포스코그룹은 안전과 탄소저감 실천에 기여하는 기술을 개발하고자 최선을 다하고 있습니다. 더 나은 사회를 만들어가는 포스코그룹의 우수한 신기술을 소개합니다. 포스코그룹 신기술에 대한 수다를 계속 이어가는 기술+잇+수다, 지금 시작합니다!
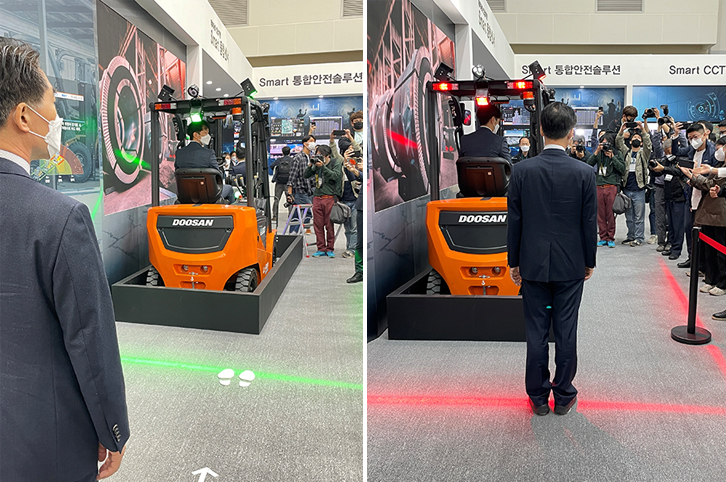
▲2022년 대한민국 안전산업 박람회에서 포스코 전시부스를 방문해 ‘지게차 안전 제동 시스템’을 시연하는 김성호 행정안전부 재난안전관리본부장.
2022년 대한민국 안전산업 박람회(K-SAFETY EXPO)에서 포스코의 기술이 행정안전부 장관상을 수상하며 우수함을 인정받았습니다. 장관상을 받은 포스코그룹의 <지게차 안전 제동 시스템>은 인공지능(AI)을 활용한 영상 인식 기술* 기반 감지•경고 시스템과 자동 정지 제어 기술** 기반 속도 제어 시스템을 접목한 기술입니다.
<지게차 안전제동 AI시스템>은 영상인식 기술과 자동정지 속도제어 기술 등이 적용돼 충돌에 따른 재해를 원천적으로 예방할 수 있습니다. 지게차가 주변 작업자에게 접근하면 운전자가 브레이크를 밟지 않아도 지게차가 단계적으로 자동 정지하기 때문인데요. 충돌 위험 거리가 6m이내라면 1단계로 알람이 울리고, 4m 지점에서는 2단계로 감속이 시작되며, 작업자가 2m 이내로 접근하면 3단계로 지게차가 자동으로 멈춥니다. 운전자 또는 작업자가 스스로 주변을 인식하지 못하고 있는 상황에서 갑작스러운 돌발사태가 발생하면 지게차 속도를 자동으로 제어해 사고를 막는 것이죠.
* 영상 인식 기술 : AI•딥러닝 기술이 적용된 영상으로 사람과 사물을 구분해 인식하고 지게차에 설치된 광각렌즈로 촬영한 영상을 좌표계로 변환해 지게차와 사람간의 정확한 거리 값을 제공하는 기술. 기존 기술과는 달리 지게차와 작업자에 별도의 태그 부착 없이도 충돌의 위험을 손쉽게 인지.
** 자동 정지 제어 : 사람이 지게차에 근접하면 운전자가 브레이크를 밟지 않아도 자동으로 지게차가 정지하는 기술.
고용노동부에서 공개한 산업재해 고위험요인(SIF)* 분석정보를 살펴보면 최근 6년간 사고사망 사례는 4,432건에 달합니다. 이 중 고용노동부에서 선정한 제조업 12대 사망사고 기인물**에 의한 사고사망 사례는 전체 632건이며 지게차에 의한 사고사망 사례는 124건으로 약 20%에 달해 전체 1위를 차지할 정도로 위험성이 큽니다. 고용노동부는 고위험사업장을 불시에 현장 점검•감독을 하며 차량•기계 등 작업에 의한 사고 위험을 집중 점검하고, “스마트 안전장비를 활발히 도입해 활용하기 바란다.”라고 강조했습니다.
*SIF(고위험 요인, Serious injury & fatality) : 사망 또는 정상적인 생활에 치명적인 지장을 초래할 수 있는 고위험작업•상황 및 재해유발요인.
**12대 사망사고 기인물 : 지게차, 크레인, 컨베이어, 지붕•대들보, 사다리, 혼합기, 굴착기, 화물운반트럭, 줄걸이기구, 산업용로봇, 분쇄•파쇄기, 사출성형기.
일반적으로 지게차에 적용된 안전기술은 충돌 위험 시 운전자에게 경고 알림을 보내는 정도에 그칩니다. 따라서 소음이 심한 작업장에서는 인지하기 어려워 원천적인 재해예방에 한계가 있죠. 고용노동부에선 중대재해 감축 로드맵에 따라 <스마트 안전장비 지원사업>을 추진해 국내 산업계의 지게차 재해를 예방하고 있지만 별도의 태그 부착한 작업자만 감지하는 등 기술적 한계도 있습니다. 작업자를 감지하더라도 관성에 의한 정지거리 불균일, 경사로에서의 밀림 등으로 2차 사고 위험성이 항상 존재합니다.
포스코는 지게차 사고의 심각성과 기존 안전 기술의 한계를 인식하고 우리 사회가 직면한 안전문제 해결에 동참해 기업시민 경영이념을 실천하고자 지게차 안전 제동 시스템 개발에 착수했습니다.
2021년 11월, RIST와 지역 중소기업이 함께 만든 태스크포스(TF)가 <지게차 안전 제동 시스템>개발에 착수했고, 2022년 5월에 개발을 마쳤습니다. 기술개발이 완료된 후 포스코 안전기획실과 포스코DX가 상호 협업해 제철소 현장에 시범적용을 추진했습니다. 포스코DX는 스마트 팩토리 플랫폼(PosFrame), 스마트 예정정비시스템(PIMS), 빅데이터와 AI 기술을 활용한 공정자동화 등 포스코그룹의 스마트와 자동화 기술을 선도하는 그룹사입니다.
2023년 4월부터는 제철소 현장에 해당 기술을 적용하는 실증테스트를 시작했습니다. 포스코그룹의 스마트기술 전문업체인 포스코DX와 모터, 원동기 전문인 지역 중소기업 ㈜태양전기가 함께 기술개발에 착수했는데요. 제철소 작업환경과 지게차 브랜드를 다양화해 포항제철소 압연공정과 선강공정 각 두 곳씩 총 네 곳을 선정해 실증 테스트에 들어갔습니다.
2024년 5월에는 포스코 안전기획실과 포스코DX가 다양한 작업환경의 특성을 고려해 포항제철소 직영 ‘3FINEX 정비섹션’, 그룹사 ‘포스코엠텍’, 협력사 ‘영남산업’과 ‘대명’의 지게차를 각각 한대씩 선정하고 현장 시범 적용을 추진했습니다. 지게차 자동제어 현장 시범적용 계획을 수립하고, 포스코DX와 협업해 8월 완료를 목표로 본격적인 적용에 들어갔습니다.
하지만 기술적 난관이 많아 일정이 수 차례 미뤄지기도 했습니다. 공장 내 조명에 따라 AI 카메라 사람 인식률이 낮아지거나, 지게차 제조사와 모델이 현대, 두산, 클라크 등 9종으로 회로 구성이 각자 달라 모델별 제어모델을 맞춤형으로 개발하는 것도 어려웠습니다. 또, ECU를 직접 프로그래밍하면 오류가 생기거나 추후 지게차 수리가 어려워지는 점, 현장 작업자가 지게차의 자동제어 시스템 관련 부가적 장치들로 활용에 불편을 느낀다는 점도 문제였습니다. 그렇다면 이런 문제들은 어떻게 개선했을까요?
포스코는 현장에서 지게차를 사용하는 직원들과 함께 개선사항을 파악하고 포스코DX와 함께 기술 보완에 들어갔습니다. 태양전기(AI카메라)와 에프에이이(LiDAR센서)의 기술을 적용한 지게차를 2전기강판공장과 1냉연공장에 각각 설치해 다양한 센서간 성능을 비교했고, 태양전기는 별도의 연구팀을 구성해 AI 카메라의 인식률을 높였습니다. 또, 다양한 지게차 기종으로 충분한 테스트를 거쳐 제조사별 자동 제어를 구성하는 핵심 장치를 맞춤으로 제작했습니다. ‘ECU 프로그래밍 배제, 제조사 수리 서비스 무조건 가능’이라는 조건을 충족하며 전체 시스템 구조를 변경했습니다. 철저한 현장 사전 답사로 운전자의 작업환경과 편의를 고려하고, 부서별로 희망 감지거리를 미리 조사해 설치 시 반영하는 방식으로 활용 편의성도 대폭 개선했습니다. 잘 보이는 경보기를 설치하고 제동시스템 일시 해제 버튼을 탑재하는 등 현장 작업자들의 편의도 챙겼습니다. 이렇듯 꼼꼼한 사전조사를 바탕으로 개선한 포스코그룹의 스마트안전기술 <지게차 안전 제동 시스템>이 11월 현장에서 활약을 시작했습니다.
물론 고온이나 분진 등 제철소의 특수한 환경에서 일어날 수 있는 카메라의 정확성과 신뢰도 문제, 승하차 시 운전자의 신체와 접촉하면서 일어나는 구성품 손상 문제, 제조물 책임법 문제 등 여전히 보완할 부분들이 있습니다. 포스코그룹은 앞으로도 개선점을 발굴해 포스코 작업환경에 적합한 지게차 자동제어 시스템을 완성할 예정입니다.
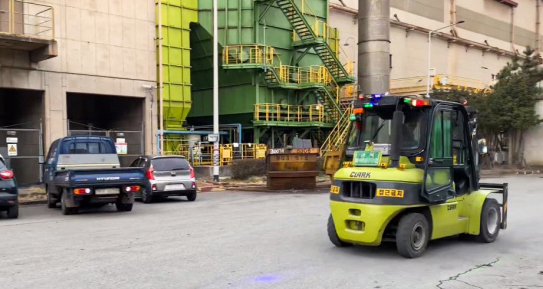
▲ ‘지게차 안전제동 AI 시스템’ 적용 실물 사진.
<지게차 안전 제동 시스템>은 작업자의 부딪힘, 깔림 위험을 원천적으로 예방하고자 개발한 기술이지만, 제어까지 조정하기 때문에 순간의 기술적 오류로 2차적 사고가 발생할 수 있습니다. 향상된 카메라의 인식률 역시 97% 수준으로 100%에 미치지 못하기 때문에 완벽한 자동화 기술이라고 볼 수는 없는데요.
앞으로 포스코그룹은 <지게차 자동제어 시스템>의 2차 사고와 리스크를 법률적으로 검토하고, 지속적으로 카메라 인식률을 높여가면서 유지•보수 지원체계를 정립할 예정입니다. 앞으로 포스코는 ‘지게차 안전 제동 시스템’을 포스코그룹 전사에 확산 운영해 차량•기계로 인한 사고를 저감하고자 노력할 것입니다.