To adapt to the rapidly changing Chinese automotive market, POSCO is actively managing 12 processing centers in China, the world’s leading car production hub, with a strong emphasis on eco-friendly vehicles. POSCO’s integrated processing centers in China practices ESG management through organic collaboration among processing centers, by addressing regional customers collectively, by engaging in active corporate citizenship activities and through the use of renewable energy.
In 1994, POSCO founded its first international processing center, the CTPC, in Tianjin, China. Since then, the company has further expanded its operations in China, establishing four production corporations, including POSCO China, and adding 11 additional processing centers to its network. In China, POSCO currently manages processing centers in various locations, such as Suzhou (CSPC, CZPC), Xianyang (CLPC), Gilim (CJPC), Poshan (CFPC), Yantai (CYPC), Chongqing (CCPC), Chengdu (CDPC), Qingdao (CQPC), Tianjin (CTPC), and Wuhan (CHPC).
The China Integrated Processing Center processes coil-shaped steel materials into various sizes and shapes as per the requirements of its customers, which include automotive, appliance, and construction companies. It also offers logistics services, including material storage and transportation, to reduce the logistical burden on its clients. POSCO in China has integrated its processing centers into the CTPC, thereby fostering a flexible and agile response system for regional customer needs and creating synergy through organic collaboration. In addition, POSCO actively practices ESG management through various methods such as active corporate citizenship activities and the use of renewable energy.
Distinguished organizational culture management and efficient safety practices
The China Integrated Processing Center is known for its well-established organizational culture, with many long-term employees. It operates an internal channel for gathering employee feedback, continuously monitoring the opinions of employees through the VOC (voice of customer) system and providing feedback within 24 hours. Thanks to this attentive organizational culture management, the turnover rate, which was 26% in 2019, decreased to 3% by 2023, and the length of service has increased, creating a “happy workplace.”
Furthermore, the organization has been innovating its culture through collaborative efforts in creative and innovative activities involving all employees. The number of improvement initiatives, which was 37 in 2020, increased to 531 in 2023, resulting in a cumulative total of 1,073 on-site improvements. Innovative improvements have been made in the sales, purchasing, and logistics areas. In the Sales Department, the introduction of an e-sales platform led to a 100% success rate in scrap sales, promoting transparency and fairness in business operations. In the Purchasing Department, 1,246 items that had previously been managed manually were systematized, and improvements in logistics routes within the factory significantly reduced waiting times during loading.
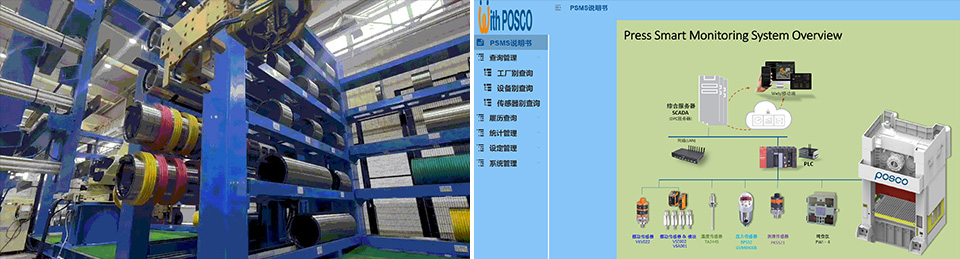
▲Unmanned knife replacement facility using a robot (left) and the newly established ‘Press Smart’ preliminary maintenance system.
Efficient safety management activities that focus on identifying core aspects are also noteworthy. The Processing Center has significantly improved safety levels through efficient safety management, with all employees equipped with safety expertise actively participating in safety initiatives. As a result of employees voluntarily engaging in potential risk mitigation activities, the number of identified ideas for mitigating potential risks increased from 1,139 in 2020 to 2,411 in 2023. This was made possible through the various policies that support safety improvement activities, including the streamlining of the proposal process and the expansion of incentive systems such as audit cards.
With ongoing efforts in equipment resilience and smartization activities, the equipment failure rate has consistently decreased annually, reaching 0.02% in 2023. In addition, the CTPC has established a maintenance system and achieved automation and unmanned operations, and is now ready for future investments in smart technology and collaborative processes for processing equipment.
Setting an example in ESG management for carbon Reduction

▲China Integrated Processing Center (left), which was introduced as an excellent company in safety management in Suzhou Daily, the largest media in Suzhou City, and the Tianjin City government-certified low-carbon environment excellent company award in 2022.
The China Integrated Processing Center is playing an exemplary role as a processing corporation based on recognition and trust from the local Chinese community. The Chinese government is currently pursuing the “Industrial Green Development Plan,” which aims to transform industrial zones into low-carbon manufacturing environments by 2050. In line with this, since 2017, it has been selecting and commending a “Green Factory” that possesses low-carbon manufacturing environments. The CTPC in Tianjin received government certification as a “Green Factory” in 2023. Processing centers such as the CSPC in Jiangsu Province, the CYPC in Shandong Province, and the CHPC in Hebei Province are currently undergoing evaluation for “Green Factory” certification.
The China Integrated Processing Center has also established a green energy production system by installing solar panels, thereby contributing to carbon Reduction. By installing solar panels covering 67% of the total roof area at the CSPC factory, equivalent to 10,000 square meters, it has saved approximately 639,000 yuan (around KRW 100 million) in annual electricity costs and reduced annual CO₂ emissions by about 11,000 tons. During the verification of renewable energy source generation, the monthly expected power generation from the solar panels was found to be 90 MWH, surpassing the predictions of the simulation conducted before the investment. The company is expanding its renewable facilities by installing streetlights powered by wind and solar energy, thereby achieving self-powering through renewable energy sources.
Let’s take a closer look at the impressive performance of the CTPC among the 12 POSCO China Integrated Processing Centers. The CTPC stands out for its smart safety management and active corporate citizenship activities, standing out as an exemplary processing center.
The CTPC, established on October 26, 1994, in Tianjin, China, is the first overseas processing center for POSCO. The CTPC processes and stores steel plates, and they sell these to car companies such as Beijing Benz, Great Wall Motor, and FAW-Toyota in the northern part of China. With a team of 150 dedicated employees, they are passionately committed to proving the capabilities of a leading materials company in the rapidly changing Chinese automotive market and are determined to make even greater strides.
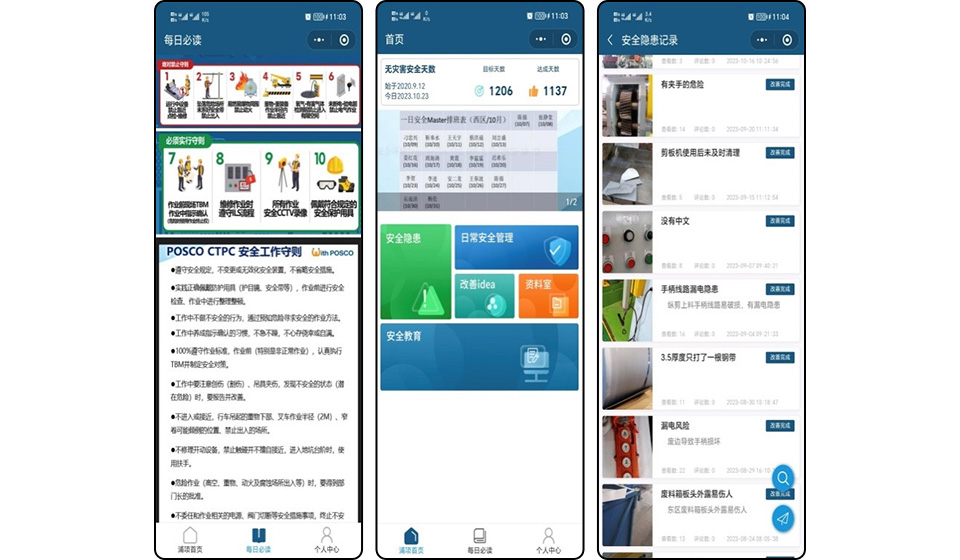
▲Integrated Safety Management Mini-App usage screen.
The CTPC has introduced the Integrated Safety Management Mini-App to effectively record and share information about safety activities that employees participate in. Previously, when employees identified potential hazards in the field, they had to take photos and send them to the safety manager, who would manually record and manage them in the potential hazard log. Sharing the recorded information with all employees immediately was also a challenge. With the implementation of the Integrated Safety Management Mini-App, employees can now quickly and easily report potential hazards they find in the field. This information is then shared with all employees. The app allows for direct checking of the improvement process and results.
Full employee engagement in safety certification and emergency response training
The CTPC has overturned the old idea that only managers or officials are responsible for on-site safety. Instead, all on-site employees are trained to be safety experts. The company encourages all employees to get safety certificates and makes sure they receive at least 32 hours of training through online lessons and other methods. As a result, all 59 production line workers have obtained safety management certifications through final evaluations. Since all employees started becoming safety management experts and taking charge of the workplace, the annual number of voluntarily proposed ideas for identifying latent risks has been on the rise. This trend reflects an enhancement in the safety competence of the employees.
The CTPC regularly participates in emergency response training organized by the Tianjin Development Zone Red Cross and conducts quarterly emergency response drills. 81 team members have successfully completed emergency response training, earning qualifications in CPR and hemostasis. The CTPC has also taken measures to equip the workplace with essential emergency response equipment, including AEDs, oxygen resuscitators, and emergency medical kits. In emergency training, employees learned how to respond to different situations, such as fires, how to use fire extinguishers, and how to handle incidents such as suffocation in confined spaces or electric shock accidents during work. In particular, the CTPC offers practical training through a combination of VR education and hands-on practice to ensure employees can respond swiftly and appropriately during emergencies.
ILS activities that address the root causes of disasters
The CTPC has established an isolation locking system (ILS) to block, isolate, and secure energy sources, thereby eliminating fundamental causes of accidents. The ILS has three locking types: “personal locking” for individual work, “facility locking” for work involving two or more people or two or more locations, and “group locking” for tasks with numerous workers. Each locking type is differentiated by padlock colors: red (personal), yellow (2 or more), and green (group). With the introduction of the ILS system and the rigorous enforcement of safety protocols during maintenance and inspection tasks, the likelihood of unexpected facility operations, which could potentially lead to accidents or incidents, was proactively mitigated, ensuring the safety of employees.
In addition, CTPC employees always check for safety risks on the job and actively work on improvements. One notable activity involved identifying the risk of blind spots during forklift operation, which led to the creation of a speed limiter and an AI video collision prevention system, effectively stopping accidents from happening. The CTPC achieved 1,146 days without accidents! They consistently maintain on-site safety through efficient safety management activities that target key safety points.
Corporate citizenship activities focused on coexisting with the local community
Driven by a sense of social responsibility, the CTPC has strived to develop alongside the local community. In particular, it actively helps the less fortunate members of the local community and also engages in corporate citizenship activities aimed at nurturing local education initiatives and skilled individuals and aiding in their employment.
On June 1, 2023, the CTPC invited elementary school students from the Tianjin area to visit the company and provided them with opportunities to experience corporate culture and safety education. The students learned about the CTPC through POSCO’s in-house recreation program and had an enjoyable time, even receiving prizes. On September 12, 2023, 14 CTPC employees engaged in DIY activities and assisted with rehabilitation therapy at a local autism rehabilitation center in Tianjin, where they spent time with the children. They also provided various support items, including food and gifts. Then, on October 23, 2023, the CTPC signed an agreement with Tianjin Polytechnic University to provide graduating students from relevant departments with opportunities to work and grow in their respective fields. This initiative has become an opportunity to support Tianjin’s youth, who are burdened by high unemployment rates, fostering mutual growth.
In addition, POSCO’s integrated processing centers in China and the CTPC are actively involved in environmental cleanup and tree-planting activities, biodiversity conservation, and wetland park preservation. These initiatives are aimed at promoting POSCO’s corporate citizenship values as it strives to enhance the well-being of the local community and its residents. It will continue to work towards making POSCO a “100-Year Company” through systematic organizational culture management, smart safety activities, and corporate citizenship activities that inspire the local community.