포스코그룹은 안전과 지속가능한 미래를 위한 기술을 개발하고자 최선을 다하고 있습니다. 더 나은 사회를 만들어가는 포스코그룹의 우수한 신기술을 소개합니다. 이번 편에서는 강성, 내구성, 경제성뿐만 아니라 프리패브 공법을 적용해 사용성까지 모두 갖춘 도심 속 UAM 이착륙장, 포스코의 스틸 버티포트를 소개합니다. 포스코그룹 신기술에 대한 수다를 계속 이어가는 기술+잇+수다, 지금 시작합니다!
전 세계적으로 도심 교통 체증과 환경 문제가 심화하면서 이를 해소하고자 UAM(도심항공모빌리티, Urban Air Mobility)의 중요성이 부각되고 있습니다. UAM의 대표적인 교통수단으로는 eVTOL(전기수직이착륙 항공기, electric Vertical Take-Off and Landing)이 있는데요. 좁은 공간에서 수직 이착륙을 할 수 있어 따로 활주로를 짓지 않아도 되고, 배터리 기반 전기 에너지로 운용해 소음을 최대한 줄일 수 있다는 점에서 주목받고 있습니다. eVTOL 항공기가 도심 속을 드나 들려면 안전하게 이착륙할 수 있는 구조물이 필요한데요. 이 구조물을 바로 ‘버티포트(Vertiport)*’라고 부릅니다. 버티포트는 항공기의 이착륙을 도울 뿐만 아니라 승객의 탑승 수속을 위한 터미널 공간, 기체를 충전·정비할 수 있는 시설까지 갖춘 일종의 도심 공항 역할을 해 UAM의 핵심 인프라로 손꼽히고 있습니다.
*버티포트(Vertiport) : 수직을 의미하는 Vertical과 터미널을 의미하는 Port의 합성어
항공기가 이륙할 때 3분, 착륙할 때 8분 동안 항공사고가 가장 빈번하다고 해서 마의 11분이라고 하는데요. UAM도 버티포트와 근접한 지점에서 이착륙 시, 기체 주변의 기류가 버티포트와 상호작용을 하면서 불안정한 난류를 만들어 내면 장애물과 충돌할 우려가 있습니다. 따라서 기체 하중을 견디고, 돌발상황에 대비할 수 있도록 내구성이 우수하게 설계돼야 하죠. 이 같은 특성상 그간 버티포트의 주재료로 내구성이 좋고 가벼워서 다루기 쉬운 알루미늄이 많이 쓰였는데요. 가격이 비싸 상용화하기 어려운 문제가 있었습니다.
포스코는 가볍고 튼튼하면서 가격 경쟁력이 있는 버티포트를 만들자는 목표로 ‘스틸 버티포트’를 개발해 냈습니다. 알루미늄 제품과 강성은 유사하면서 두께는 얇고, 가격은 알루미늄 제품 대비 절반 이하로 낮췄습니다. 여기에 일반 도금 강판보다 내식성이 5~10배 우수한 포스코의 PosMAC을 적용하면서 유지관리의 우려도 덜었습니다.
주로 지표면이 아닌 건물 상부에 설치되는 버티포트 유형을 옥상형 버티포트(Elevated Vertiport)라고 하는데요. 고층으로 자재를 인양해야 하기에 중장비 투입을 최소화해 조립하는 게 특징입니다. 포스코의 스틸 버티포트는 15m 크기의 정사각형 버티포트를 18개의 모듈로 분할해 공장에서 사전 제작하고, 현장에서 조립할 수 있도록 프리패브* 공법을 적용해 시공과 해체가 간편하다는 사용 효율성까지 모두 갖췄습니다.
*프리패브(Prefab) : Pre-fabrication의 줄임말로 공장에서 부재를 미리 제작하고 현장에서는 조립만 해 구조물을 완성하는 공법
포스코 구조연구그룹과 강건재가전솔루션그룹은 건설 산업에서 포스코의 철강재나 기술이 기존 토목·건축 구조물에 접목될 때의 장점을 연구해 고객사 맞춤형 제품으로 개발하고, 판매까지 연계될 수 있도록 활발한 시장 조사, 연구개발, 기술 마케팅을 수행하고 있는데요. 연구 아이템 선정 기준으로 대개 시장의 크기·고객의 니즈·활용처를 검토하는데 미래 모빌리티 산업의 혁신이라 불리는 ‘UAM 수직 이착륙장 개발’ 과제가 이 세 가지 기준에 완벽히 부합했습니다.
고객의 니즈
2022년 한국공항공사와 MOU를 맺으면서 포스코가 버티포트 산업에서 할 수 있는 일을 함께 고민했고, 버티포트와 유사한 구조물인 기존 헬리패드의 단점*을 철강재로 보완할 수 있을 것이란 결론을 도출했는데요. 그 결과 ‘가볍고 경제적인 버티포트 개발’이라는 목표를 세울 수 있었습니다.
*헬리패드(Helipad) 단점 : 헬리콥터 또는 드론 등의 수직 이착륙을 위한 비행장으로, 보통 콘크리트나 알루미늄으로 만들어지는데 각각 무게가 무겁고 가격이 비싸다는 단점이 있어 UAM 이착륙장으로 상용화하기엔 어려움이 존재했음
활용처
지난해 포스코는 잠실 MICE·수서역세권 개발 현장에 민간으로서는 최초로 버티포트를 건설할 계획을 밝힌 ㈜한화 건설부문과 함께 포스코형 안전한 버티포트 설계 및 연구개발이라는 공통된 목표를 갖고 MOU를 체결했습니다. 당시 토목, 건축, 항공 등 여러 분야의 전문가들이 모여 실제 버티포트가 도입될 현장을 대상으로 필요성과 적합성을 검토하고 연구했는데요. 이는 스틸 버티포트 개발에 큰 명분과 동력이 됐습니다.
포스코는 지난해 10월, 구조연구그룹, 강건재가전솔루션그룹을 필두로 스틸 버티포트 설계 및 연구개발에 착수했습니다. UAM의 운용 효율을 극대화하려면 항공기가 접근하기 수월한 곳에 버티포트가 설치돼야 하는데 도심지의 일반 지표면에 설치하기엔 비행 장애물이 많다는 리스크가 존재했고, 별도의 넓은 부지를 확보하기 어렵다는 문제가 있었는데요. 따라서 건물 옥상에 설치하는 엘리베이티드 버티포트 형태로 개발하는 것이 적합하다고 판단했습니다. 이 유형의 버티포트를 건설하려면 건물의 하중 부담을 줄여야 하고, 고층으로 자재 인양 시 투입되는 인력이나 설비를 최소화해야 했기에 경량화와 모듈화가 핵심 과제였습니다.
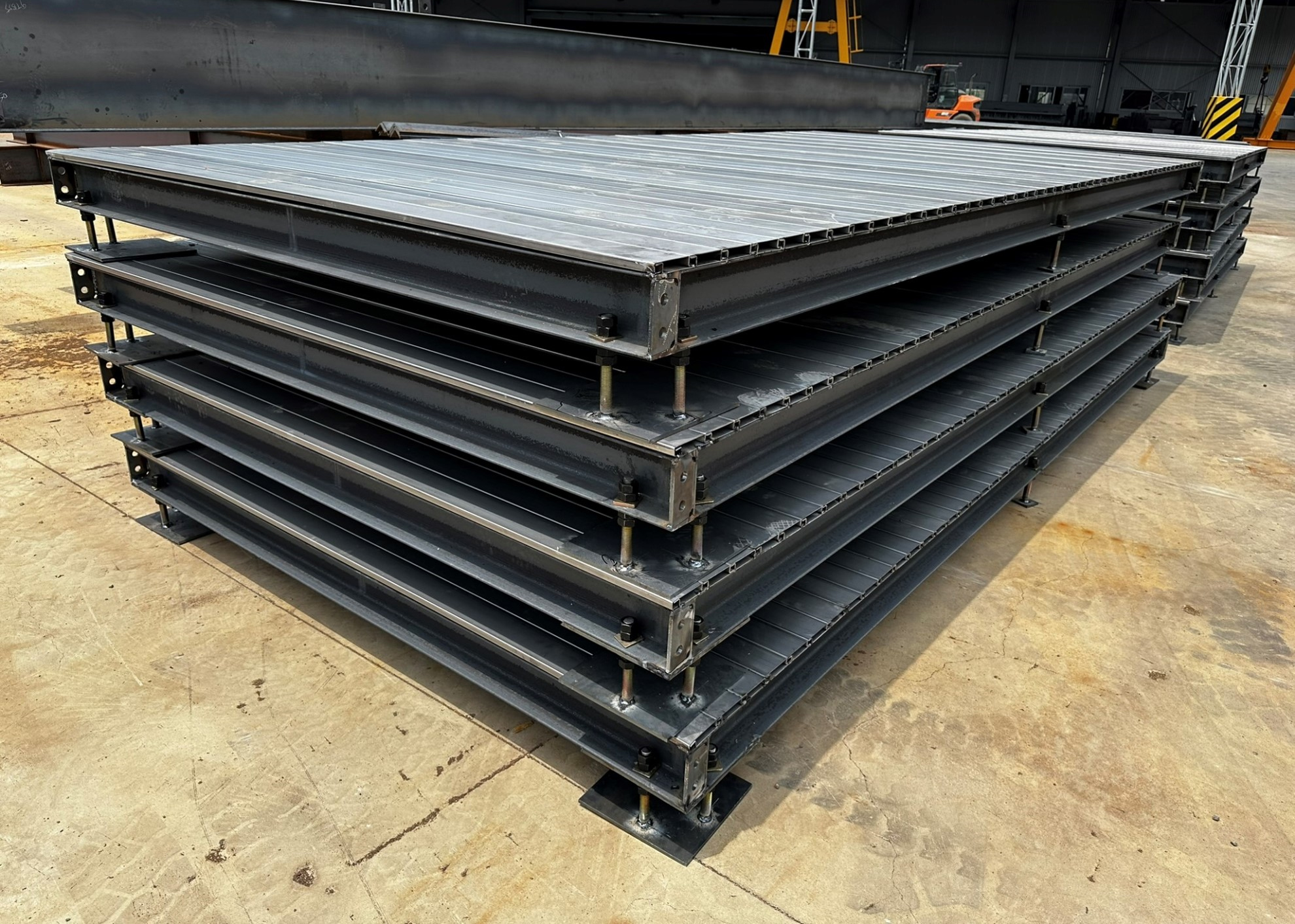
▲고객사 유석철강과 협업해 개발한 포스코 스틸 버티포트.
우선 경량화를 위해서는 강판의 두께가 1~2mm 수준으로 얇아야 했는데, 잘 휘어지는 문제가 있습니다. 이러한 경우 보강재 용접을 할 수 있지만 제작비가 비싸지고 변형 우려가 큽니다. 구조연구그룹은 용접하지 않고 보강재를 붙일 방법을 고민하다가 문득 롤포밍 공법*을 사용하면 흡사 보강재가 부착된 단면을 저렴하게 성형할 수 있겠다고 판단했습니다. 포스코 유관부서를 통해 고객사의 L형 데크를 추천받았던 것은 큰 기회였는데요. 고객사의 기존 설비를 활용하여 투자비를 절감하고, 고객사는 새로운 수요를 발굴하게 된 win-win 협업을 통해, 강성과 내구성, 경제성, 사용성을 모두 잡은 제품을 성공적으로 개발할 수 있었습니다.
포스코는 지난 6월 전남 고흥 국가종합비행성능시험장에서 국내 최초로 스틸 버티포트 공개 성능 검증을 진행했습니다. 포스코는 성능 검증을 위한 스틸 버티포트의 설계부터 시공까지 단 20일 만에 완료해 기술력을 입증했는데요. 쉽지 않은 도전이었지만 개발 과정에서 제작 공장, 시공사와 적극적으로 협의해왔기에 계산된 시간 내에 제작과 시공을 완료할 수 있었습니다. 포스코의 스틸 버티포트는 DfMA*와 모듈화 기술을 접목해 시공 효율성을 강화한 것이 특징입니다. 현장에서 조립이 편리하도록 제품을 최대한 동일한 모듈로 분할 해 공정별 소요 시간을 최소화했는데요. 지금부터 포스코 스틸 버티포트 공개 성능 검증 현장을 만나볼까요?
*DfMA(Design for Manufacture and Assembly) : 건축물이나 구조물 설계 시, 부재·모듈의 제작과 운송, 설치를 사전에 고려하는 기술
5톤에 달하는 헬리콥터가 착륙할 때 실시간 데이터를 계측해 본 결과, 1cm도 변형이 되지 않을 정도로 강재의 튼튼함이 돋보였습니다. 현장에 있던 항공우주연구원, 롯데건설 컨소시엄 관계자들은 향후 UAM 산업에 스틸 버티포트를 적용할 가능성을 언급하며 호평을 보냈습니다. 또, 직접 시험 비행에 참여한 헬리콥터 기장으로부터 기존 헬리패드와 비교했을 때 견고함, 소음, 진동 등에서 차이가 없다는 의견을 받아 다시 한번 스틸 버티포트의 안정성과 우수함을 실감했습니다.
국내뿐만 아니라 국제적으로도 스틸 버티포트의 가능성을 증명할 수 있었는데요. 지난달 열린 2024 WSCE(World Smart City Expo) 버티포트 국제포럼에서 현장 설계 적용 사례를 성공적으로 발표해 포스코의 스틸 버티포트를 전 세계적으로 알린 겁니다. 특히 포스코의 발표가 끝나자, 청중석에서는 상용화 파트너십 문의를 비롯한 다양한 질문 세례가 이어지기도 했습니다. 포럼 후에는 공항공사의 홍보부스에 스틸 버티포트 목업이 전시되어 관람객들의 발길과 이목을 끌었습니다. 이날 전시된 스틸 버티포트 목업은 포스코의 고강도 트러스를 적용한 프레임과 기둥이 결합된 형태의 버티포트 모델로, 구조성능은 물론 건축미와 개방감이 돋보여 큰 관심을 받았습니다.
정부 주도의 실증 사업, 국책 과제 외에도 여러 지자체와 기업이 UAM 시대의 주도권을 잡기 위해 버티포트 건설 계획을 잇달아 발표하고 있습니다. 그중에서도 포스코의 스틸 버티포트는 UAM의 보급과 대중화에 크게 기여할 것으로 기대되고 있는데요. 그동안 버티포트 건설 계획을 발표한 국내 기업은 많았으나 구조 안전성을 객관적으로 증명하고 경제성을 구체적으로 검토한 사례는 포스코의 스틸 버티포트가 국내 최초이기 때문입니다. 포스코는 실현 가능성이 높고, 비교적 가까운 미래에 건설될 것으로 보이는 프로젝트를 중심으로 스틸 버티포트 적용을 추진하고 있는데요. 민간으로서는 최초로 버티포트를 잠실 MICE에 건설할 계획인 ㈜한화 건설부문과의 MOU가 그 대표적인 프로젝트이며, 이외에도 4건 정도의 국내외 버티포트 프로젝트와 협업해 세계 각지에 포스코의 스틸 버티포트를 건설하겠다는 목표입니다. 이번에 내놓은 모델이 프로토타입이었다면 앞으로는 고객별 구체적인 요구사항을 반영한 맞춤형 솔루션을 완성도 높게 개발해 나갈 예정입니다.
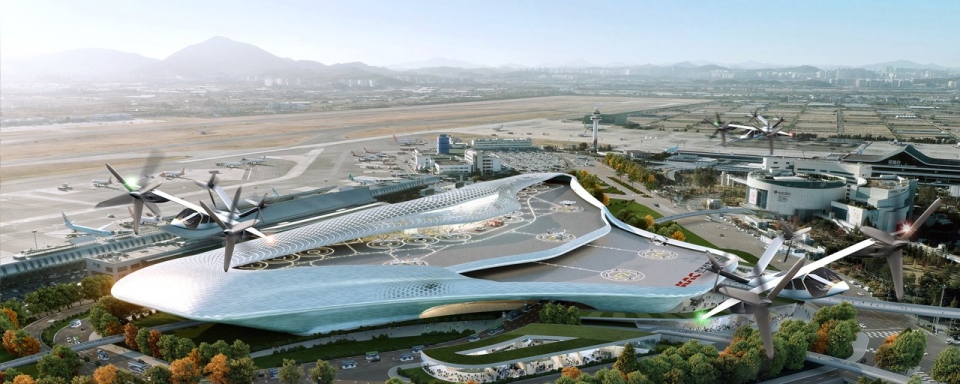
▲대형 UAM 버티포트 개념도 (출처: 한국공항공사)
버티포트도 하나의 건축물이기 때문에 최근 건설업계의 화두인 에너지 효율 향상을 위한 고민이 요구됩니다. 이에 포스코는 이착륙 패드가 옥외에 상시 노출된다는 점을 적극 활용해 태양광 패널을 패드 모듈에 부착하는 방안과 태양광 발전과 터미널의 외장 기능을 겸하는 BIPV* 적용을 검토하고 있습니다. 또 헬리콥터가 하강할 때 강하게 생기는 바람을 말하는 다운 워시(Down Wash)를 활용한 풍력 발전 아이디어 구현도 고려 중입니다. 그밖에 건설 폐기물을 절감할 수 있는 포스코의 고유 솔루션인 재사용 가능 모듈 시스템(RMS, Reusable Module Steel System)을 이용한 터미널 건설 등 다양한 연구를 진행하고 있는데요. 물론 이런 아이디어를 실현하려면 스틸 버티포트의 높은 내구성, 구조적 안전성이 전제돼야 하기에 충분한 시간을 갖고 연구를 해 나갈 계획입니다.
*BIPV(Building Integrated PhotoVoltaic, 건물 일체형 태양광 발전 시스템) : 태양광 모듈을 건축 자재로 활용해 태양광 에너지를 얻을 수 있는 발전 시스템
철강은 재사용이 가능하고 모듈화된 버티포트는 이동·확장·해체가 용이하기 때문에 건설 폐기물을 획기적으로 절감할 수 있습니다. 특히 포스코의 고내식, 고강도 강재와 강구조 기술은 버티포트의 내구성과 안전성, 두 마리 토끼를 모두 잡을 수 있는 건설 재료로, UAM과 버티포트 상용화에 있어 매우 중요한 역할을 할 것으로 기대되는데요. UAM 인프라 구축의 핵심 파트너로 자리매김할 포스코의 스틸 버티포트에 많은 성원 부탁드립니다!
1편 : 지게차 안전 제동 시스템
2편 : 아파트 외벽관리 솔루션 포스-비전
3편 : 인조흑연 음극재 국산화 기술
4편 : 4족 보행 로봇솔루션
5편 : 합성전이보 공법
6편 : 잔선천공기 국산화 기술