Using virtual environment simulation technology to train AI models and perfect ‘physical AI’
Leading the spread of AX in the industrial field with applications such as coil unloading systems for tens of tons of steel products
POSCO DX (President Shim Min-suk) is accelerating its manufacturing AX (AI Transformation) by advancing its ‘Physical AI’ technology based on virtual environment simulation and applying it to the field one after another.
POSCO DX announced that it has developed an AI model that replicates a real-world factory in a virtual environment and established a ‘physical AI’ development system that efficiently supports AI learning and verification prior to field application. Facilities and sensors at industrial sites are greatly affected by the physical environment such as inertia, acceleration, and noise, and by implementing conditions that can be encountered in the real world in a virtual space and conducting various simulations, AI can learn the optimal movement of facilities.
At actual industrial sites, there were limitations in acquiring field data and testing AI models due to disruption of operations or safety and security reasons. POSCO DX utilized virtual environment simulation to solve these issues and is expected to significantly reduce the time and cost of AI model development and field application.
POSCO DX has implemented virtual environment simulation by adopting Isaac Sim of NVIDIA Omniverse platform. Isaac Sim is a SW that supports verification by simulating the physical environment precisely with actual sensors and systems in a virtual environment.
POSCO DX recently built a specialized optical laboratory in its Pangyo office building to further advance its ‘physical AI’. The optical laboratory is a space where the response of sensors and precision according to specifications, which are difficult to identify in AI simulations, are tested by artificially creating an environment similar to the actual site in terms of lighting, temperature, and movement. By reflecting the sensor data verified here in the AI simulation, it is evaluated that the gap between the virtual and actual sites has been minimized, enabling more efficient simulations.
On the other hand, ‘Physical AI’, which was the topic of this year’s CES 2025, refers to AI that recognizes the surrounding environment and interacts with the real world by controlling physical systems. ‘Physical AI’By applying , AI can recognize and judge various operation situations and control and operate facilities directly with the on-site control system (PLC, Programmable Logic Controller), enabling unmanned operation. POSCO DX is leading the spread of ‘Physical AI’ in industrial sites by converging AI technology with existing IT (information technology) and OT(automation technology).
POSCO DX ‘physical AI’ to cranes that transport atypical products with different sizes and packaging forms.is prioritizing the application of In the first half of this year, POSCO DX developed an AI model to automate the unloading of coil products transported on trailers into cranes, and plans to spread it horizontally by conducting virtual test drives and applying it to the field.
Yoon Il-yong, head of POSCO DX AI Technology Development Center, emphasized, “POSCO DX is pursuing the implementation of ‘physical AI’ technology with the goal of ‘autonomous physical systemization of manufacturing facilities’ based on the convergence of AI, IT, and OT technologies,” and added, “We will strive to establish ourselves as a leading company in intelligent factories by advancing ‘physical AI’ utilizing physical development methodologies such as virtual environment simulation.”
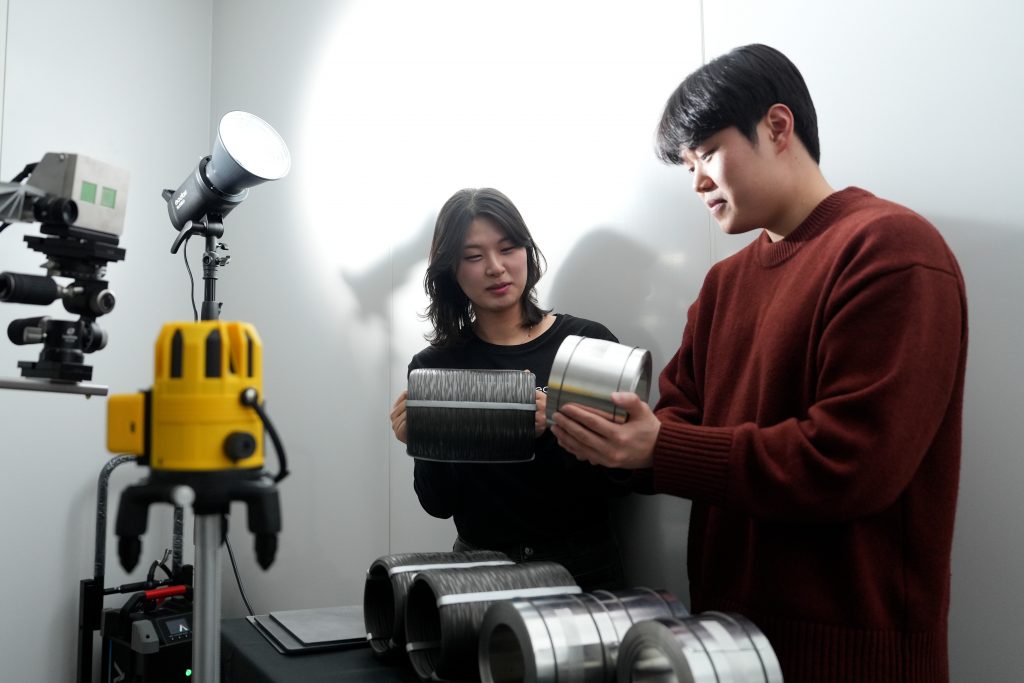
▲POSCO DX AI researchers are testing the physical environment, such as light and distance, of the coil loading and unloading site in the optical laboratory of the Pangyo building.