions.
AHSS is about 10 percent lighter but more than twice as strong as conventional steel sheets for cars. A new 2016 model using more AHSS is 130 kg lighter than the 2015 model with less AHSS but boasts even higher crash performance. Annval fuel use of a vehicle is reducsd by 140ℓ CO2 emissions by 301kg and fuel costs by KRW 201,882. If Applying the Lifetime Driving Distance (LTDD), the new model can reduce fuel use per vehicle by around 2 kℓ, CO2 emissions by 4.4t CO2 and fuel costs by KRW 3 million.
(2) Hyper NO electric sheet – Reducing electricity consumption of home appliances through improved motor efficiency
Improving power efficiency in home appliances to reduce energy consumption and cut greenhouse gas emissions.
POSCO has developed a top-grade non-oriented electrical steel, Hyper NO. Hyper NO can be used in motor cores, a key component in motors that converts electric power to mechanical power. It helps to make motors more efficient and improves the energy efficiency of home appliances. Motor cores with Hyper NO minimize core losses, thereby improving the power efficiency of home appliances using compressor motors with these motor cores.
In a pilot test, a refrigerator using a motor with Hyper NO in place of a compressor motor with a conventional motor core saw its compressor motor efficiency improve by up to 1.5% and electricity use efficiency rise
by 1.2%.
If these figures were applied to the total sales for the refrigerator model, it would reduce annual electrical power consumption by 2.1 GWh and save annual electric costs of KRW 390 million.
Moreover, assuming that a high-efficiency motor with Hyper NO steel were used in all refrigerators sold in Korea, it would reduce annual electrical power consumption by 89.5 GWh and annual electric costs by KRW 16.8 billion.
(3) PosMAC and Giga Steel – Building the Life Cycle Inventory database and conducting third-party certification
Preparing for a low-carbon circular economy characterized by eco-friendliness and recycling of resources through a full life cycle database and third-party certification.
Acknowledging that the future will be characterized by a circular economy dominated by sustainable competitiveness, POSCO believes that eco-friendliness, and recyclability in particular, will become a key to product quality. The company has begun evaluating the eco-friendliness of its steel products based on whole life cycle thinking. A first for a Korean steelmaker, POSCO established the Lif Cycle Inventory database (LCI).
Since January 2018, it has been preparing for obtaining Environmental Product Declaration (EPD)4 certification at home and abroad. It has selected PosMAC5, the construction steel materials produced at the Pohang Steelworks and Giga Steel6 for automobiles produced at the Gwangyang Steelworks as its WP (World’s Premium) products.
In May 2018, it compiled quantitative environmental information on PosMAC taking into consideration the extraction of raw materials, supply, manufacture (cradle-to-gate) and recyclability. This information can be used for setting directions for reducing the environmental impact of the steel production process by considering the use of resources and energy in the whole life cycle of steel products and potential effects on climate change.
In addition, POSCO is building the environmental information on Giga Steel from the whole life cycle perspective. It plans to obtain Environmental Product Declaration (EPD) certification from an international certification body and the Korean Ministry of Environment by August 2018.
(4) PosMent – Eco-friendly cement with a higher slag content
Developing “PosMent” with a higher slag content, a by-product from the steel-making process, to strengthen the circular industry ecosystem and reduce greenhouse gas emissions.
Ground-granulated blast furnace slag is a sandtype slag manufactured by spraying high-pressure water jets on molten slag from a blast furnace. It has a chemical composition similar to cement. As an alternative to cement clinker,7 granulated slag is used up to 5% in a cement mixture to conserve natural resources such as limestone and reduce energy and CO2 emissions associated with cement calcination. In cooperation with RIST and POSCO E&C, POSCO developed PosMent in 2012, which has a higher slag content but demonstrates improved physical properties such as pressure resistance and strength. It can reduce CO2 emissions by up to 60% compared to conventional cement.
In 2017 alone, the company used 10.95 Mt of ground-granulated blast furnace slag for the production of cement and reduced 8.6 Mt of greenhouse gas emissions.
(5) Utilization of process off-gas – Innovative energy efficiency improvement and CO2 emissions cuts
Using off-gas created in the steel-making process to improve energy efficiency, reduce CO2 emissions, and minimize electricity costs.
POSCO collects most of the off-gas (BFG, COG, LDG, FOG) created in the steel-making process for use as a process energy source and power generation. In 2017, Pohang Steelworks and Gwangyang Steelworks self-supplied 72% of their electricity needs through energy collection equipment, off-gas generators, and LNG power generation equipment, such as Coke Dry Quenching (CDQ) and Top Gas Pressure Recovery Turbines (TRT). This figure has increased by 6%p from the generation rate of 68% in 2016.
To prepare for stricter greenhouse gas restrictions and rising electricity prices in the future, the power generation rate using off-gas will continue to increase.
l Suggestions for the future
It is an undeniable fact that the global economy is shifting toward a low-carbon and eco-friendly sustainable circular economy in order to address the potential depletion of energy resources, climate change, and air pollution. The steel industry will not be exempted from these changes in the business environment.
Although steel is a CO2-and energy-intensive industry, recently developed lightweight and high-strength steel products bolster the sustainable competitiveness of the steel industry, demonstrating that the steel industry can become a representative industry for sustainable competitiveness in a circular economy.
POSCO utilizes Life Cycle Assessment for product development. The company analyzes the recyclability and eco-friendliness of its steel products and by-products from the whole life cycle perspective. It applies the analytic outcomes to product development and processes to cut energy and CO2 emissions across the entire industrial and social ecosystems. In particular, it seeks to explore new markets by ensuring the eco-friendliness of both its products and by-products through third-party certification.
Thanks to such efforts, the steel industry can remain a staple of industry in the circular economy and POSCO will stand firmly as a sustainable, competitive company.
* This article has been reproduced from Asian Steel Watch, a bi-annual English journal specialized in the Asian steel industry. The original version Vol 5. (2016.06) can be accessed and downloaded directly from POSRI’s website here.