포스코는 1968년 산업화라는 국가적 사명을 안고 출범한 이래, 국가 경제 발전에 이바지하고, 지역사회와의 동반성장 활동을 지속 펼쳐왔다. 2013년부터는 중소 협력기업들의 역량 향상을 지원하고자 포스코型 생산성 혁신 프로그램을 운영해 지역 중소기업의 경영•제조혁신•공정개선 등 생산성 향상과 안전한 일터 조성을 돕고 있다.
포스코型 생산성 혁신은 포스코그룹 대표 동반성장 프로그램 중 하나이다. 포스코 고유의 제조혁신기법인 QSS(Quick Six Sigma)를 통해 임직원의 혁신 마인드를 함양하는 등 체질개선에 중점을 둔 스마트화 역량강화 컨설팅과 설비 및 시스템 구축을 지원하는 스마트공장 구축 지원 활동이 있다.
포스코는 2019년부터 2023년까지 5년간 총 200억 원을 출연해 생산성 혁신 프로그램을 운영하며 다양한 산업군에서 중소기업의 혁신과 성장을 지원해 오고 있다. 포스코가 펼쳐온 포스코型 생산성 혁신 활동을 조금 더 자세히 살펴보자.
스마트화 역량강화 컨설팅은 스마트공장 구축에 앞서 일하는 방식의 변화를 돕는 프로그램으로 전담 컨설턴트가 주 1회 컨설팅 대상 기업을 방문해 △작업환경 개선 △임직원 혁신 마인드 고취 △설비관리 능력 향상 △안전사고 예방 △에너지 관리 △생산성 및 품질관리 등 계층별 교육을 통해 기업이 자체적으로 혁신 역량을 확보할 수 있도록 지원한다.
특히, 최근에는 ESG 경영이 중요해짐에 따라 희망하는 기업을 대상으로 에너지 저감 컨설팅도 실시 중이다. 기업별 맞춤형으로 계약 전력, 선택요금제 분석과 변경 등 전기 사용법 관련 컨설팅을 하고, 보일러 열처리 및 래들 건조 방법 개선 등 설비 관련 열효율을 높이기 위한 활동을 실시한 결과, 2020년 컨설팅을 받은 기업 35개사는 연간 5억 9,800만 원, 기업당 평균 1,700만 원의 에너지 비용을 절감할 수 있었다. 이는 탄소배출량으로 환산 시 연간 무려 1,590톤의 CO2를 감소한 것과 같은 효과이다.
고객사 화신하이스틸은 2020년 5월, 에너지 사용현황 진단과 사용 효율화에 대한 컨설팅을 받았다. 컨설팅 결과, 피크전력 절감과 공기압축기 고효율화 그리고 기존 높은 전력량으로 체결했던 계약전력을 낮은 전력으로 분할해 계약하는 모자(母子)분리 방법을 통해 에너지 효율을 높여 연평균 2,600만 원을 절감했다.
또 다른 고객사인 원하이텍도 에너지 컨설팅을 통해 에너지 효율을 높였다. 에너지 사용을 최적화해 계약전력을 1,900㎾에서 1,100㎾로 변경하고, 공기압축기 설비 진단을 통해 누출(leak)을 점검하고 노즐 등을 개선함으로써 연평균 3,300만 원을 절감했다.
스마트화 역량강화 컨설팅 단계에서 체질을 개선했다면, 스마트공장 구축 지원 단계에서는 본격적으로 스마트공장 구축에 나선다. 포스코그룹의 전문가들이 중소기업의 스마트화 수준과 경영 환경에 따라 스마트센서, 무인재고 시스템, MES 등 다양한 스마트시스템 도입을 맞춤 지원한다. 비용은 포스코와 정부가 각각 30%, 중소기업이 40%를, 사업비가 2,000만 원 이하일 경우에는 중소기업 부담 없이 전액 포스코와 정부가 부담한다.
선박용 LNG탱크를 제작하는 고객사 이영산업기계는 탱크 내부 품질관리에 어려움을 겪고 있었다. 온도와 습도를 측정하는 시스템이 없어 작업자가 직접 상태를 측정하다 보니 부정확한 측정 결과로 인해 생산이 지연되는 일이 있었다. 또 작업자가 탱크 내부로 들어가 직접 제품 상태를 점검해야 했기에 밀폐공간인 탱크에서 질식과 같은 안전사고가 발생할 위험성도 높았다. 포스코는 이를 해결하고자 사물인터넷 기반 자동감시 시스템 구축을 지원했다.
이영산업기계는 자동감시 시스템 구축의 일환으로 탱크에 설치한 스마트센서 덕분에 각종 데이터를 실시간으로 모니터링할 수 있게 됐다. 그 결과, 생산 품질을 일정하게 유지할 수 있게 됐고 덕분에 납기도 기존대비 8.3%가량 단축했다. 또한, 탱크 내부 가스를 감지하고 그 정보를 무선으로 전송할 수 있게 됨에 따라 작업자의 안전사고 위험성도 크게 낮췄다.
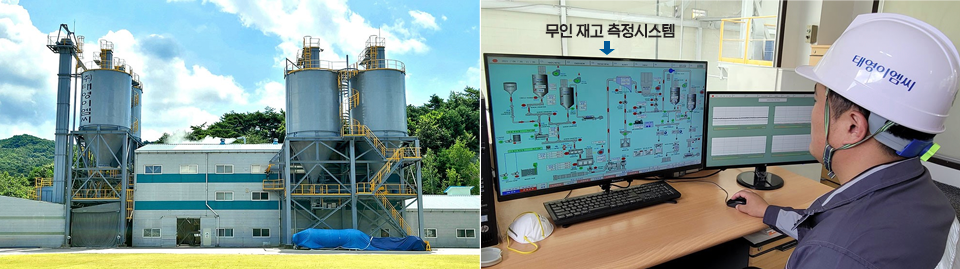
▲석회석 원석과 제품을 저장하는 태영EMC의 사일로와 무인 재고 측정시스템을 활용해 업무 중인 태영EMC 직원.
태영EMC도 스마트공장 구축지원을 통해 생산성 향상과 안전이라는 두 마리 토끼를 잡은 사례이다. 태영EMC는 포스코에 석회석, 생석회를 공급하는 회사인데 석회석 원석 및 제품 등을 저장하는 사일로(silo) 내부에 쌓인 재고를 측정하는 시스템이 없었다. 이 때문에 직원들은 재고 파악을 위해 매일 약 20m 높이의 사일로 정상부를 직접 오르내리고 있었다. 직원들은 안전 위험에 노출돼 있었고, 수작업에 의한 재고 파악은 부정확한 데이터 산출의 원인이 돼 의사결정에 혼선을 불러일으켰다.
이에 포스코는 태영EMC에 재고 자동계측 및 실시간 데이터 전송이 가능한 무인 재고 측정시스템을 구축했다. 시스템 구축 이후 작업자가 직접 사일로를 오르내릴 필요가 없어져 안전사고의 위험성이 줄었다. 정확한 측정값을 산출하니 신속하고 정확한 의사결정도 가능해졌다.
또, 원재료와 제품 재고 부족으로 인한 생산, 출하 지연을 방지하는 효과가 있었고 직원들이 사일로 저장량을 모바일로 조회할 수 있게 돼 업무처리가 신속해졌다.
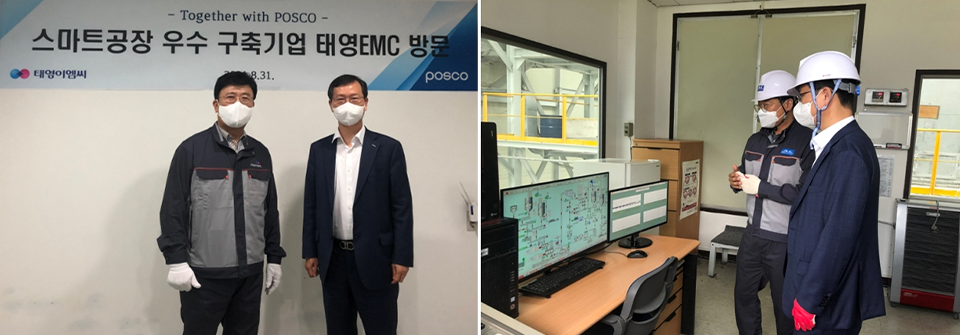
▲이주태 구매투자본부장(오른쪽)이 8월 31일 태영EMC를 방문, 김재성 대표의 안내로 스마트공장 구축 현황을 살펴보고 있다. 이주태 구매투자본부장은 “포스코는 앞으로도 파트너사가 안전한 작업장 구현, 에너지 저감 등 무형의 가치를 지켜낼 수 있도록 적극 지원할 예정이다”고 말했다.
중소기업의 혁신성장과 ESG 가치 전파에 앞장설 예정이다.
※이 콘텐츠는 포스코그룹 통합 소통채널 ‘포스코투데이’ 기사를 토대로 제작했습니다.