조선소에 다녀온 적이 있다. 야드 곳곳을 차지하고 있는 선박 블록들. 멀리서 바라본 선박 구조물들이 마치 레고(Lego) 장난감처럼 보였다.
조선소는 거대한 선박을 건조할 때 선체를 300여 개 부분(이를 “블록”이라고 한다)으로 나눠, 그 블록을 먼저 만든 후 이들 블록을 도크(Dock)에서 결합하여 최종적으로 완성한다. 선박 건조가 레고 조립과 다른 점은 소재인 후판(厚板, 일반적으로 두께가 6㎜ 이상인 스틸 판재)이라 불리는 강판을 이어붙이는 과정에서 “용접”이 필요하다는 것. 그래서 선박 건조 과정은 곧 용접 과정이다.
그러고 보면 이 세상 단일 구조물 기준 스틸 소재가 가장 많이 소요되는 게 선박이고, 형체를 만들기 위해 가장 많은 “용접”을 필요로 하는 구조물 또한 선박이다. 그래서 선박을 건조할 때 “스틸 소재”와 “용접”은 옷을 만들 때 헝겊과 바느질 작업처럼 밀접하다.
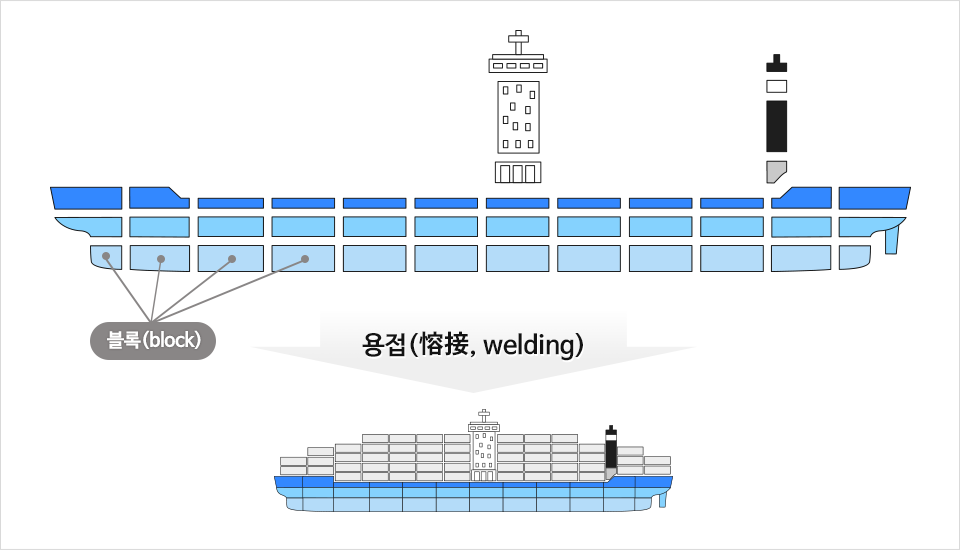
▲ 300여개 개별 블록들은 용접을 통해 선박으로 탄생한다. 이 개별 블록도 용접의 산물이다.
l 선박은 “강판”을 “용접”으로 기워 만든다
2010년 무렵부터 시작된 조선업 불황 속에 국내 조선사들은 고도의 건조기술을 필요로 하는 선박, 가령 ‘초대형 컨테이너 선박’이나 ‘LNG 수송선’ 등을 수주하는데 주력하고 있다.
선박의 규모를 대형화하거나, LNG 추진선 같은 특수선을 건조한다는 것은 그 선박의 설계·건조 상의 난이도와 구조적 복잡성이 커지는 것인 만큼 소재로 쓰이는 강재의 재료적 특성 또한 차별화되어야 하고, 또 이를 효율적으로 재단, 용접하는 기술이 동시에 뒷받침되어야 한다는 것을 전제로 한다.
“두꺼운 판재들을 유기적으로 접합하는 용접공정은 상상하는 것 이상으로 예민하고 전문적인 작업입니다. 사용되는 철강재의 특성과 그에 맞는 용접재료의 개발, 용접조건 등이 최적화되지 못하면 용접부에 결함이 발생하게 되어 선체의 안정성 확보가 불가능하게 됩니다”. 철강솔루션연구소 접합연구그룹 정보영 수석연구원의 말이다.
포스코 철강솔루션연구소에는 선박용 강재를 개발하고 이 강재의 용접 솔루션을 개발하는 전문가 집단이 따로 있다. 선박 건조 시 가장 많은 비용과 공수가 들어가는 부분이 “용접”이며, 선박의 안정성을 담보하는 중요한 공정도 “용접”이기 때문.
국내 조선사들이 글로벌 특화된 경쟁력을 보유할 수 있도록 선박 건조의 안전성과 생산성 양면에서 치열하게 고민하는 포스코의 솔루션을 소개한다.
#1 ‘초대형 컨테이너 선박’의 선체 안전성·생산성 강화 솔루션
컨테이너선은 화물을 많이 적재해야 하기 때문에 윗부분이 개방되어 있다. 때문에 선체 구조의 불안정성이 발생할 수 있는데 이를 보완하기 위해 하부에서 상갑판부(Upper deck)로 갈수록 두껍고 강한 강재를 사용한다.
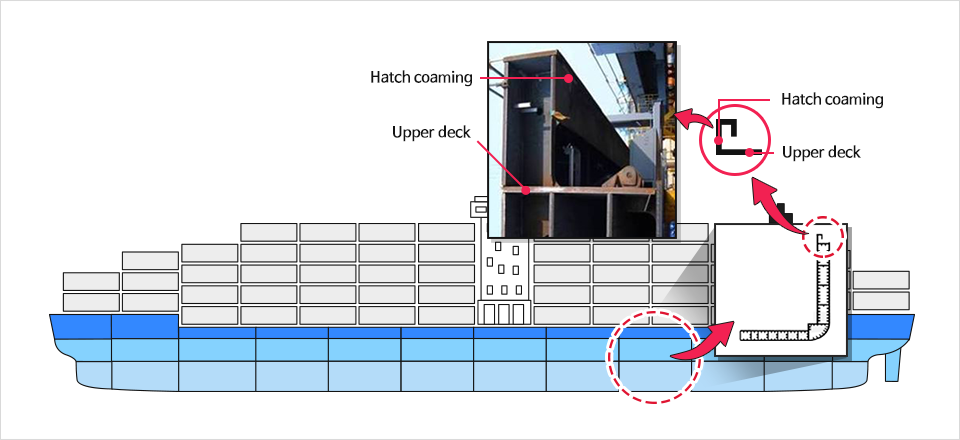
▲ Upper deck는 선박의 최상층에 위치한 갑판을 말하며, Hatch coaming은 해수로부터의 화물손상 방지를 위해 설치된 구조물을 의미함. 초대형 컨테이너 선박의 Uppe deck와 Hatch coaming부분은 안전성 확보를 위해 가장 강한 스틸 소재가 사용된다
국제 선급협회*는 대형 컨테이너선박 제작 규정을 제정하면서, 일본에서 주로 사용하는 계단형 용접법과 한국에서 사용하는 직선형 용접법을 등록했다. 일본 업체들은 계단형 용접법이 용접부에서 균열이 발생하면 선체 전체로 확산되지 않기 때문에 안정성이 높다고 주장했다.
*국제선급협회: 각국의 선급협회들이 선급 간의 협력 및 규칙의 통일을 도모하기 위하여 조직한 모임으로, 조선사들은 국제선급협회에 등록되어 있는 규격·규정에 따라 선박을 제조해야만 한다.
이에 반해 국내 조선사들은 블록을 한 줄로 용접하는 직선형 용접법을 사용해왔는데, 일본 업체들은 한국 방식이 용접부를 옮겨가야 하는 계단식에 비해서 생산성은 좋지만, 선박이 대형화되면 용접부 균열 발생 시 용접선을 따라 선체 전체로 진행될 수 있다고 우려했다.
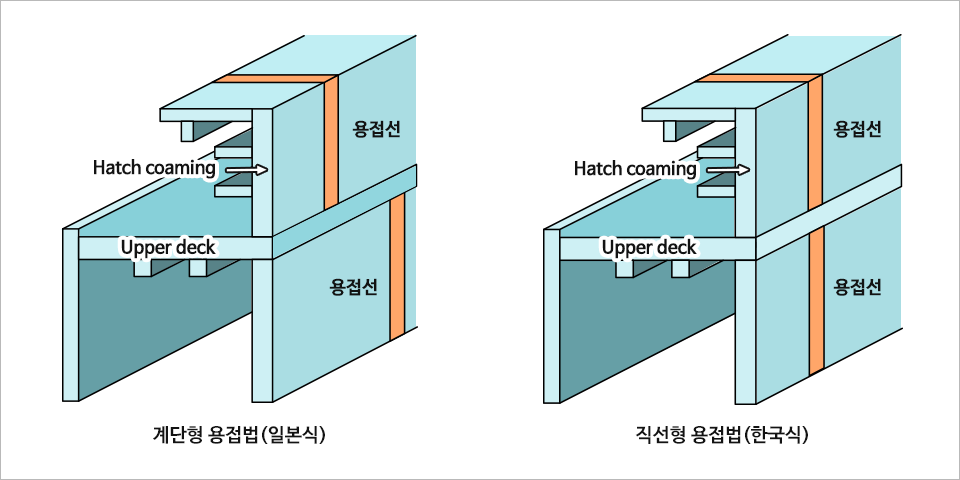
▲ 후판 용접 방식 비교
결국, 한국식 용접방식의 안정성 입증이 필요했는데, 포스코 철강솔루션연구소가 상갑판부(Upper deck) 용접부 끝부분에 구멍을 뚫거나(Arrest hole) 인성이 높은 용접재료(또는 강재)를 삽입/용접(Arrest insert/Arrest Weld)해서 용접부 균열 확산을 막는 방법을 개발해냈다. 그리고 조선사를 대신해 국제선급협회의 협의회 활동을 적극적으로 펼친 결과, 직선형 용접 방식 또한 안정성을 인정받았다. 국내에서 생산되는 대부분의 컨테이너선박은 직선 용접 방식을 활용해 건조되고 있다.
선박 건조상의 안전성도 입증됐고, 조선사의 생산성도 항상된 일석이조의 솔루션!
#2 일주일 걸리던 용접작업을 하루 만에 – 조선사 생산성 향상 지원
일반적으로 후판을 접합하여 선박을 제조할 때는 뜨개질을 하듯이 한 땀 한 땀 이어가는 다층용접 방식을 사용하기 때문에 시간과 인력이 많이 소요된다. 용접에 소요되는 시간을 최대한 줄이는 것이 중요한 생산성 향상 포인트. 조선소에서는 선박 건조 상의 중요 공정인 용접 생산성을 획기적으로 향상시킬 방안을 모색했다. 그래서 철강솔루션연구소가 찾아낸 방안이 대입열용접법(大入熱熔接, Electro-gas welding)이다.
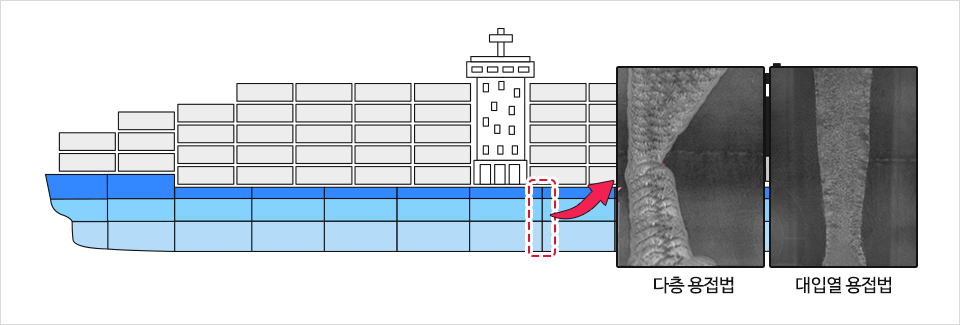
▲ 다층용접과 대입열용접의 용접부 비교
대입열용접법은 아크(arc)를 하나씩 쌓아가며 용접하는 일반적인 방법과 달리 한 번에 용접부 전체를 단층으로 용접하는 방법이다. 하지만, 한 번에 높은 열을 쏟아붓기 때문에 용접부의 물리적 성질이 나빠질 수 있다. 이 문제를 해결하기 위해 포스코 기술연구원의 강재연구소는 대입열을 적용해도 용접부 물성을 만족시킬 수 있는 대입열강재를 별도로 개발했으며, 철강솔루션연구소는 최적의 용접 조건을 찾아냈다.
조선소에서는 대입열용접 솔루션을 사용해 일주일이 소요되던 작업시간을 단 8시간으로 단축, 생산성 향상에 큰 성과를 얻을 수 있게 됐다. 대입열강재와 용접 솔루션은 ’08~’15년에 걸쳐 D조선사에 공급되었고, ’18년부터는 S조선사에 공급되는 등 조선사에서 활발히 활용되고 있다.
거대한 선박의 강철 표면에는 이음부에 가해진 용접의 흔적들이 발견된다. 그 흔적들은 선박이라는 거대한 철강 소재의 완성체가 갖는 영광의 상처다. 이 상처가 없었다면 거대한 블록 조각들에 불과했을 테니.
그리고 그 안에는 포스코 철강솔루션연구소의 고민과 노력이 녹아들어 있다. 포스코는 철강회사지만 철강제품만을 판매하지 않는다.