In Russia, existing oil field pipes operate in challenging conditions — in constant contact with the corrosive water which is a mixture of oil and concentrated salt solutions. The corrosive water limits the operation periods of the oil pipes to about two years. PAO Severstal, one of the world’s largest metallurgical steel companies, needed to develop a new steel grade to tackles these obstacles head-on.
The scientists at Russia’s NUST MISIS answered the call – they proposed an innovative technology for the production of rolled steel to manufacture corrosion-resistant field pipes with improved mechanical characteristics.
How will the new steel grade “SeverCorr” help reduce environmental risks and the operating costs of oil extraction? POSCO Newsroom presents worldsteel, “New Steel for Oil Pipelines Prevents Leaks.”
A newly-developed steel grade is improving the integrity of pipelines and reducing the environmental impact of Russia’s oilfields.
Oil extraction in Russia presents a particularly tricky environment for engineers. Pipes are constantly exposed to corrosion by a mixture of oil and concentrated salt, meaning that operation periods are cut short and accidents become increasingly likely. These can be particularly problematic, with surrounding areas becoming subject to dangerous levels of pollution in the result of leaks.
Repairs are not easy, either. Oilfields are often remote, and conditions can be hostile. The wilds of Siberia have weather conditions that contribute to the pipes requiring constant maintenance while simultaneously complicating the delivery and installation of replacement sections.
Thankfully a new, innovative technology from Russia’s National University of Science and Technology (NUST) looks to change the way such pipes are manufactured – increasing efficiency for companies and reducing not only operating costs and necessary repairs but also risk to the environment.
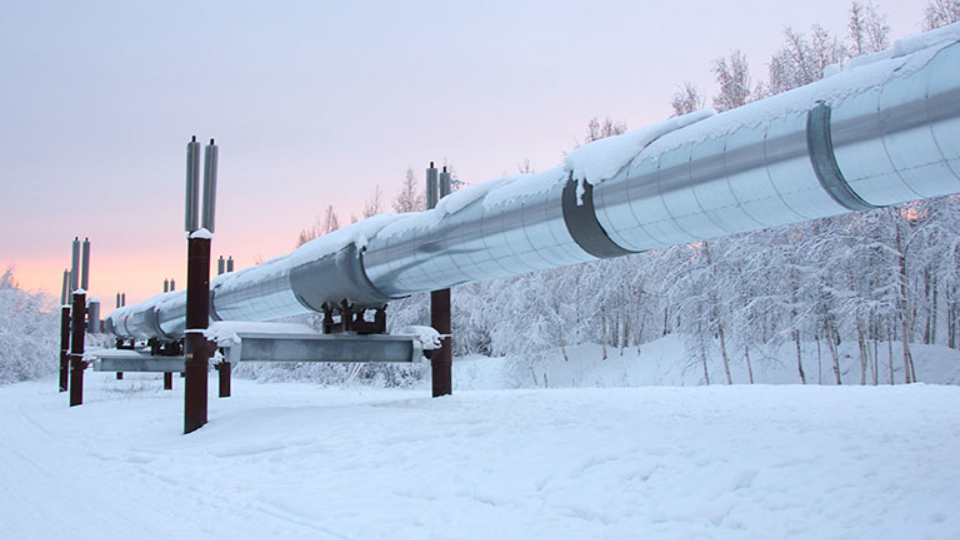
▲ Pipelines that service Russia’s oilfields must withstand extreme environmental conditions. (Image source: iStock)
l Making the Grade
At the centre of this innovative technology is a new steel grade – Severcor. The addition of chromium, copper and nickel during the steel’s manufacture means that the composition of the pipes can be carefully regulated, thus boosting their anti-corrosive properties. This could, researchers hope, “at least double” the lifecycle of the pipes, which in certain oilfield conditions can be as little as two years.
“The new technology provides increased corrosion and cold resistance,” explains Alexander Komissarov, one of the steel’s developers and research associate from NUST. “The development of new alloying schemes (adding impurities to the composition of the materials to improve the properties of the base material) and providing the necessary structural and phase steel composition to the production of rolled and sheet metal has become our main task.” According to NUST, this advanced steel grade will lower operating costs and reduce the environmental impacts of oil production.
“It is not just the steel grade’s intrinsic properties that have improved pipeline performance – the way the metal is shaped is also crucial.”
It is not just the steel grade’s intrinsic properties that have improved pipeline performance – the way the metal is shaped is also crucial. The new pipeline technology uses precise steel rolling techniques. What this does is twofold, reducing thickness and making that thickness more uniform. This uniformity means that the pipes are less susceptible to corrosion and to cold – a frequent issue in the freezing oil fields of Siberia.
The project has also developed several other steel concepts that researchers describe as “promising”. The NUST team says one set of melting and smelting experiments “passed the corrosion tests with flying colours”. Full-scale pilot tests for this new alloy are now being launched in Lukoil, Gazprom Neft, and Irkutsk, oil fields in West Siberia.
Severstal, the company that commissioned the university to research the production of the pipes, underlined the impressiveness of NUST’s technical achievement. The company said the that project involved high levels of “steel purity and structural uniformity” that represented “partly contradictory technological tasks”.
This makes it even more impressive that the research team were able to craft and implement this new steel grade – and could mean more impactful innovations for both steel and oil pipe manufacturing down the line.
The original content published on the worldsteel’s ‘Our Stories’ section is available at: https://stories.worldsteel.org/infrastructure/new-steel-for-oil-pipelines-prevents-leaks/