특히 전기차 시장의 확대와 함께 차체 경량화가 이슈로 떠오르면서 멀티머티리얼의 적용이 적극적으로 이루어지기 때문이다.
이에 포스코 철강솔루션연구소, 자동차소재연구소, 자동차소재마케팅실은 철강 중심의 멀티머티리얼 제품 기술과
수요 개발에 박차를 가하고 있다. 다가오는 멀티머티리얼 시대를 대비한 포스코의 새로운 도전을 다음과 같이 소개한다.
멀티머티리얼은 소재, 부품 단위에서 이종(異種)소재를 결합하는 것을 의미한다. 이미 존재하는 소재를 재해석하고 연결해 단일 소재에서 확보하기 어려운 최적의 성능을 구현한다. 철강, 비철금속, 플라스틱 등 전통 소재들을 결합해 과거에 없었던 새로운 성능을 발휘할 수 있다.
전통적으로 이종소재는 볼트, 리벳 등을 이용해 기계적으로 결합시켰는데, 중량과 가공비가 증가하는 단점이 있어 최근에는 철, 비철금속에 열과 압력을 가해 접합하거나 새로운 접착제로 붙이는 방식을 사용한다.
최근 다양한 산업에서 △경량화 △제조원가 △안전 △디자인의 강점을 가진 멀티머티리얼에 대한 관심이 높아졌다. 그중 멀티머티리얼을 가장 많이 활용하는 분야는 자동차 부품이며, 전기전자·STS 제품 시장에서도 활발하게 적용하고 있다.
특히 자동차 시장에서 전기차 생산 확대에 따른 차체 경량화 니즈가 계속해서 증가하고 있다. 소비자들이 전기차를 구매할 때 ‘한 번 충전하면 얼마나 멀리 갈 수 있느냐’를 중요하게 생각하기 때문이다. 그래서 자동차 회사는 철강 제품보다 3배가량 비싸지만 가벼운 알루미늄 소재를 사용해 주행거리를 늘리고 있다. 이는 미래 자동차 산업에서 경량 소재들이 철강재를 점차 대체하고 있음을 의미한다.
이렇게 자동차 산업의 패러다임 전환으로 알루미늄 등 경량 소재의 수요가 늘고 있어 철강업계에는 큰 위협으로 떠오르고 있다. 철강기업들도 경쟁 소재와 함께 공존할 수 있는 방법을 찾고 새로운 시장의 수요를 확보해 나가야 한다.
철강재 수요를 지키려면, 고성능 철강재를 공급해 차별화된 경쟁력을 갖추거나 철강에 알루미늄 등 경량 소재를 결합한 멀티머티리얼 제품을 개발하는 것이 필요하다.
이에 포스코 철강솔루션연구소와 자동차소재연구소는 철강 중심의 멀티머티리얼 제품 기술과 솔루션을 개발하고 있다. 이와 함께 자동차소재마케팅실은 시장의 니즈를 바탕으로 고객사에 멀티머티리얼 솔루션 제안과 수요개발을 통해 본격적으로 전기차 시장 성장에 대비하고 있다. 그럼 지금부터 포스코 멀티머티리얼을 보다 상세히 살펴보자.
1) 멀티머티리얼 배터리팩
전기차의 셀-모듈-팩으로 구성된 배터리팩은 단일 부품으로는 가장 무겁고, 차량 성능과 안전성을 좌우하는 핵심 요소이다. ‘가볍게’ 만들어 주행거리를 연장해야 성능을 높일 수 있고 ‘튼튼하게’ 만들어 외부충격의 영향을 최소화해야 안전성을 확보할 수 있다. 때문에 철강, 알루미늄, 플라스틱 등 멀티머티리얼을 가장 많이 적용하는 부품이다.
포스코는 더 가볍고, 더 튼튼한 두 가지 기술적 모순을 풀고자 포스코형 멀티머티리얼 배터리팩을 개발했다. 철강에 알루미늄을 접목해 두 소재가 지니는 장점을 동시에 잡겠다는 컨셉이다.
철강과 알루미늄으로 구성된 포스코형 멀티머티리얼 배터리팩 컨셉은 철강의 강인함과 알루미늄의 가벼움을 결합해 시너지를 극대화했다. 국부적인 충돌에너지는 알루미늄, 전체적인 충돌에너지는 초고강도 철강이 버틸 수 있도록 설계해 기존 철강 배터리팩 대비 중량은 10% 이상, 성능은 20% 내외로 개선했다. 또한 같은 무게의 알루미늄 배터리팩 대비 제조 단가는 20% 이상으로 낮췄다.
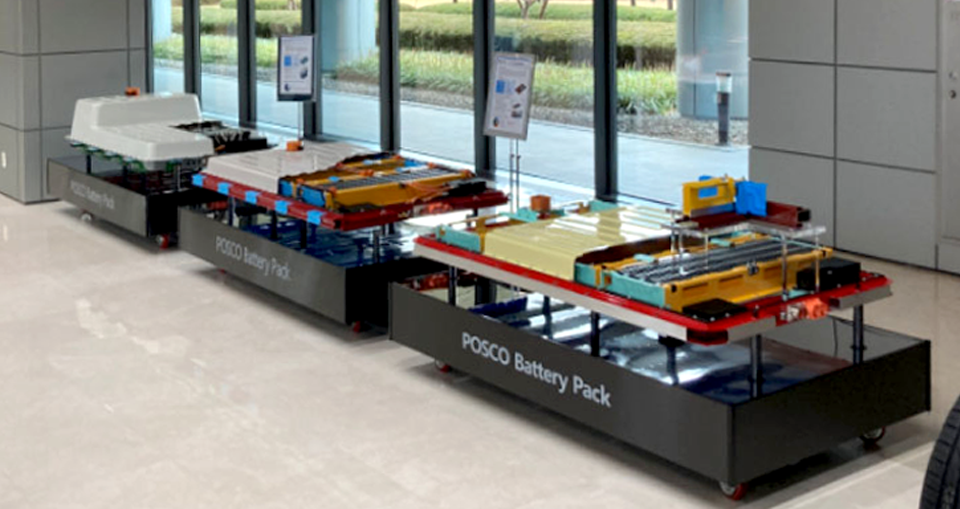
▲ 전기차용 POSCO 배터리팩 컨셉(PBP-EV). 왼쪽부터 1세대 철강컨셉(2018년), 2세대 철강컨셉(2020년), 2.5세대 멀티머티리얼 컨셉(2021년) 모델.
2) 멀티머티리얼 차량용 클로저
최근에는 자동차의 클로저(Closure) 부품(후드, 도어, 트렁크, 테일게이트)의 경량화를 위해 알루미늄 사용이 증가하고 있다.
포스코는 클로저 외판에 알루미늄을, 내판에는 극박 스틸을 적용했다. 이는 알루미늄이 가질 수 없는 스틸의 ‘우수한 성형성’과 ‘원가 경쟁력’을 보완하기 위해서이다. 반면, 스틸과 알루미늄이 직접 닿으면 부식이 발생하기 쉽다. 특히 클로저 부품은 차량 외부에 직접 노출돼 더욱 부식에 취약하다. 이러한 문제를 해결하고자 포스코는 내판에 내부식성이 뛰어난 포스맥(PosMAC) 소재를 적용했다.
3) 멀티머티리얼 복합강판, ‘샌드위치 강판’
샌드위치형 강판은 샌드위치처럼 두 장의 스틸 사이에 다양한 형태의 재료를 넣어 3층 구조를 갖도록 만들었다. 유형별로는 ①제진강판, ②샌드위치 패널, ③샌드위치 강판으로 구분할 수 있다.
현재 포스코는 경량 샌드위치 강판 개발에 박차를 가하고 있다. 위아래에는 스틸을, 중앙에는 플라스틱을 사용해 스틸과 두께가 비슷하면서도 경량 효과를 극대화할 수 있다. 또한 기존 가공법을 그대로 적용하면서 소음과 진동을 저감할 수 있다.
경량 샌드위치 강판은 최적의 저탄소 플라스틱을 선정해, 포스코만의 새로운 코팅 기술로 별도 접착제를 사용하지 않고도 자연스럽게 접착력을 확보했다. 또한 플라스틱 특성과 열융착 기술을 통해 면 접합 방식의 폭 1200㎜ 대면적 샌드위치 강판을 제조할 수 있는 설비를 도입해 부품화하는 한편, 적용 가능한 사이즈의 시제품을 제작할 계획이다.
이러한 강점을 지닌 샌드위치 강판을 포스코가 개발한 차체의 31개 스틸 부품에 적용한 결과, 34%의 경량화 효과가 있음을 확인할 수 있었다.
4) 멀티머티리얼 이종접합과 부방식 기술
[이종접합 기술]
이종소재 간 접합은 소재 특성 차이로 Spot·Arc 용접 등 기존 방식으로 접합이 어려워 일반적으로 SPR(Self-Piercing Rivet), FDS(Flow Drilling Screw)와 같은 기계적 접합 기술을 적용하고 있다. 하지만 기계적 접합 기술은 설비투자, 중량 증가, 구조적 제약이라는 문제가 있다.
이를 해결하고자 Spot 용접과 같은 기존 방식을 그대로 활용하는 용융접합기술과 1.5GPa 급 초고강도강에 대한 기계적 접합 기술을 개발해 국내 자동차사와 성능평가를 했다. 이를 통해 양산 중인 일반적 접합 기술과 동등 수준의 강성을 확인할 수 있었다.
또한 전기차 배터리팩의 냉각판을 기존의 Al-Al 단일조합에서 Al-STS 이종조합으로 대체하는 이종소재 Brazing 접합기술을 고객사와 함께 개발하고 있다.
[부방식 기술]
멀티머티리얼 접합부에서는 두 소재 사이에 발생하는 ‘갈바닉 부식’*과 좁은 틈 사이에서 발생하는 ‘틈 부식’이 복합적으로 일어난다. 연구소는 다양한 강판들의 접합부 부식 시험을 실시해 포스맥(PosMAC) 1.5 강판이 알루미늄과 접합할 때 갈바닉 부식을 저감할 수 있는 가장 효과적인 소재임을 확인했다. 또한 틈으로 수분과 부식성 물질 유입을 방지하는 기능을 첨가한 멀티머티리얼 전용 접착소재를 전문 업체와 함께 개발 중이다.
*갈바닉 부식 : 이종금속이 접촉되어 전위차가 있을 때 전자의 이동으로 발생하는 부식
멀티머티리얼 전략의 시대는 이미 시작됐다. 일본, 독일 등 주요 제조업 강국은 최근 새로운 소재의 발견보다 철강 등 전통 소재의 가치를 인정하고, 수요에 기반한 멀티머티리얼 기술을 개발하는 산업을 육성하고 있다. 특히 자동차, 전기전자 등 핵심 산업에서 멀티머티리얼 소재에 대한 수요가 점차 늘고 있어 소재기업들은 독보적인 기술력과 차별화된 솔루션으로 시장을 선점해야 미래 경쟁력을 확보할 수 있을 것이다.
포스코는 철강 베이스의 멀티머티리얼 기술과 솔루션을 끊임없이 개발하여, 소재 기업으로서 강인한 리더십을 지속적으로 유지하고 멀티머티리얼 시장을 향해 전진해 나갈 계획이다.
※이 콘텐츠는 포스코그룹 통합 소통채널 ‘포스코투데이’를 토대로 제작했습니다.