포스코의 차별화된 기술력으로 탄생시킨 고부가가치 강재 WTP(World Top Premium). 과연 고객에게 WTP는 어떤 솔루션이 되고 있을까? 포스코 마케터들이 솔루션 마케팅을 펼치고 있는 고객사 현장을 직접 찾아 이야기를 들어봤다.
l 치열한 친환경 자동차 시대, 기가스틸로 고객의 경쟁력 확보
포스코 고객사 아산은 자동차 섀시를 생산하는 중견 부품사다. 2000년 경기도 김포에 설립 후, 계속 사업을 확장하여 현재는 발안, 부산, 광주에도 공장을 두고 화성에는 연구소를, 중국에도 합작 공장을 갖고 있다. 자동차 시장 불황기에도 매년 매출액을 700억 원 이상 유지해온 탄탄한 기업이다.
아산은 포스코로부터 띠강(테이프처럼 폭이 좁은 강판, 대강(帶綱) 또는 Skelp)을 구매해 각종 자동차 부품들을 생산하고 있다. 주요 생산부품은 자동차 앞 부분에서 충격을 흡수하는 범퍼 속에 들어가는 빔(Bumper Beam)을 비롯해, 옆면의 충격을 분산, 흡수하는 도어 섀시(Door Chassis), 임팩트 빔(Impact Beam), 사이드 실(Side Sill) 등이다. 모두 차체를 구성하면서 형태를 잡아주고, 운전자를 보호하는 기능을 한다.
아산 공장에서는 롤 포밍(Roll Forming) 설비에서 자동차 부품들이 쉬지 않고 쏟아져 나오고 있었다. 롤 포밍은 자동차에 필요한 형상을 연속 압연롤을 통해 생산하는 최신 성형 설비다. 대강을 풀어 차 부품을 꽂을 구멍을 먼저 뚫은 후 롤 압연을 통과하면서 필요한 모양으로 성형을 한 다음 자른다. 같은 형상의 부품을 연속적으로 만들기 때문에 생산성이 좋다. 아산의 앞선 기술력이 돋보이는 대목이었다. 포스코의 고급 소재가 이 최신설비를 만나 다양한 부품으로 변신 중이었는데, 이 만남은 꽤 오래전부터 준비되어 왔다고 한다.
‘친환경’이라는 키워드가 자동차 업계에서도 중요해지면서, 차체의 경량화가 화두로 떠올랐다. 아산에게도 중요한 이슈였다. ‘더 단단하면서도 더 가벼운 부품을 만들어 내는 것.’ 아산과 포스코는 2010년부터 이 과제를 함께 고민해왔다. 포스코는 2015년 기가스틸 개발에 박차를 가해 포작년 초 MART(MARTensite)강 개발에 성공해 테스트를 마치고 양산에 돌입했다. 아산은 현재 MART강을 구입해 사용하고 있다. MART강은 마르텐사이트(Martensite)라는 조직 형태를 가져 150kg 이상의 하중도 충분히 견딜 수 있다. 포스코가 역점을 두는 대표적인 기가스틸 중 하나다. MART강 적용으로 아산은 시장에서 원하는 차체 경량화에 적합한 부품 생산이 가능해졌다.
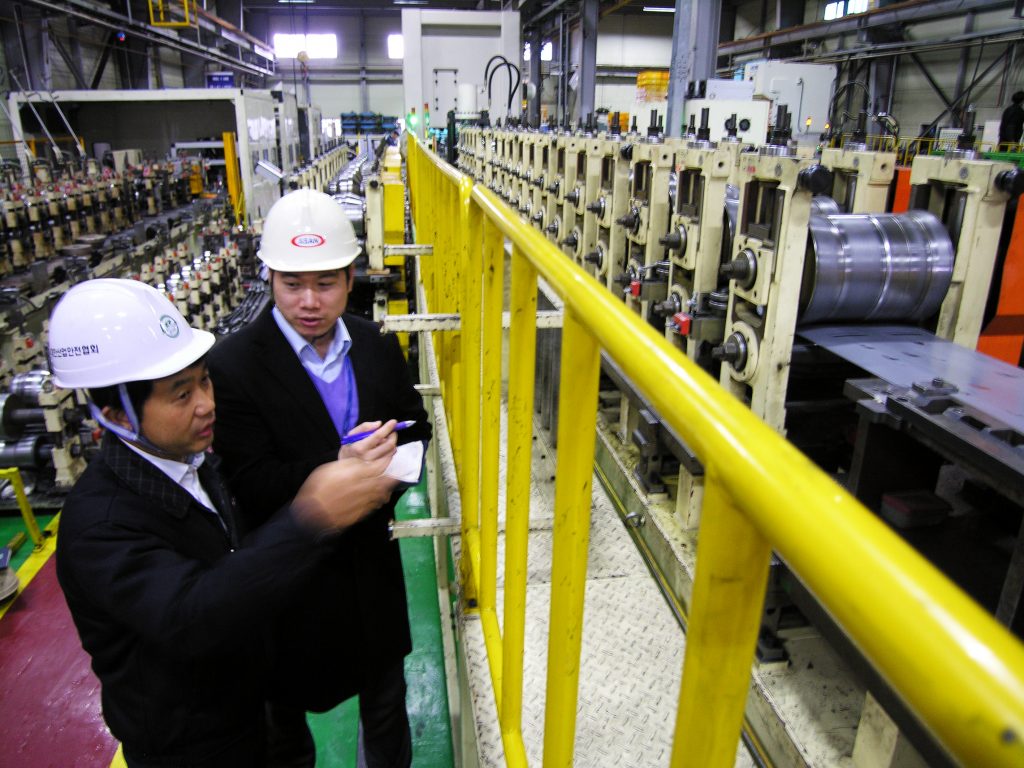
▲ 포스코 자동차소재마케팅실 하승호 과장(오른쪽)과 아산 김근호 부장이 롤 포밍 설비에서 포스코 WTP로 생산하는 차 부품의 품질에 대해 얘기를 나누고 있다.
아산을 담당하고 있는 포스코 자동차소재마케팅실 하승호 과장은 “MART강 같은 경우 내연기관차뿐 아니라 친환경차인 전기차의 부품에도 적용하는 것을 목표로 수요처 개발에 집중하고 있다”라고 말했다. 더 나아가 포스코는 친환경차에 일종의 토털패키지 정책을 추진하고 있다. 차체, 섀시, 모터, 배터리팩 등 부분별로 판매하기보다 패키지로 묶어 토털마케팅을 펼치고 있다. 설계부터 생산, 부품제작에 이르기까지 포스코의 역량을 공유하면서 마케팅으로 연결한다는 구상이다.
l 콘크리트면 된다고? 포스코 WTP로 바꿔보니…
첨단 자동차뿐 아니다. 건설산업계에도 포스코 WTP를 적극 적용하고 있다. 포스코건설이 모산•영신지구에 지제 지역주택조합이 발주한 아파트 대단지를 짓고 있는 현장을 찾아봤다.
포스코건설 유윤종 소장과 NI스틸 홍순호 부장, 포스코 강건재마케팅실 고광호 과장과 함께 지하 주차장으로 내려갔다. 천장 부분이 일반 콘크리트가 아닌 ‘세로 ㄹ’형 데크로 시공돼 있었다. 고광호 과장은 “이 데크는 자동차 또는 건물 외장재용 용융아연도금강판(GI-ACE)으로 만들었다. 일반 소재에 비해 제작하기 쉽고 수명이 긴 것이 특징이다. 또한 무엇보다 표면이 미려하다. 이것도 포스코 WTP 제품이다.”라고 알려줬다.
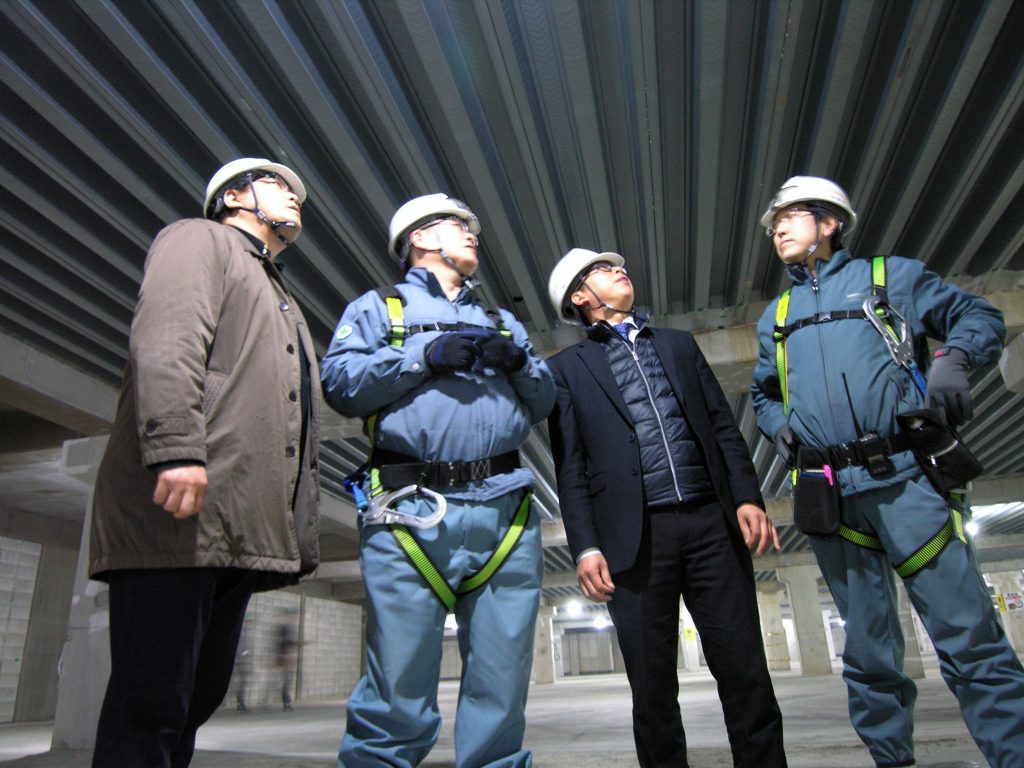
▲ 포스코건설이 경기도 평택시에 건설하고 있는 지제 지역주택조합아파트 지하주차장 천장(상부 바닥)에 시공한 D-데크 시설물을 꼼꼼히 살펴보고 있는 포스코 강건재마케팅실 고광호 과장과 포스코건설 유윤종 소장, 시공사인 NI스틸 홍순호 부장, 포스코건설 손용성 리더.(왼쪽부터)
관행적으로 콘크리트를 사용하는 바닥 데크를 포스코 강재로 바꾸는 것은 쉽지 않았다. 강건재업계는 시큰둥했다. 지금까지 콘크리트로도 잘해 왔는데 귀찮게 왜 바꾸냐는 반응이었다. 이때 NI스틸이 선뜻 도전에 나섰다. 평소 NI스틸은 모든 강건재 제품을 포스코 소재로 충당하면서, 포스코재에 대한 자부심이 대단했다. 합판으로 만든 거푸집을 하부에 받쳐 콘크리트를 부어 만드는 재래식 공법을 버리고 강재로 제작한 모듈형 합성 구조 공법으로 바꿨다. 아예 ‘D-데크’라는 브랜드를 새로 만들었다. 그리고는 포스코건설에 역 제안했다.
포스코건설도 적극 호응했다. D-데크의 장점이 눈에 보였다. 우선 아파트 설계도부터 다시 검토했다. 지하주차장에는 콘크리트 공법이 이미 적용돼 있었다. 시공 발주처인 주택조합과 평택시의 별도 승인도 받아야 했다. 행운이 따랐다. 발주처 사정으로 착공이 늦어지고 있어 주택조합도 평택시도 공사단축을 바라고 있었다. 포스코건설 유윤종 소장은 “새로운 공법(D-데크)을 적용하면 공기도 단축되고 추가 비용도 발생하지 않는다고 설득했는데 그게 주효했다.” 실제 공기가 적게는 40일에서 60일까지 단축됐다. 조합도, 지자체도 고마워했다.
NI스틸 홍순호 부장은 “포스코 소재가 좋은 것은 건설업계에선 다 안다. 장기적으로는 포스코 소재를 이용하면 시공작업이 쉽고 편해서 공사비 절감에도 큰 도움이 되기 때문이다. 하지만 눈앞의 이익 때문에 값싼 수입품을 찾는 국내 데크 제작사들의 현실이 솔직히 마음 아프다”라고 안타까워했다.
포스코는 그룹사 차원의 협업을 강화해 설계에서 제작, 일선 시공 현장까지 포스코의 건설용 강건재를 확산 적용할 수 있도록 마케팅 활동을 강화하고 있다. 발주량이 문제가 아니다. 건설현장에서 기존의 목재나 콘크리트 등은 철강으로, 수입품은 포스코 강재로 바꾸는 마케팅 활동을 전방위적으로 펼치고 있다고 소개한 고광호 과장은 “강건재 WTP 발주 3천 톤에는 일반재 3만 톤과 맞먹는 노력과 가치가 반영돼 있다”라고 강조했다.
포스코는 ‘비즈니스 파트너와 가치를 함께 만든다(Business With POSCO)’는 비전 아래, 세계 최고의 프리미엄 제품과 서비스를 제공하고자 R&D를 혁신하고 차별화된 솔루션을 꾸준히 개발해나가고 있다. 특히 친환경적이고 안전한 미래자동차 ‘Neo Mobility’, 모두가 꿈꾸는 안전한 미래도시 ‘Mega City’ 그리고 깨끗하고 무한한 에너지 ‘Eco Energy’로 구성된 3대 메가트랜드에 부응해, 포스코의 WTP가 핵심적인 역할을 할 수 있도록 고객의 현장에서 끊임없이 니즈를 발굴해나갈 계획이다.