Tech companies are doing their best to keep consumers constantly connected to their gadgets. A large part of that has been advances in IoT (Internet of things) that has automated nearly everything from TVs to thermostats through M2M (machine to machine) communication. Today’s connected devices can communicate with each other and operate based on changes in their environment without user input. Despite unbelievably rapid progress, many IoT tasks for consumers are seen as nice, but not necessary. Waking up to coffee that is brewed in sync with the alarm is certainly a perk most people would enjoy, but it is not something that could not be done with a little extra effort.
While consumers are able to see benefits added to their daily lives with IoT, it is the adoption in the industry and manufacturing sectors that are seeing the most significant economic gains, reductions in waste, and higher quality production. IoT is expected to see massive growth in the next ten to fifteen years, and most of that growth is expected to come from enterprise adoption, or what is now called IIoT, the industrial internet of things.
Below we take a look at how businesses are implementing IIoT and how it is revolutionizing industries all over the world.
Volkswagen Truck & Bus Launches RIO Platform
Beginning in 2017, Volkswagen Truck & Bus began offering its RIO platform, an open and cloud-based “operating system.” RIO is unique in that it can connect multiple pieces of the global supply chain regardless of brand. Because the shipping and logistics industries utilize many different brands and types of equipment, it has been difficult to make the process more connected and more sustainable – but RIO does just that.
Shippers, dispatchers, carriers, drivers, and recipients can all be connected with a uniform logistics platform that includes forecasting features. RIO looks at information from traffic, weather, and navigation and combines it with information from tractors, trailers, bodies, drivers, and orders so that it can offer recommendations in real time.
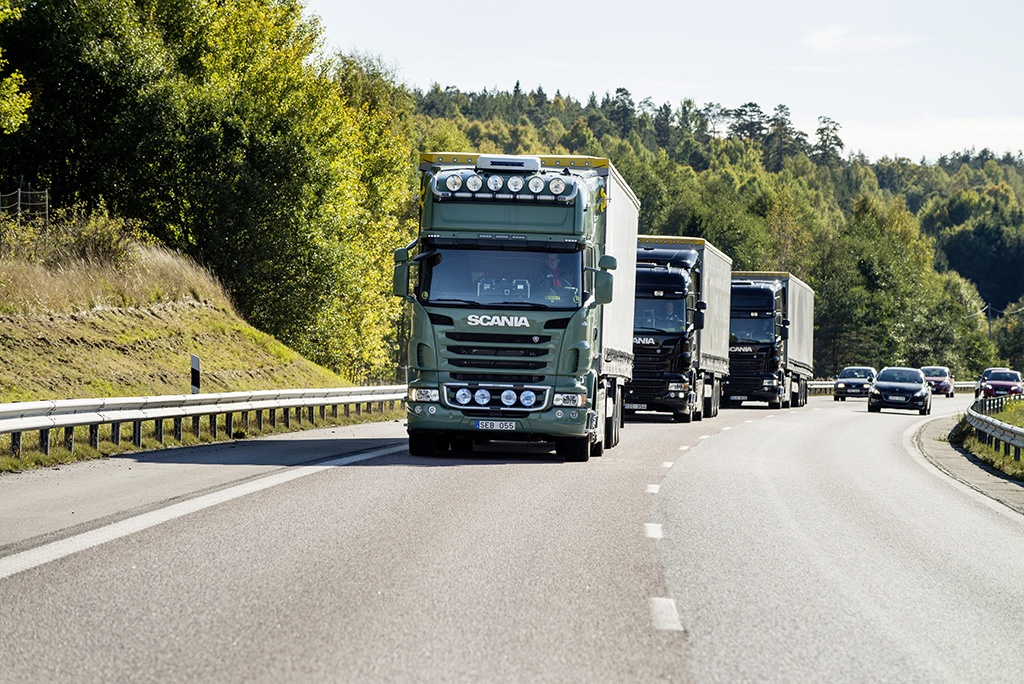
Volkswagen Truck & Bus utilize IIoT technology to help compile information across multiple brands and types of logistics equipment. (Photo courtesy of Volkswagen AG)
In utilizing IIoT technology, Volkswagen can streamline the vast information sources across brands that will help improve the transportation and reloading process. As Volkswagen Truck & Bus CEO Andreas Renschler noted, this is not just good for efficiency and the company’s bottom line, it is also good for the environment. Being able to real-time decisions through multiple sensors and input, there will be fewer empty trucks on the road and far less waste.
Caterpillar IIoT Saves Money, Increases Uptime
In the U.S., construction and mining equipment company Caterpillar is utilizing IIoT to help customers monitor their equipment to increase efficiency. Partnering with Uptake, a predictive analytics firm, Caterpillar sends data gathered from sensors on its products and sends it into the cloud for diagnostic analysis. Caterpillar then provides its customers with vital information related to their equipment so that they have the ability to plan maintenance schedules more efficiently. If customers can know that several parts are likely to need to be replaced, these can be fixed all at once while the equipment is offline instead of having each one break individually while in use. This ultimately helps prevent costly downtime providing customers with uninterrupted productivity.
Caterpillar also integrated advanced IIoT systems in their Marine Division to help monitor almost every aspect of their tugboats and shipping vessels. The generators, engines, GPS, air conditioning systems, and fuel meters are all connected and providing valuable data for the systems operators.
Caterpillar’s IIoT systems can now look at GPS and weather information to help guide the ship operators in how much power to use when operating their vessels. Also, when Caterpillar looked at performance data and hull cleaning correlations, they learned that dirty hulls were costing more than $5 million per year in decreased performance. By changing the cleaning schedule from once every two years to once every six months, they were able to save $400,000 per year per ship.
POSCO Implements AI Into Its Smart Factories
POSCO’s Gwangyang Works is one of the top automotive coated steel plants in the world, providing 10% of global supply. During automotive steel production, one of the most critical steps is the coating weight process. When coating weight is controlled manually, quality deviates depending on the skill level of the worker, inevitably resulting in significant amounts of wasted zinc, so POSCO implemented IIoT technology to improve efficiency and product quality & consistency.
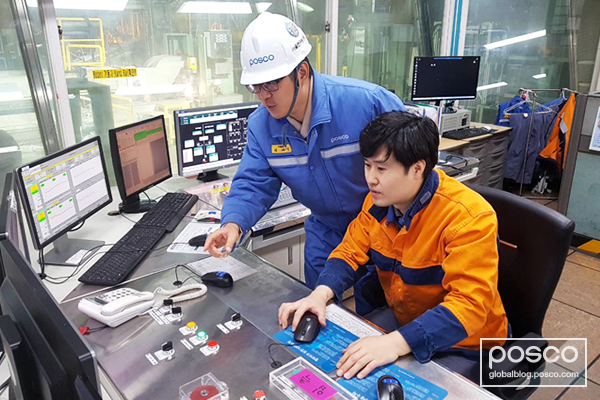
POSCO workers monitor the optimal coating weight predicted through IIoT and AI. It is now possible to collect hundreds of different types of data and make adjustments in real time for complex coating weights
This highly-sophisticated technology helps keeps the thickness of the coating layer consistent – even when operating conditions change suddenly. They have installed a data integration infrastructure that uses an automated control technology that predicts the coating weight of zinc in automotive steel to precisely control the Continuous Galvanizing Line (CGL). In combination with the coating weight system, they have also created a data pre-analysis system that can preemptively detect abnormalities. The implementation of this technology has helped to increase the quality of POSCO’s automotive coated steel while also decreasing production costs.
Advancements in IoT technology are changing the way people live, but behind the scenes, at manufacturing facilities around the world, IIoT is having an even greater impact. Companies like Volkswagen, Caterpillar, and POSCO are leading the way to create more efficient and sustainable production methods using IIoT.